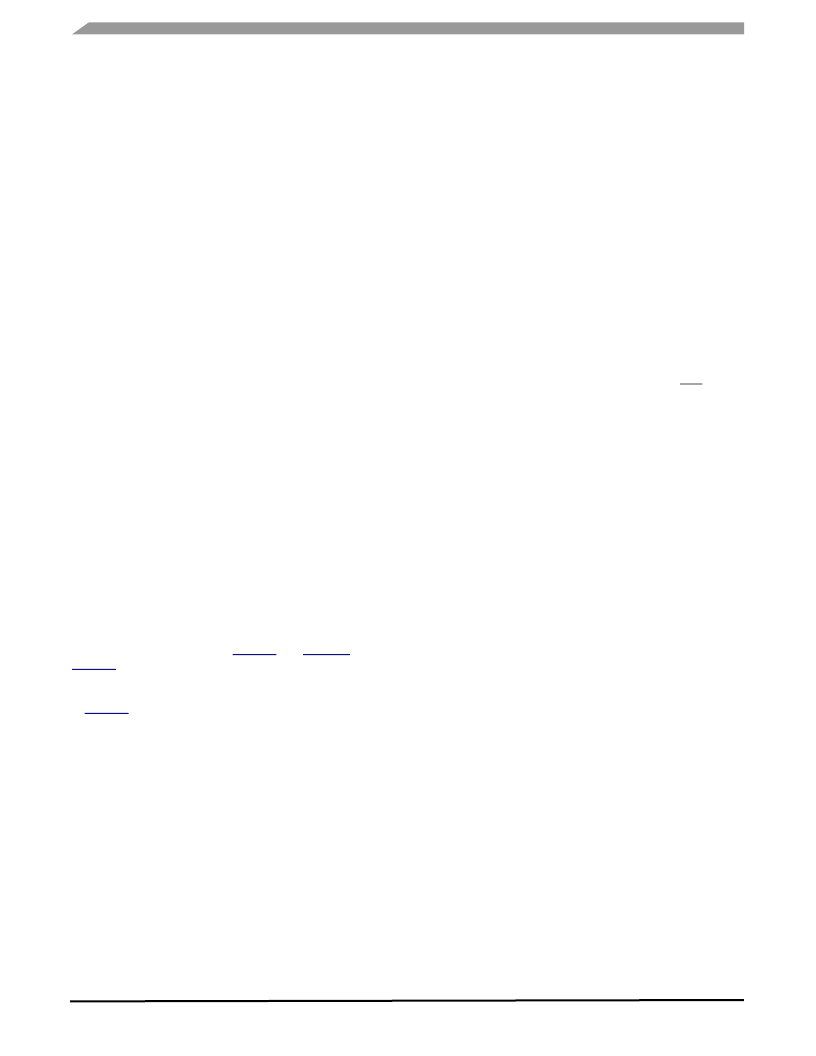
Analog Integrated Circuit Device Data
Freescale Semiconductor
32
33976
FUNCTIONAL DEVICE OPERATION
STATE MACHINE
A pointer that is not on a full step location or that is in
magnetic alignment prior to the RTZ event may cause a false
RTZ detection. More specifically, an RTZ event beginning
from a non-full step position may result in an abbreviated
integration value potentially interpreted as a stalled pointer.
Advancing the pointer by at least 12 microsteps clockwise (if
PE7 = 0) to the nearest full step position (e.g., 0, 6, 12, 18,
24, etc.) prior to initiating an RTZ ensures the magnetic fields
line up and increases the chances of a successful pointer
stall detection. It is important that the pointer be in a static, or
commanded, position before starting the RTZ event.
Because the time duration and the number of steps the
pointer moves prior to reaching the commanded position can
vary depending upon its status at the time a position change
is communicated, the master should assure sufficient
elapsed time prior to starting an RTZ. If an RTZ is desired
after first enabling the outputs or after forcing a reset of the
device, the pointer should first be commanded to move
12 microsteps clockwise to the nearest full step location.
