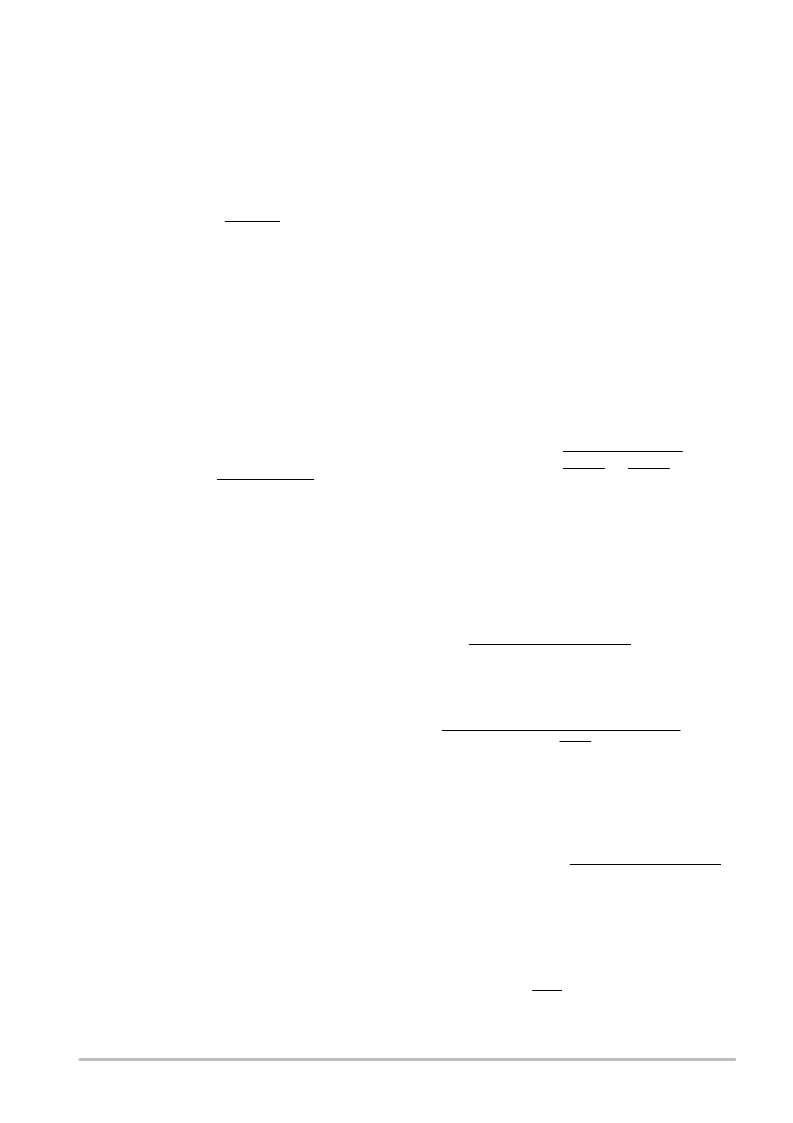
NCP5218
http://onsemi.com
24
V
DDQ
is finished. The C
ss
will continue to charge up until
it reaches about 2.5 V to 3.0 V.
The soft
start time t
ss
can be programmed by the
soft
start capacitor according to the following equation:
0.8
tss
Css
Iss
(eq. 40)
Ceramic capacitors with low tolerance and low
temperature coefficient, such as B, X5R, X7R ceramic
capacitors are recommended to be used as the C
SS
. Ceramic
capacitors with Y5V temperature characteristic are not
recommended.
Soft
Start of VTT Active Terminator
The VTT source current limit is used as a constant
current source to charge up the VTT output capacitor
during VTT soft
start. Besides, the VTT source current
limit is reduced to about 1.0 A for 128 internal clock cycles
to minimize the inrush current during VTT soft
start.
