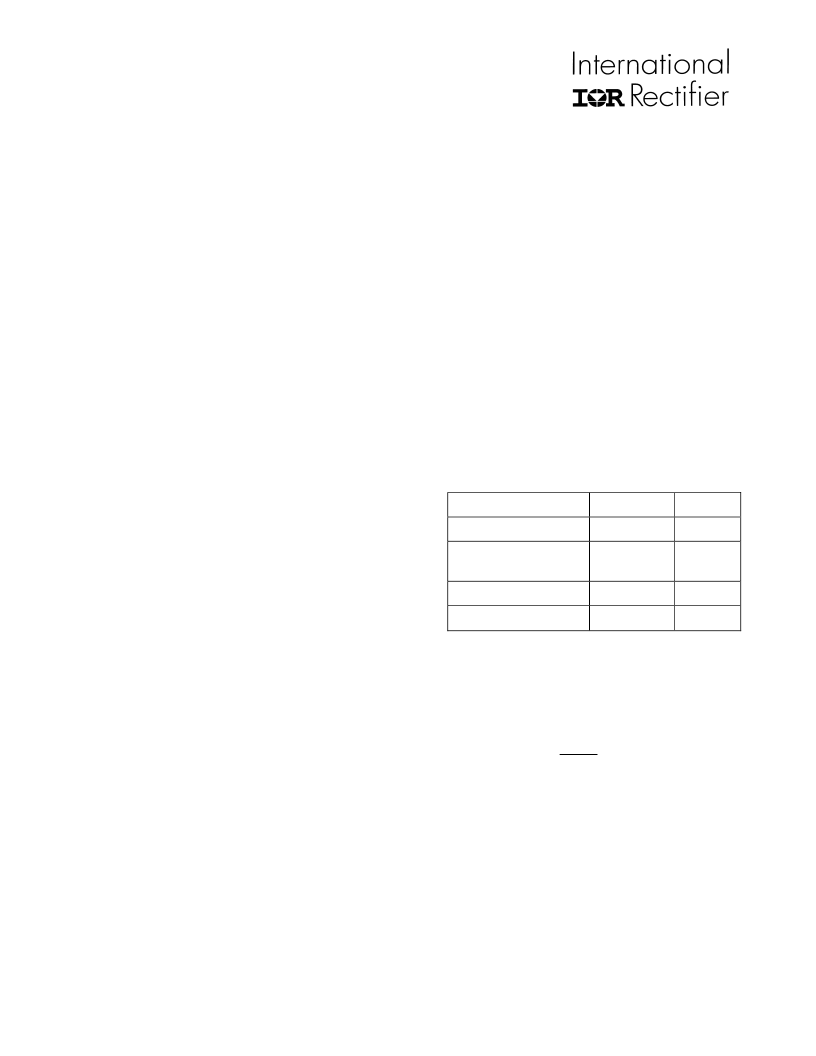
www.irf.com
14
PIIPM25P12B008
I27147 01/03
same linear regulator as a starting point for all
reference voltages. In fact if the 5V linear
regulator drifts in temperature or time, then all
references (even the 3.30V being this a simple
partitioning) follow in track and still keep the
overall chain precision. The trimming is then
done only once, in a single point of the
measuring chain, that is the conditioning op-amp
collecting the current sensing ICs signal as will
then be described in the following chapter.
3. Current sensing interfaces, over-current
protections and signal conditioning.
This block is the real critical point of the system.
Current measuring performances directly impact
on motor control performances in a servo
application: errors in current evaluation, delay in
its measuring chain or poor overall precision of
the system, such as scarce references or lower
number of significant A/D bits, inevitably results
in unwanted trembling and unnatural noise
coming from the motor while running at lower
speed or at blocked shaft conditions.
In the PI-IPM25P12B008 the current sensing
function is done through three sensing resistors
dropout measurement, one on each output phase,
with the benefit of a lower area and somewhat a
lower cost compared to the well-known Hall
effect devices. This solution has the added value
of having the shunts element embedded in the
power module with all Kelvin connections
available, avoiding any noise due to long routing
of power paths.
As the block schematic on page 2 shows, the
voltage across each sensing resistor is applied,
through an anti-aliasing 400kHz filter, at the
input of a current sense IC and then to a signal
conditioning circuit.
Though the block schematic here shows an Op-
Amp plus an external passive filter this is simply
realized implementing a VCVS cell (i.e. a
Constant Gain or Sallen – Key cell) configured
so that the offset and gain is easily trimmed by
three on board resistors. The filter implemented
is a second order Bessel with 5.5kHz pole
frequency, the reason for this is that this type of
polynomials are calculated with the aim of
having a constant group delay within the pass-
band frequencies, thus giving the minimum
waveform distortion to the output signal up to
almost twice the filter pole. In other words we
could also say that the group delay of the signal
chain from the sensing resistor up to the ADC
input of the DSP is constant from 0 to 5.5kHz.
Signal outputted from the overall chain has a 0 to
+3.30V dynamic, with a sensing resistor of
4mohms the input measured current range is +/-
50A then we have a situation as follows:
=
V
A
V
A
V
A
30
.
50
65
.
00
.
+
0
50
=
=
Summing
performances are shown in the following table:
up
our
current
measurements
The “2406A” DSP has a 10bit ADC,
consequently the PI-IPM25P12B008 has a
minimum
appreciable
approximately:
current
step
of
Α
=
=
0976
.
2
50
10
*
2
LSB
that is:
mA
LSB
1
98
The over current protection is provided also
through the current sensing ICs, the related fault
signal is activated when a 250mV voltage across
sensing pins is detected, this means an over-
current detection level of approximately 25%.
The delay of this line is around 3
μ
s, fast enough
to let the DSP react within the 10
μ
s IGBTs short
circuit rating, thus providing full device
protection for any phase-to-ground and phase-to-
PI-IPM Current sensing chain typical
performances
Value
Units
current range
+/- 50
A
Gain and Offset
precision
+/- 1.8
%
bandwidth
5.5
kHz
latency time
10
μ
s