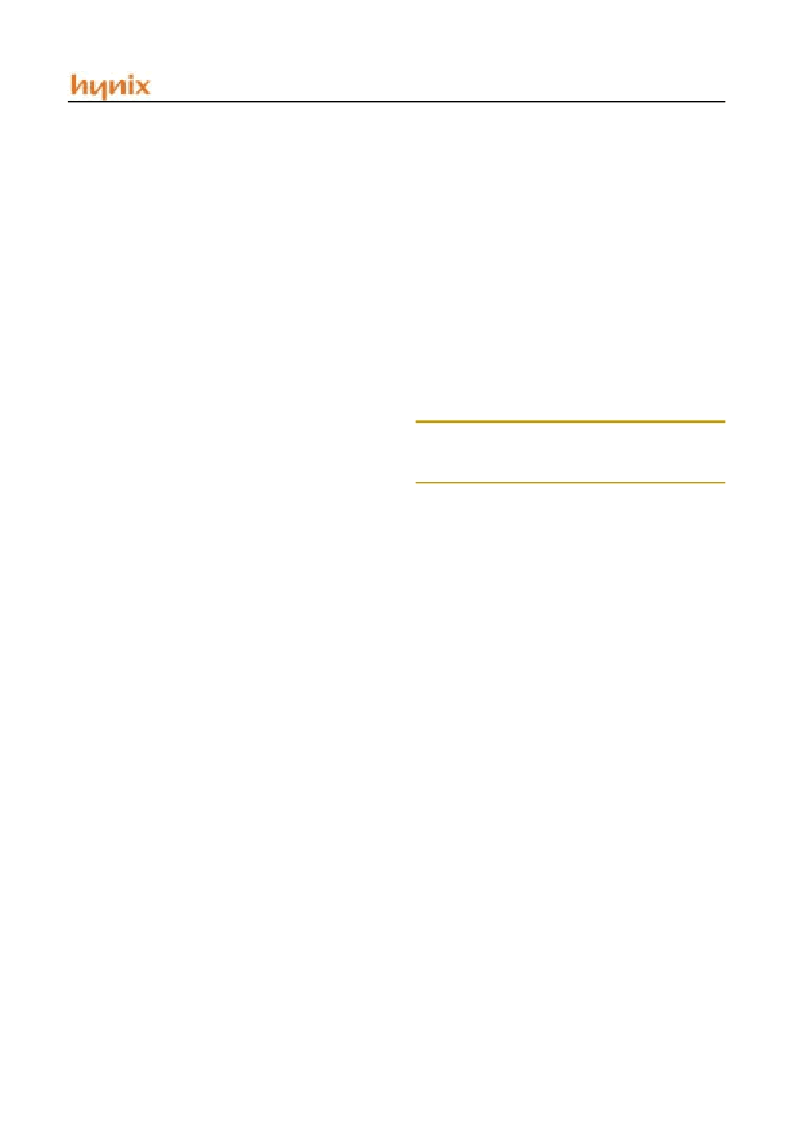
HMS77C2000/2001
Nov. 2002 Ver 1.1
45
13. IN-CIRCUIT SERIAL PROGRAMMING(ICSP) SPECIFICATIONS
13.1 PROGRAMMING THE HMS77C200X
The HMS77C2000 and HMS77C2001 can be programmed
using a serial method. Due to this serial programming, the
HMS77C2000 and HMS77C2001 can be programmed
while in the user’s system increasing design flexibility.
This programming specification applies to the
HMS77C2000 and HMS77C2001 devices in all packages.
13.1.1 Hardware Requirement
The HMS77C2000 and HMS77C2001 require two pro-
grammable power supplies, one for V
DD
(4.5V to 5.5V rec-
ommended) and one for V
PP
(11.25V to 11.75V).
Both supplies should have a minimum resolution of 0.25V.
13.1.2 Programming Mode
The programming mode for the HMS77C2000 and
HMS77C2001 allows programming of user program mem-
ory, special locations used for ID, and the configuration
word for the HMS77C2000 and HMS77C2001.
13.2 PROGRAM MODE ENTRY
The program/verify mode is entered by holding UP0, UP1
and the other pins(UP2, UP4, UP5) low while raising V
PP
pin from V
IL
to V
IHH
.
Once in this mode the user program memory and the test
program memory can be accessed and programmed in a se-
rial fashion. The first selected memory location is the con-
figuration word.
Incrementing the PC once (using the increment address
command) selects location 0x000 of the regular program
memory. Afterwards all other memory locations from
001
H
~1FF
H
(HMS77C2000), 001
H
~3FF
H
(HMS77C2001)
can be addressed by incrementing the PC.
If the program counter has reached the last user program
location and is incremented again, the on-chip special
EPROM area will be addressed.
(See Figure 13-2 to determine where the special EPROM
area is located)
13.2.1 Programming Method
The programming technique is described in the following
section. It is designed to guarantee good programming
margins. It does, however, require a variable power supply
for V
DD
.
Programming Method Details
- Perform blank check at V
DD
= V
DDMIN
. Report
failure.
The device may not be properly erased.
- Program location with pulses and verify after
each pulse at V
DD
= V
DDP
:
where V
DDP
= V
DD
range required during pro-
gramming (4.5V ~ 5.5V).
Programming / Verify Condition
V
PP
= 11.25V to 11.75V
V
DD
= V
DDP
= 4.5V to 5.5V
If location fails to program after “N” pulses, then report er-
ror as a programming failure.
Note:
Device must be verified at minimum and maximum
specified operating voltages as specified in the data
sheet.
- Once location passes “Step 2”, apply 3x over-
programming, i.e., apply 3 times the number of
pulses that were required to program the loca-
tion. This will guarantee a solid programming
margin. The over programming should be made
“software programmable” for easy updates.
- Program all locations.
- Verify all locations (using speed verify mode) at
V
DD
= V
DDMIN
.
- Verify all locations at V
DD
= V
DDMAX
.
System Requirement
Clearly, to implement this technique, the most stringent re-
quirements will be that of the power supplies:
-
V
PP
: V
PP
can be a fixed 11.25V to 11.75V
It must not exceed 13V to avoid damage to the
pin and should be current limited to approximate-
ly 100mA.
-
V
DD
: 4.5V to 5.5V with 0.25V granularity.
Since this method calls for verification at different
V
DD
values, a programmable V
DD
power supply
is needed.
-
Current Requirement
: 200mA maximum
Software Requirement
Certain parameters should be programmable (and there-
fore easily modified) for easy upgrade.
- Pulse Width