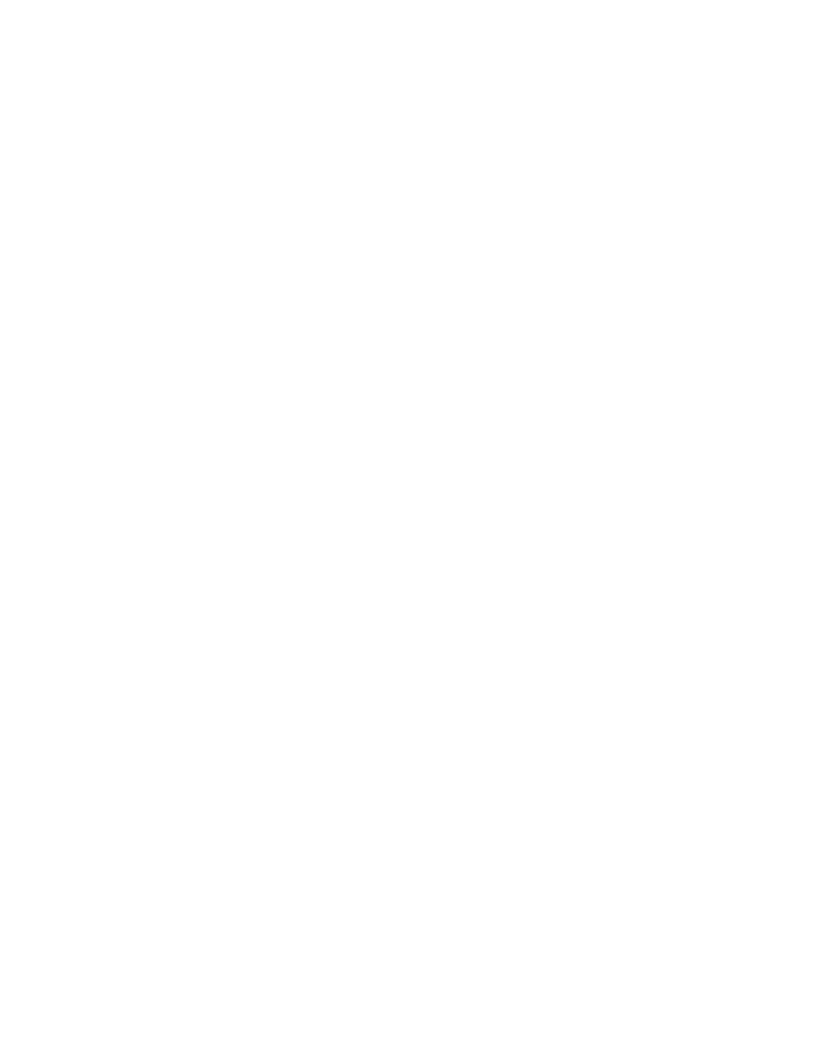
M68HC11
REFERENCE MANUAL
ANALOG-TO-DIGITAL CONVERTER SYSTEM
MOTOROLA
12-13
calculations. After the sample period, the shorting paths are disconnected, and the
conversion sequence proceeds as in the earlier examples. The 16-unit capacitor from
the plus input of the comparator to V
L
is not critical in terms of size because it is only
used to hold the plus input at V
TRIP
during the short conversion time.
12.2.2 A/D Charge Pump and Resistor-Capacitor (RC) Oscillator
A charge pump on the chip develops about 7 or 8 V, and this high voltage is used to
drive the gates of the analog switches in the input multiplexer and capacitor array. This
high gate voltage assures low source to drain impedance for analog signals up to and
including V
DD
. In fact, V
RH
can be somewhat higher than V
DD
(approximately 6 V), and
the converter will still yield good ratiometric results.
The A/D charge pump is disabled coming out of reset and is turned on by setting the
A/D power-up (ADPU) control bit in the OPTION control register before the A/D system
can be used. A delay is required after turning on ADPU to allow the charge pump and
comparator circuits to stabilize before using the converter system.
The charge-redistribution A/D process is a dynamic process in that the charge on the
capacitor array will eventually leak off. This capacitor array is part of an internal digital-
to-analog converter (DAC), which means the conversion process must be completed
within a reasonable time after the sample time ends. The other circuitry on the MCU
is static to allow very low clock frequencies, thus saving power. At bus frequencies (E
clock) below 750 kHz, the E clock should not normally be used as the A/D conversion
clock because there is a risk of error due to charge leakage at temperature extremes.
Laboratory characterization has indicated good performance at E-clock rates as low
as 10 kHz, but the specification has been guard banded against process variations.
An on-chip RC oscillator provides an alternate clocking source for the A/D system
when the E clock is running too slow to assure good conversions. This clock source is
selected by writing a one to the clock select (CSEL) control bit in the OPTION control
register. The A/D clock (E clock or RC oscillator depending on CSEL) drives the SAR
sequencer and the A/D charge pump. Some delay may be required after switching
clock sources, depending on their frequencies. The RC oscillator frequency varies with
processing but is typically about 2 MHz.
When the E clock is being used as the A/D clock source, the conversion sequence is
inherently synchronized to the main MCU clocks. Using the E clock has two advantag-
es over using the RC oscillator, which is asynchronous to system clocks. First, the
comparator output is sampled at relatively quiet times in the system clock cycle, thus
reducing the effects of internal MCU noise. When the RC oscillator is being used, there
is more error attributable to internal system clock noise. Second, result-register up-
dates automatically occur during a portion of the system clock cycle where reads do
not occur; thus, an update cannot interfere with a read. When the RC oscillator is used,
there is no conflict between updates and reads, but there is an additional synchroni-
zation delay imposed at the end of each channel conversion to allow for synchroniza-
tion to the system E clock.
The following illustration shows the OPTION control register for reference since the