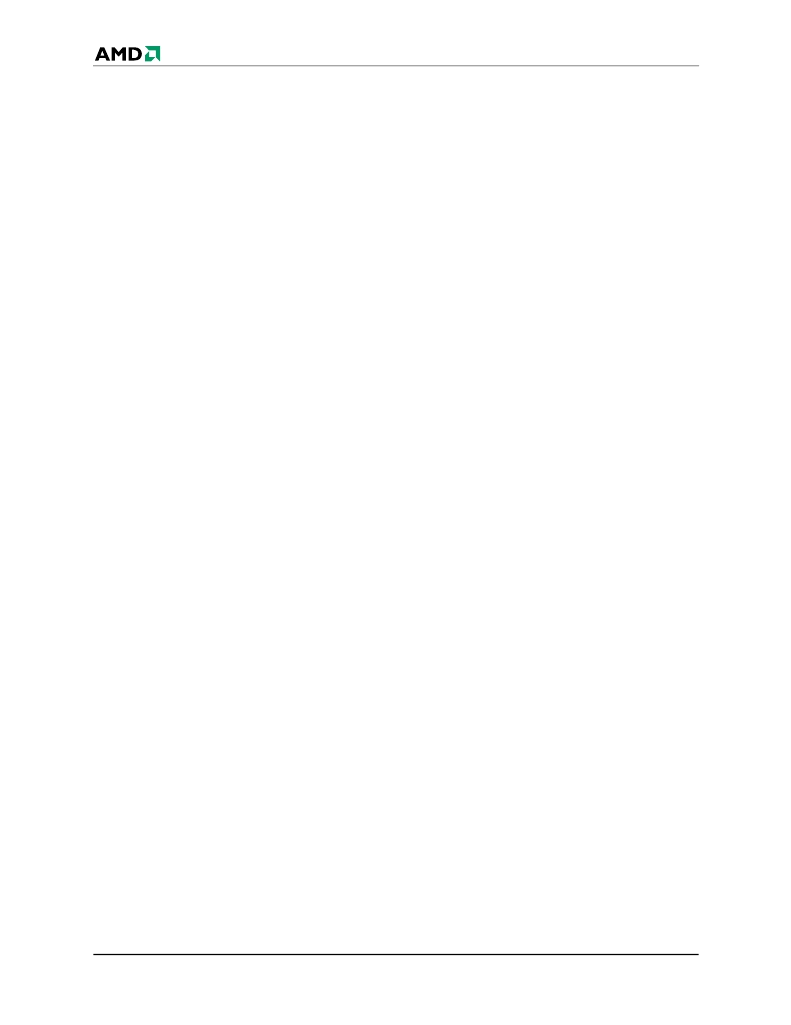
FBGA User’s Guide
62
Version 4.2, November 1, 2002
Materials
Most of the laminates for PCBs in the industry are produced using epoxy resins. The choice of epoxy
resin is made because of its outstanding electrical, mechanical, and thermal properties. FR-4 epoxy
fiberglass laminate is the standard for all high technology and professional electronic assemblies, and
is the material selected for this study.
Design Parameters
Pad defined land pattern for the CSPs was chosen in order to achieve a good interface between the
solder balls and the PCB pads. The circular pad has a diameter of 12 mils, and is dipped with eutectic
63Sn/37Pb solder with thickness of 0.5 to 0.8 mils. The clearance (or spacing) between solder mask
and pads is 3 mils; and the registration is +/- 2 mils. No solder mask is allowed on the pads. Liquid
photo imageable solder mask is coated over base Copper with maximum thickness of 3 mils. 5 mil
nominal trace width is used for all trace routing.
Assembly of Packages
The test boards were not panelized during assembly. Only one piece of board was on each panel.
Fixtures were used at all stages of the process, including printing. The boards were taped onto the
fixtures using Kapton tape. No clean process was used for this study because the stand off height for
CSPs is very low, and cleaning and drying under the CSP package could lead to contamination.
Solder Paste Screen Printing
DEK 265Lt screen printer with 300 mm metal squeegee was the equipment used for the solder paste
printing process. LR737 rosin, a no-clean paste from Alpha Metals was used for the study. It is
designed for stencil application in surface mounting process where post reflow cleaning is not
required. It has mesh size of –325, which is equivalent to a particle size of less than 45 μm diameter.
The key criteria of stencil performance are vertical wall straightness, wall smoothness and dimensional
precision. Laser cut stencils were used, since the laser cutting processes can produce stencils with
smooth and straight vertical walls.
While screen printing solder paste, the stencil thickness and aperture dimensions are combined to
achieve a balance between printing resolution and the avoidance of either starved solder joints or pad
bridging. The stencil was designed to have a thickness of 3 mils and aperture of 12 mils in this study.
During the solder printing process, visual inspection for smear, slump, missing, and bridging is
performed for each board. Paste height at random locations is measured through scanning laser
microscopy (LSM) for one of every five boards. The average paste height is controlled at 3.6 mils with
deviation of 0.3 mils.