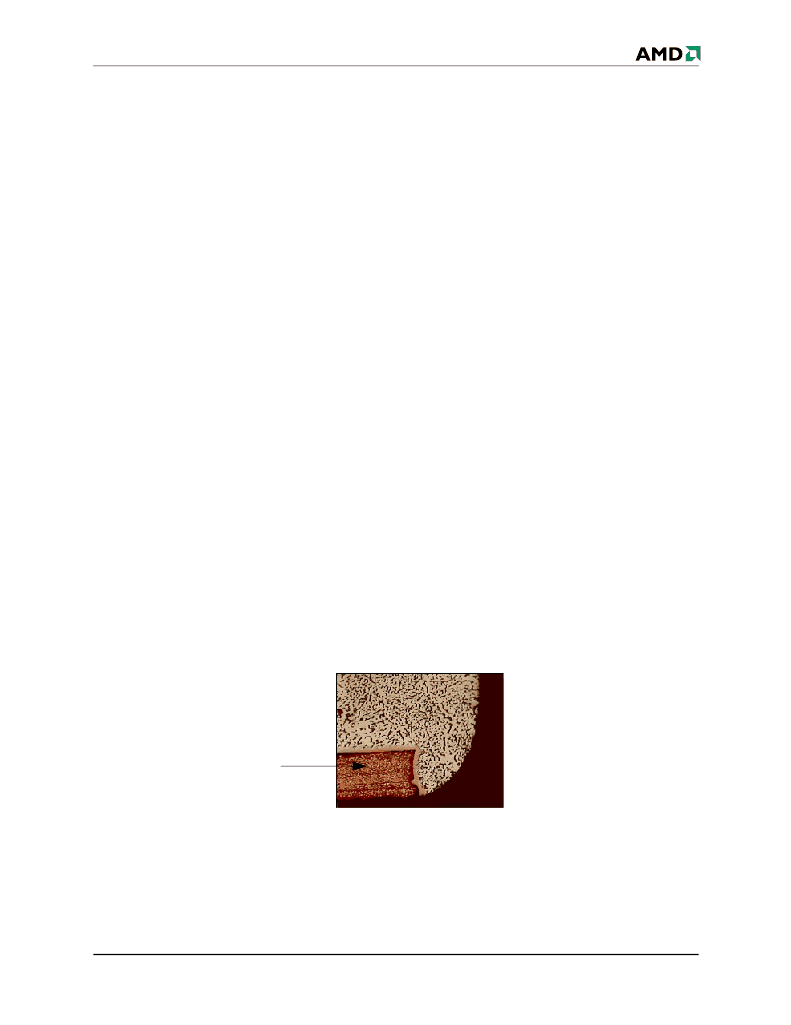
FBGA User’s Guide
Version 4.2, November 1, 2002
53
Chapter 7:
Board Design and Layout Considerations
General Design Considerations
One of the first decisions to be made when designing boards for chip scale packages is whether it will
be possible to use conventional PCB technology and design rules, or whether microvia technology will
be necessary. Recently, microvia HDI (High Density Interconnects) boards have been adopted in
several volume applications, particularly in cell-phones and camcorders, and the prices of microvia
boards have been falling quickly. HDI are defined as having vias with a diameter less than 0.006 inch
on pad size of 0.014 inch or smaller. However they are still more expensive. Measured on the basis of
price per unit area per metal layer, microvia boards are at least twice as expensive as high-density
conventional multilayer PCBs, even with blind and buried vias. Furthermore, there is also the question
of availability: it may not be easy to find suppliers with production capacity for microvia boards.
It is for this reason that a pitch of 0.8 mm has been chosen for AMD’s FBGA. As shown in the next
section, single-layer routing for Flash Memory FBGA can be accomplished with line and space widths
of 0.005 inch or more. Because of the relatively low lead count, this can be done in one layer, but if
desired, connections down to inner layers can be accomplished through interstitial vias.
Solder-Mask Defined Versus Non-Solder-Mask Defined
There has been much discussion about the relative merits of solder-mask defined (SMD) and non-
solder-mask defined (NSMD) lands for attaching area array packages such as conventional BGA and
fine pitch BGA. AMD’s FBGA can be used with either, but there are two important benefits of NSMD
pads. One is that smaller copper pads can be used, thus providing more generous clearance for the
routing channels. (Another is that the solder can wet around the sides of the pad during reflow (see
Figure 7-1) thus providing a stronger joint.)
Figure 7-1. Solder Wetting Around Pad During Reflow
Note that if the kind of wetting shown in Figure 7-1 is desired, it is important to provide sufficient
clearance of solder mask around the pad. The PCB supplier may consider the edge of the solder mask
touching the edge of the pad to be acceptable, however, this condition would prevent the solder from
completely wetting the side of the pad.
Copper attachment pad