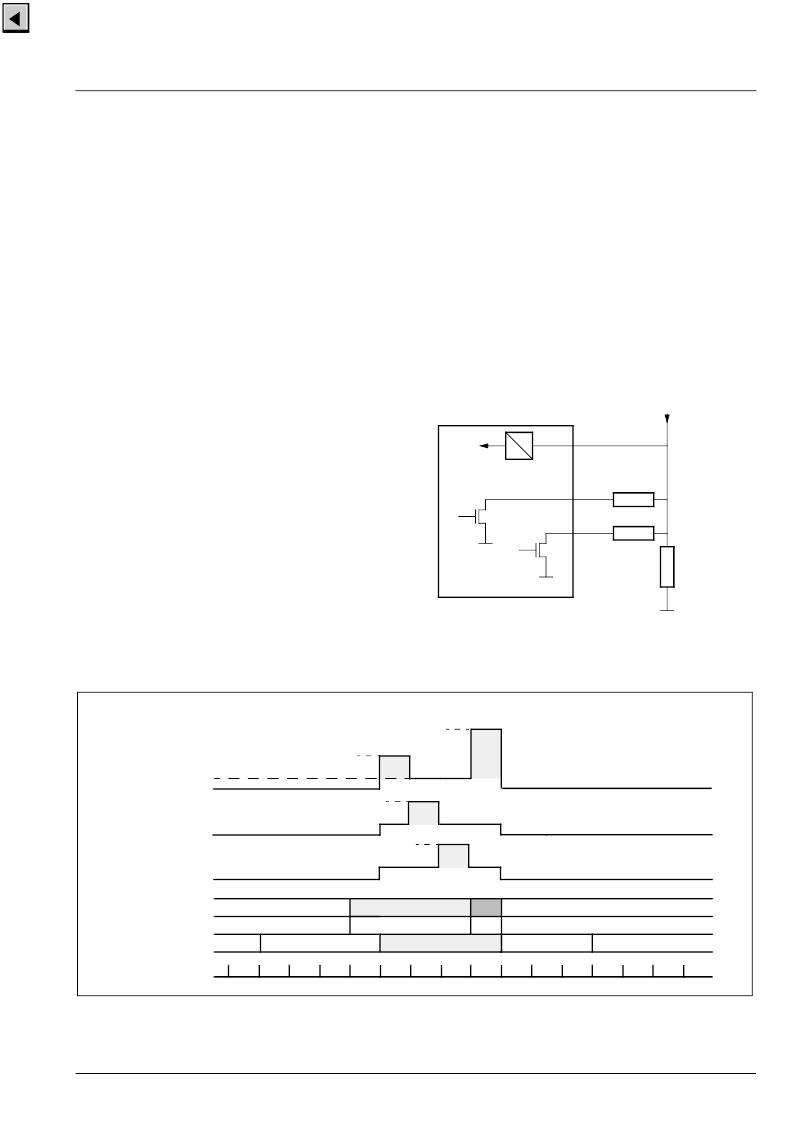
ADVANCE INFORMATION
VCT 38xxA
Micronas
25
2.11.Video Back-end
The digital RGB signals are converted to analog RGBs
using three video digital-to-analog converters (DAC)
with 10-bit resolution. An analog brightness value is
provided by three additional DACs. The adjustment
range is 40 % of the full RGB range.
Controlling the white-drive/analog brightness and also
the external contrast and brightness adjustments is
done via the Fast Processor, located in the front-end.
Control of the cutoff DACs is done via I
2
C bus regis-
ters.
Finally cutoff and blanking values are added to the
RGB signals. Cutoff (dark current) is provided by three
9-bit DACs. The adjustment range is 60 % of full scale
RGB range.
The analog RGB-outputs are current outputs with cur-
rent-sink characteristics. The maximum current drawn
by the output stage is obtained with peak white RGB.
An external half contrast signal can be used to reduce
the output current of the RGB outputs to 50 %.
2.11.1.CRT Measurement and Control
The display processor is equipped with an 8-bit
PDM-ADC for all measuring purposes. The ADC is
connected to the SENSE input pin, the input range is 0
to 1.5V. The bandwidth of the PDM filter can be
selected; it is 40/80 kHz for small/large bandwidth set-
ting. The input impedance is more than 1 M
.
Cutoff and white-drive current measurement are car-
ried out during the vertical blanking interval. They
always use the small bandwidth setting. The current
range for the cutoff measurement is set by connecting
a sense resistor to the MADC input. For the white-drive
measurement, the range is set by using another sense
resistor and the range select switch 2 output pin
(RSW2). During the active picture, the minimum and
maximum beam current is measured. The measure-
ment range can be set by using the range select
switch 1 pin (RSW1) as shown in Fig. 2–19 and Fig. 2–
20. The timing window of this measurement is pro-
grammable. The intention is, to automatically detect
letterbox transmission or to measure the actual beam
current. All control loops are closed via the external
control microprocessor.
Fig. 2–19:
MADC range switches
Fig. 2–20:
MADC measurement timing
A
D
MADC
Beam Current
SENSE
RSW1
RSW2
R3
R2
R1
Lines
active measure-
ment resistor
ultra black
black
R1
||
R2
||
R3
RSW1=on, RSW2=on
PICTURE MEAS.
PMSO
R1
CB + IBRM
B
cutoff
CR + IBRM + WDRV
WDR
CR + IBRM
CG + IBRM
G
cutoff
R
cutoff
R1
||
R3
=on
R1
||
R2
||
R3
RSW1=on, RSW2=on
PICTURE MEAS.
PMST
TML
TUBE MEASUREMENT
R
G
B
white
drive
R