Therefore, the VTT soft
start time t
SSVTT
can be estimated
by the equation:
COUTVTT
tSSVTT
VTT
ILIMVTSS
(eq. 41)
where C
OUTVTT
is the capacitance of VTT output capacitor
and I
LIMVTSS
is the VTT soft
start source current limit.
Boost Supply Diode and Capacitor
An external diode and capacitor are used to generate the
boost voltage for the supply of the high
side gate driver of
the bulk regulator. Schottky diode with low forward
voltage should be used to ensure higher floating gate drive
voltage can be applied across the gate and the source of the
high
side MOSFET. A Schottky diode with 30 V reverse
voltage and 0.5 A DC current ratings can be used as the
boost supply diode for most applications. A 0.1
F to
0.22
F ceramic capacitor should be sufficient as the boost
capacitor.
VTTI Input Power Supply for VTT and VTTR
Both VTT and VTTR are supplied by VTTI for sourcing
current. VTTI is normally connected to the VDDQ output
for optimum performance. If VTTI is connected to VDDQ,
no bypass capacitor is required to add to VTTI since the
bulk capacitor at VDDQ output is sufficiently large.
Besides, the maximum load current of VDDQ is the sum of
I
VDDQ(max)
and I
VTT(max)
when making electrical design
and components selection of the VDDQ buck regulator.
VTTI can also be connected to an external voltage source.
However, extra power dissipation will be generated from
the internal VTT high
side MOSFET and more
heatsinking is required if the external voltage is higher than
VDDQ. Whereas, the headroom will be limit by the R
DS(on)
of the VTT linear regulator high
side MOSFET, and the
maximum VTT output current with VTT within regulation
window will also be reduced if the external voltage is lower
than VDDQ. Besides, the VTTI pin input must be bypassed
to VTTGND with at least a 10
F capacitor if external
voltage source is used.
Design Example
A design example of a V
DDQ
bulk converter with the
following design parameters is shown below:
DDR2 V
DDQ
bulk converter design parameters:
1. Input voltage range: 7.0 V to 20 V.
2. Nominal V
OUT
: 1.8 V.
3. Static tolerance: 2% (
4. Transient tolerance:
5. Maximum output current: 10 A
(I
VDDQ(max)
= 8.0 A, I
VTT(max)
= 2.0 A).
6. Load transient step: 1.0 A to 8.0 A.
7. Switching frequency: 400 kHz.
8. Bandwidth: 100 kHz.
9. Soft
start time: 400 s.
a. Calculate input capacitor rms ripple current rating and
voltage rating:
36 mV).
100 mV.
ICIN(RMS)
10 A
1.836 V
8.0 V
1.836 V
8.0 V
2
4.2 A
(eq. 42)
VCIN(rating)
20
1.25 V
25 V
(eq. 43)
Therefore, two 10 F 25 V ceramic capacitors with 1210
size in parallel are used.
b.Calculate inductance, rated current and DCR of
inductor:
First, suppose ripple current is 0.3 times the maximum
output current, such that:
(20 V
1.836 V)
1.836 V
0.3
10 A
20 V
Second, the overshoot requirement at load release is then
considered and supposes two 220 F capacitors in parallel
are used as an initially guess, such that:
1.836 V)2
(1.836 V)2)
7 A
2
L
400 kHz
1.39 H
(eq. 44)
L
440 F
((100 mV
0.3
7 A
2
2.56 H
(eq. 45)
Thus, inductors with standard inductance values of
1.5 H, 1.8 H and 2.2 H can be used. As a trade
off
between smaller overshoot and better efficiency, the
average value of 1.8 H inductor is selected.
Then, the maximum rated DC current is calculated by:
IL(rated)
1.2
10 A
(20 V
1.836 V)
2
1.8 H
1.836 V
400 kHz
20
(eq. 46)
13.39 A
Therefore, inductor with maximum rated DC current of
14 A or larger can be used.
Finally, the DCR of inductor is 2.0 m per H of
inductance as a rule of thumb, then:
2 m
1 H
DCR
1.8 H
3.6 m
(eq. 47)