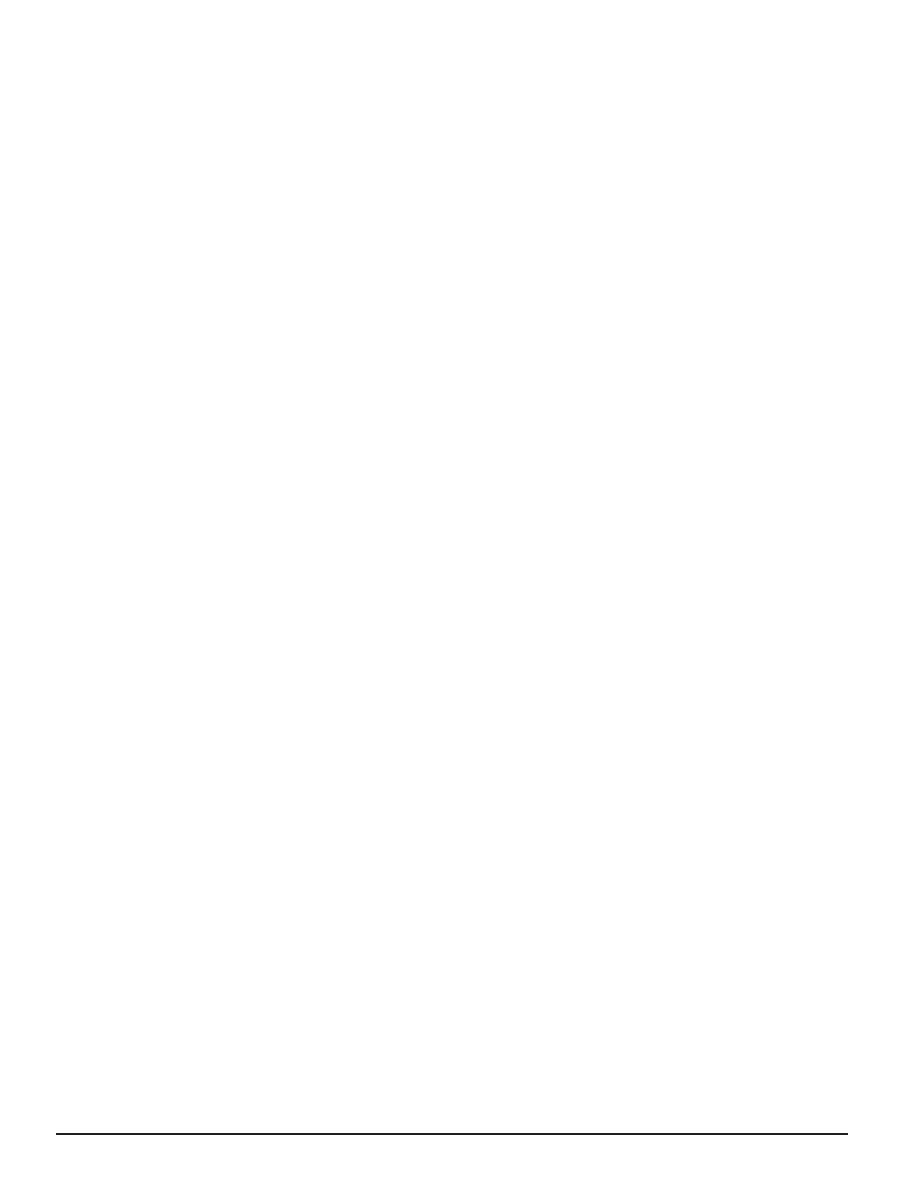
LCX Applications Information
MOTOROLA
LCX DATA
BR1339 — REV 3
16
LCX Applications Information
Introduction
Many system designers concerned about reducing power
in mobile computing and communications are unnecessarily
avoiding the use of 3.3V products because of either cost or
the
dreaded 3V/5V interface. Cost may be a concern, but
nearly every new 3.3V device has better performance –
either increased speed, reduced power, or both – when
compared to a 5V “counterpart”. In the long run it could easily
cost the equipment maker more to continue with older
technology rather than make the move to 3.3V or mixed
3.3V/5V systems.
There are three major reasons that chip manufacturers are
accelerating the introduction of low voltage devices.
First–DRAM manufacturers are worried about damage to
products with fine geometries. As memory becomes more
dense, feature geometries by necessity shrink. Voltages as
high as 5V would damage these compactly designed RAMs.
