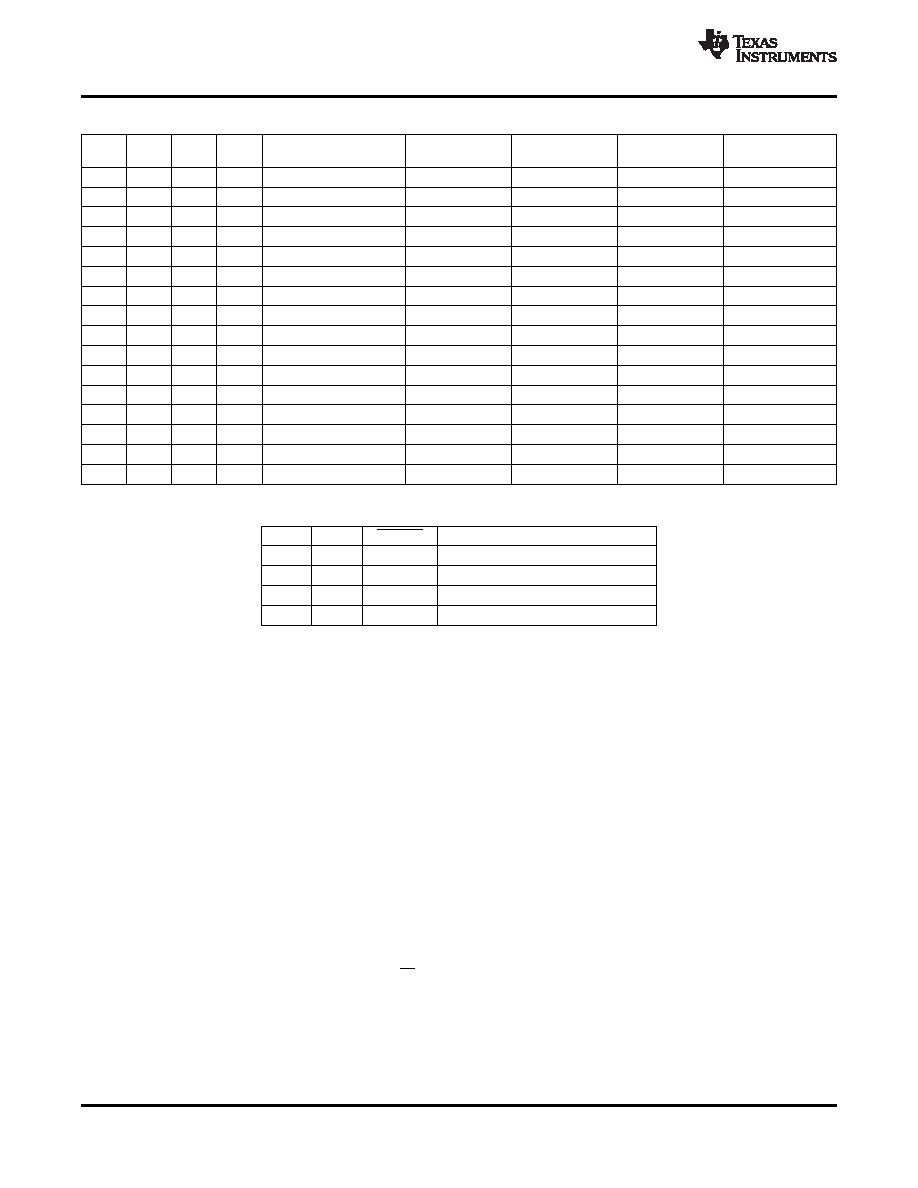
Start Conversion/Write Cycle
SBAS454 – DECEMBER 2008 ........................................................................................................................................................................................... www.ti.com
Table 1. Possible Input Configurations
REFERENCE
C3
C2
C1
C0
FUNCTION
INPUT TO ADC
X DRIVERS
Y DRIVERS
MODE
0
Measure TEMP0
TEMP0
Off
Single ended
0
1
Measure VBAT1
VBAT1
Off
Single ended
0
1
0
Measure IN1
IN1
Off
Single ended
0
1
Reserved
—
Single ended
0
1
0
Measure TEMP1
TEMP1
Off
Single ended
0
1
0
1
Measure VBAT2
VBAT2
Off
Single ended
0
1
0
Measure IN2
IN2
Off
Single ended
0
1
Reserved
—
Single ended
1
0
Activate X– Drivers
—
On
Off
Differential
1
0
1
Activate Y– Drivers
—
Off
On
Differential
1
0
1
0
Activate Y+, X– Drivers
—
X– On
Y+ On
Differential
1
0
1
Reserved
—
Differential
1
0
Measure X Position
Y+
On
Off
Differential
1
0
1
Measure Y Position
X+
Off
On
Differential
1
0
Measure Z1 Position
X+
X– On
Y+ On
Differential
1
Measure Z2 Position
Y–
X– On
Y+ On
Differential
Table 2. Power-Down Bit Functions
PD1
PD0
PENIRQ
DESCRIPTION
0
Enabled
Power-down between conversions
0
1
Disabled
Internal reference off, ADC on
1
0
Enabled
Internal reference on, ADC off
1
Disabled
Internal reference on, ADC on
The internal reference voltage can be turned on or off independently of the ADC. This can allow extra time for
the internal reference voltage to settle to its final value prior to making a conversion. Allow this extra wakeup time
if the internal reference was powered down. Also note that the status of the internal reference power down is
latched into the part (internally) when a Stop or repeated Start occurs at the end of a command byte (see
Figure 14 and
Figure 16). Therefore, to turn off the internal reference, an additional write to the TSC2003 with
PD1 = 0, is required after the channel has been converted.
It is recommended to set PD0 = 0 in each command byte to get the lowest power consumption possible. If
multiple X-, Y-, and Z-position measurements are done one right after another, such as when averaging, PD0 = 1
leaves the touch screen drivers on at the end of each conversion cycle.
M: Mode bit. If M is 0, the TSC2003 is in 12-bit mode. If M is 1, 8-bit mode is selected.
X: Don’t care
When the TSC2003 powers up, the power-down mode bits need to be written to ensure that the part is placed
into the desired mode to achieve lowest power. Therefore, immediately after power-up, a command byte should
be sent which sets PD1 = PD0 = 0, so that the device is in the lowest power mode, powering down between
conversions.
A conversion/write cycle begins when the master issues the address byte containing the slave address of the
TSC2003, with the eighth bit equal to a 0 (R/W = 0), as shown in
Figure 12. Once the eighth bit has been
received, and the address matches the A1–A0 address input pin setting, the TSC2003 issues an acknowledge.
Once the master receives the acknowledge bit from the TSC2003, the master writes the command byte to the
slave (see
Figure 13). After the command byte is received by the slave, the slave issues another acknowledge
bit. The master then ends the write cycle by issuing a repeated Start or a Stop condition, as shown in
Figure 14.20
Copyright 2008, Texas Instruments Incorporated