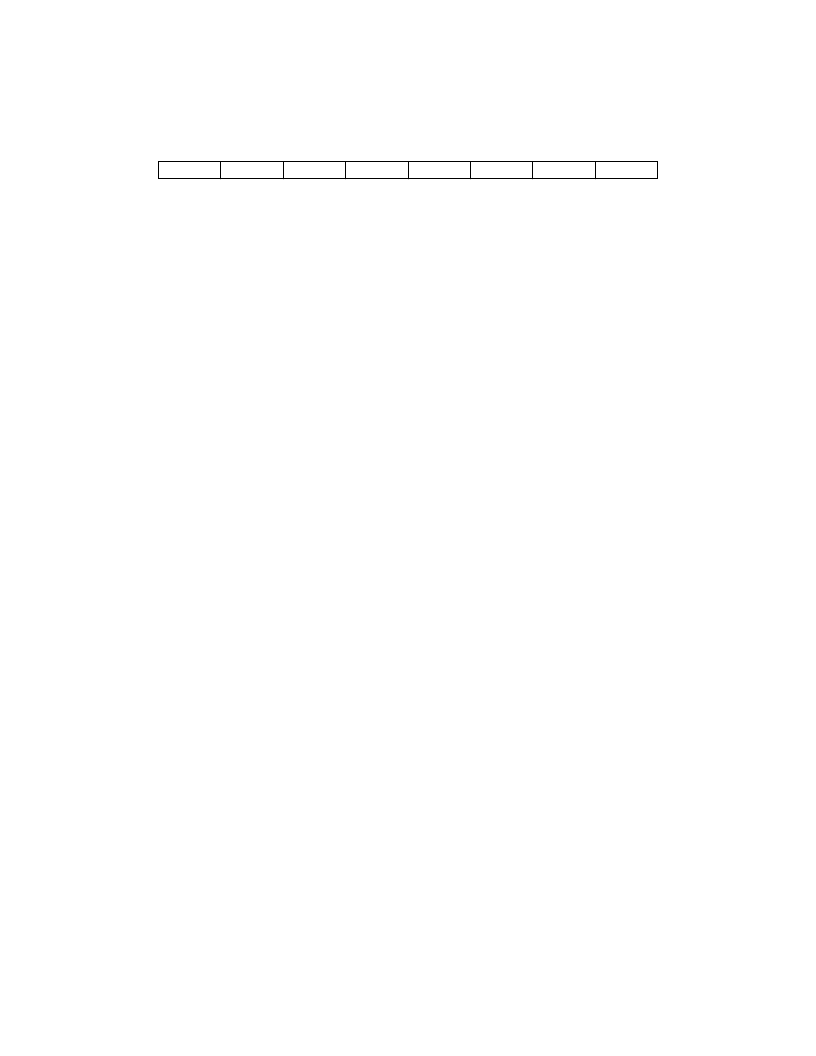
MOTOROLA
12-14
ANALOG-TO-DIGITAL CONVERTER SYSTEM
M68HC11
REFERENCE MANUAL
ADPU and CSEL control bits affect the A/D converter system.
The CSEL control bit also selects an alternate clock source for the on-chip EEPROM
charge pump. This charge pump is separate from the A/D charge pump, but both
pumps are selected with the CSEL control bit. In the case of the A/D charge pump,
CSEL needs to be one when the E clock is too slow to assure that the successive-ap-
proximation sequence will finish before any significant charge loss. In the case of the
EEPROM, the efficiency of the charge pump is at issue. More details on EEPROM
charge-pump efficiency are presented in
SECTION 4 ON-CHIP MEMORY
. When the
E clock is at or above 2 MHz, CSEL should always be zero; when the E clock is below
750 kHz, CSEL should almost always be one.
At E-clock frequencies between 750 kHz and 2 MHz, CSEL should be set to one for
EEPROM programming and erase operations so the EEPROM charge pump works
more efficiently; however, CSEL should be set to zero for A/D conversions to assure
highest A/D accuracy by reducing the effects of on-chip noise.
In most applications, switching CSEL on and off is not necessary. Instead, a trade-off
can usually be made on the basis of application requirements. For example, the addi-
tional A/D error attributable to internal noise when CSEL equals one is on the order of
±
1/2 LSB, which is acceptable in many applications.
12.2.3 MC68HC11A8 A/D System Control Logic
The A/D system on the MC68HC11A8 consists of a single successive-approximation
A/D converter, an input multiplexer to select one of 16 channels (including eight chan-
nels associated with pins on the MCU), and sophisticated control circuitry to configure
and control conversion activities. Four separate result registers are included with con-
trol logic that implements automatic conversion sequences on a selected channel four
times or on four channels (once each). Conversion sequences are configured to re-
peat continuously or to stop after one set of four conversions. An on-chip RC oscillator
is selected to allow normal operation of the A/D when very low MCU clock frequencies
are being used.
Figure 12-4
shows the timing for a sequence of four A/D conversions; the system E
clock is being used as the conversion clock, which is the normal case. The A/D con-
verter is dynamic in that the charge attained during the sample period will eventually
leak off the DAC capacitors. If the system E clock is slower than 750 kHz, an on-chip
RC oscillator should be selected as the A/D conversion clock source. The RC clock
source is selected by setting the CSEL control bit in the OPTION register. Since the
RC clock source is asynchronous to the MCU E clock, a synchronization delay is re-
quired at the end of each conversion in the sequence to prevent result-register up-
dates in the same part of the E-clock cycle where a read is taking place. A/D result
registers should not normally be used before the conversion complete flag (CCF) is
OPTION —
System Configuration Options
$1039
BIT 7
ADPU
0
6
5
4
3
2
1
BIT 0
CR0
0
CSEL
0
IRQE
0
DLY
1
CME
0
CR1
0
RESET:
0