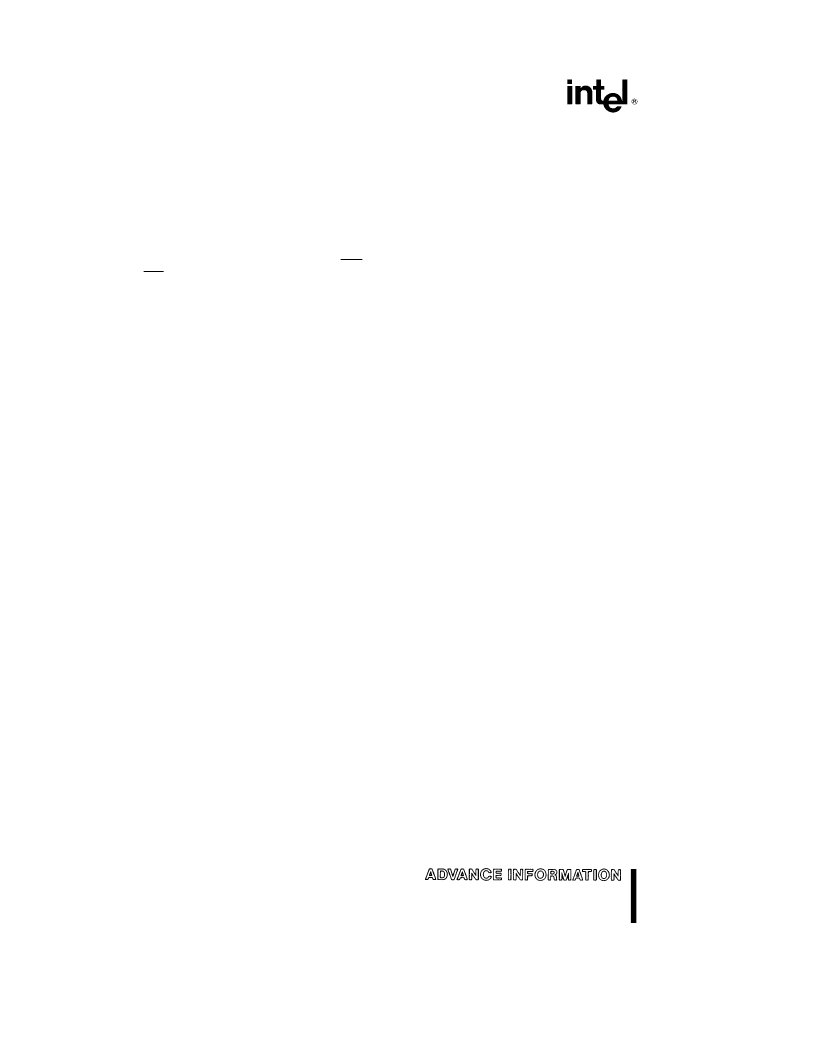
82595FX
10.4.2 TPE CIRCUIT
The 82595FX provides the line drivers and receivers
needed to directly Fabinterface to the TPE analog
filter network. The TPE receive section requires a
100
X
termination resistor, a filter section (filter, iso-
lation transformer, and a common mode choke) as
described by the 10BASE-T 802.3i-1990 specifica-
tion.
The TPE transmit section is implemented by con-
necting the 82595FX’s four TPE outputs (TDH, TDH,
TDL, TDL) to a resistor summing network to form the
differential output signal. The parallel resistance of
R5 and R6 sets the transmitters maximum output
voltage, while the difference (R5
b
R6)/R5
a
R6), is
used to reduce the amplitude of the second half of
the fat bit (100 ns) to a predetermined level. This
predistortion reduces line overcharging, a major
source of jitter in the TPE environment. The output
of the summing network is then fed into the above
mentioned filter and then to the 10BASE-T connec-
tor (RJ-45). Analog Front End solutions can be pur-
chased in a single-chip solution from several manu-
facturers. The solution described in this data sheet
uses the Pulse Engineering (PE65434) AFE.
10.4.3 LED CIRCUIT
The 82595FX’s internal LED drivers support four
LED indicators displaying node status and activity
(i.e., Transmit data, receive data, collisions, link in-
tegrity, polarity correction, and port (TPE/AUI). To
implement the LED indicators, connect the LED driv-
er output to an LED in series with a 510
X
resistor
tied to V
CC
. Each driver can sink up to 10 mA of
current with an output impedance of less than 50
X
.
10.5 Layout Guidelines
10.5.1 GENERAL
The analog section, as well as the entire board itself,
should conform to good high-frequency practices
and standards to minimize switching transients and
parasitic interaction between various circuits. To
achieve this, follow these guidelines:
Make power supply and ground traces as thick and
as short as possible. This will reduce high-frequency
cross coupling caused by the inductance of thin
traces.
Connect logic and chassis ground together, only at
one point on the fabDnear the connection to system
ground.
You must connect all V
CC
pins to the same power
supply and all V
SS
pins to the same ground plane.
Use separate decoupling per power-supply/ground
pin.
Close signal paths to ground as close as possible to
their sources to avoid ground loops and noise cross
coupling.
10.5.2 CRYSTAL
The crystal should be adjacent to the 82595FX and
trace lengths should be as short as possible. the X1
and X2 traces should be as symmetrical as possible.
10.5.3 82595FX ANALOG DIFFERENTIAL
SIGNALS
The differential signals from the 82595FX to the
transformers, analog front end, and the connectors
should be symmetrical for each pair and as short as
possible.
The differential signals should also be isolated from
the high speed logic signals on the same layer as
well as on any sublayers of the PCB.
Group each of the circuits together, but keep them
separate from each other. Separate their grounds.
In layout, the circuitry from the connectors to the
filter network should have the ground and power
planes removed from beneath it. This will prevent
ground noise from being induced into the analog
front end.
All trace bends should not exceed 45 degrees.
10.5.4 DECOUPLING CONSIDERATIONS
Four 0.1
m
F ceramic capacitors should be used.
Place one on each side in the center of the I.C. adja-
cent to the 82595FX. Connect the capacitors direct-
ly to the V
CC
pins and ground planes of the
82595FX.
34