Second–as processor manufacturers have increased the
performance of their chips, they have found that packages
could not handle the increased power dissipation need. The
enabling factor was to move to 3.3V supplies. Power
dissipation varies roughly by the ratio of the squares of the
VCCs, (PD (VCC2)(capacitance)(frequency)), so the ratio of
reduction in power is 3.32/52 (11/25) when moving from 5V to
3.3V. Third–Battery–powered system manufactures are
continually working for extended battery life. Obviously a
56+% reduction in power would considerably extend battery
life. There are other benefits as well. Smaller packaging can
be used to house the low voltage chips–saving board space
and making the end product smaller and lighter. Smaller or
fewer power supplies are required, and costly, space–
hogging heat dissipating equipment can be eliminated.
Most 3.3V logic families can directly interface with only
3.3V products. LVC, LVX, VHC, LVQ/FACT AC, FCT3, and
HC product families are lines that may work well for pure 3.3V
system interface. Of these families only LVX and redesigned
LVC guarantee 5V–tolerant inputs. The other families can
tolerate maximum input and output levels of only VCC+0.5V. If
a 5V TTL bus voltage swings to levels that exceed these
specifications then the non 5V–tolerant products may be
damaged, destroyed, load the bus, or current may be
sourced into the 3.3V supply. Not only is it important to be
5V–tolerant on the inputs but to be 5V–tolerant on the outputs
as well.
The LCX logic family provides the necessary circuitry to
bridge the technology gap between the 5V and 3.3V worlds.
The inputs of this low voltage family can be safely driven to
5.5V, guaranteed, easily handling a 5V TTL or 5V CMOS
interface on the input bus. When the LCX device outputs, or
I/Os, have finished their tasks and are in the high–impedance
state, the voltage levels on the bus to which they are tied may
rise well above the 3.3V VCC, up to 5.5V without loading the
bus or causing damage to the device or power supply,
guaranteed. This capability has been properly termed
5V
tolerant, rather than 3.3V/5V translation which is a misnomer.
(Products that are powered by 3.3V supplies do not drive 5V
rail–to–rail output swings. Dual 3.3V/5V supply devices are
needed to drive 5V CMOS level outputs. See 74LVXC3245
and 74LVX4245–translating transceivers.)
There is no longer reason to fear mixed voltage designs.
The LCX CMOS family is available now to help you bridge the
3.3V–5V interface.
Interfacing Dual Systems
To properly interface between integrated circuits, it is
imperative that input and output specifications be reviewed
and voltage and current levels satisfied. Output
specifications (VOH and VOL) of the driving device must meet
or exceed the input requirements (VIH and VIL) of the
receiving device for the interface to function properly.
Meeting these requirements protects against malfunction
when operating at different environments which may induce
noise to the interface.
The 5V power supply has been the standard for many
years in the IC world. Several product families have been
introduced with varying speeds, drive capabilities, and power
requirements. Because of this many I/O standards have
evolved complicating the interface between 5V devices. The
move to 3.3V power supplies actually simplifies the interface
problem. Pure Bipolar products cannot function at 3.3V, so
the core technology is either BiCMOS or pure CMOS. In a
pure 3.3V MOS environment the interface can be made
directly–inputs and outputs. However, it will be several years
before all system components operate from 3.3V supplies.
This is especially true for peripheral devices such as printers,
displays, and faxes.
Interfacing 5V–TTL to Pure 3.3V Logic
(No 5V–Tolerance)
When the desired interface is 5V–TTL to pure 3.3V CMOS
(such as FACT AC or LVQ), the solution becomes a little
messy. The designer must make sure that the 5V–TTL
outputs do not exceed the 3.3V CMOS input specifications.
There are a few options available to protect the 3.3V device
from excessive input current. The 3.3V and 5V power
supplies should be regulated together. It would also be a
benefit to run the 5V supply on the low side reducing the
VCC–VOH difference. If, however, the power supplies are not
regulated together and the supplies end up at 5V+10% and
3.3V–10% then the CMOS input specifications would likely
be violated. To keep within the CMOS input specification the
5V–TTL output cannot exceed 0.5V + VCC of the CMOS
device. The simplest way to insure that VOH remains within
the input specification of the CMOS part is to use a parallel
termination resistor tied to ground. There are also CMOS
switches that can be placed between the 5V and 3.3V
devices to reduce the VOH, but this solution is very
expensive.