Because the pointer was in a static position at default, the
master could determine the number of microsteps the device
has taken by monitoring and counting the MOV0. MOV1
device status bit transitions to confirm the pointer is again in
a static position. Alternatively, the user could monitor the
device status bits CMD1 and CMD2.
It should be pointed out that the flux value, for an ideal
motor with the coils perfectly aligned at 90°, will vary little
from full step to full step if all other variables (e.g.,
temperature) are held constant. The full steps are evenly
spaced which results in equidistant movement as the motor
is full stepped.
In comparison, motors that have coils aligned at a 60°
angle will result in two distinct flux values as the coils are
driven in the same full step fashion. This lack of symmetry in
the measured flux is due to the difference in the electrical
angles between full steps. In other words, the distance that
the rotor moves changes from full step to full step. This
difference can be observed in
Figure 8
and
Table 29
. In
Figure 8
, where PE6 = 0, the difference in microsteps
between alternating full steps (one coil at maximum current
while the other is at zero) is always six. In contrast, as seen
in
Figure 8
, where PE6 = 1, the difference in microsteps
between full steps of the 60° coils alternates between four
and eight. These expected differences need to be taken into
account when setting the RTZ threshold.
Only one gauge at a time can be returned to the zero
position. The gauge not returning to zero can continue to be
controlled. An RTZ should not begin until the gauge to be
calibrated is at a static position and its pointer is at a full step
position. An attempt to calibrate a gauge while the other is in
the process of an RTZ event is ignored by the device. In most
applications of the RTZR command, it is possible to avoid a
visually obvious sequential calibration by first bringing the
pointers back close to their previous zero positions, then re-
calibrating them sequentially.
After completion of an RTZ, the 33976 automatically
assigns the zero-step position to the full step position at the
end-stop location. Because the actual zero position could lie
anywhere within the full step where the zero was detected,
the assigned zero position could be within a window of ±0.5
degree. An RTZ can be used to detect stall, even if the
pointer already rests on the end stop when an RTZ sequence
is initiated. However, it is recommended the pointer be
advanced by at least 12 microsteps to the nearest full step
prior to initiating the RTZ.
RTZ OUTPUT
During an RTZ event the non-driven coil is analyzed to
determine the state of the motor. The 33976 multiplexes the
coil voltages and provides the signal from the non-driven coil
to the RTZ pin.
DEFAULT MODE
Default mode refers to the state of the 33976 after an
internal or external reset prior to SPI communication. An
internal reset occurs during V
DD
power-up or if V
PWR
falls
below 4.0 V. An external reset is initiated by the
RST
pin
driven to a logic [0]. With the exception of the RTZCR full step
time and the RMPSEL Register values, all of the specific pin
functions and internal registers will operate as though all of
the addressable configuration register bits were set to
logic [0]. This means, for example, all of the outputs will be
disabled after a power-up or external reset, and SO flag OD6
and OD8 are set, indicating an undervoltage event. Anytime
an external reset is exerted and the default is restored, all
configuration parameters (e.g., clock calibration, maximum
speed, RTZ parameters, etc.) are lost and must be reloaded.
FAULT LOGIC REQUIREMENTS
The 33976 device indicates each of the following faults as
they occur:
Overtemperature fault
Undervoltage V
PWR
Overvoltage V
PWR
Clock out of spec
These fault bits remain enabled until they are clocked out
of the SO pin with a valid SPI message.
Overcurrent faults are not reported directly; however, it is
likely an overcurrent condition will become a thermal issue
and be reported.
Overtemperature Fault Requirements
The 33976 incorporates overtemperature protection
circuitry, which shuts off the affected gauge driver when
excessive temperatures are detected. In the event of a
thermal overload, the affected gauge driver is automatically
disabled. The overtemperature fault is flagged via the OT0
and/or OT1 device status bits. The indicating flag continues
to be set until the affected gauge is successfully re-enabled,
provided the junction temperature has fallen to a temperature
below the hysteresis level.