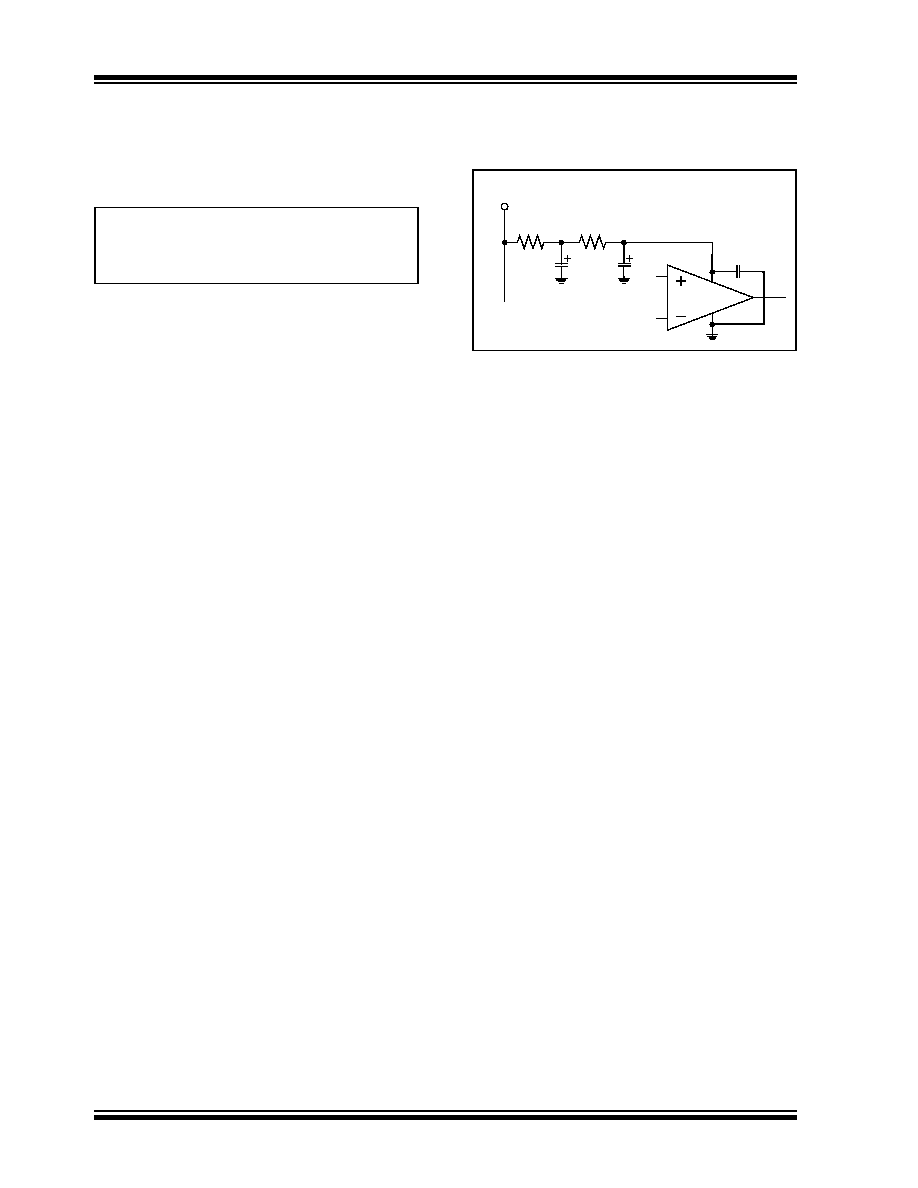
MCP6V26/7/8
DS25007B-page 26
2011 Microchip Technology Inc.
The largest value of RF that should be used depends
Loads), CG and the open-loop gain’s phase shift. An approximate limit for RF is:
EQUATION 4-2:
Some applications may modify these values to reduce
either output loading or gain peaking (step response
overshoot).
At high gains, RG and CG need to be small in order to
prevent positive feedback and oscillations.
4.3.9
REDUCING UNDESIRED NOISE
AND SIGNALS
Reduce undesired noise and signals with:
Low bandwidth signal filters:
- Minimizes random analog noise
- Reduces interfering signals
Good PCB layout techniques:
- Minimizes crosstalk
- Minimizes parasitic capacitances and
inductances that interact with fast switching
edges
Good power supply design:
- Provides isolation from other parts
- Filters interference on supply line(s)
4.3.10
SUPPLY BYPASSING AND
FILTERING
With this family of op amps, the power supply pin (VDD
for single supply) should have a local bypass capacitor
(i.e., 0.01 F to 0.1 F) within 2 mm of the pin for good
high-frequency performance.
These parts also need a bulk capacitor (i.e., 1 F or
larger) within 100 mm to provide large, slow currents.
This bulk capacitor can be shared with other low noise,
analog parts.
In some cases, high-frequency power supply noise
(e.g., switched mode power supplies) may cause
undue intermodulation distortion, with a DC offset shift;
this noise needs to be filtered. Adding a resistor into the
supply connection can be helpful. This resistor needs
to be small enough to prevent a large drop in VDD for
the op amp, which would cause a reduced output range
and possible load-induced power supply noise. It also
needs to be large enough to dissipate little power when
circuit with resistors in the supply connections. It gives
good rejection out to 1 MHz for switched mode power
supplies. Smaller resistors and capacitors are a better
choice for designs where the power supply is not as
noisy.
FIGURE 4-11:
Additional Supply Filtering.
4.3.11
PCB DESIGN FOR DC PRECISION
In order to achieve DC precision on the order of ±1 V,
many physical errors need to be minimized. The design
of the Printed Circuit Board (PCB), the wiring and the
thermal environment has a strong impact on the
precision achieved. A poor PCB design can easily be
more than 100 times worse than the MCP6V26/7/8 op
amps minimum and maximum specifications.
4.3.11.1
PCB Layout
Any time two dissimilar metals are joined together, a
temperature dependent voltage appears across the
junction (the Seebeck or thermo-junction effect). This
effect is used in thermocouples to measure tempera-
ture. The following are examples of thermo-junctions
on a PCB:
Components (resistors, op amps, …) soldered to
a copper pad
Wires mechanically attached to the PCB
Jumpers
Solder joints
PCB vias
Typical thermo-junctions have temperature to voltage
conversion coefficients of 10 to 100 V/°C (sometimes
higher).
Microchip’s AN1258 (“Op Amp Precision Design: PCB
Layout Techniques”
) contains in depth information on
PCB layout techniques that minimize thermo-junction
effects. It also discusses other effects, such as
crosstalk, impedances, mechanical stresses and
humidity.
R
F
2 k
Ω 12 pF
C
G
---------------
×
G
N
2
×
≤
VS_ANA
50
Ω
50
Ω
100 F
0.1 F
1/4W
1/10W
to other analog parts
U1
MCP6V2X