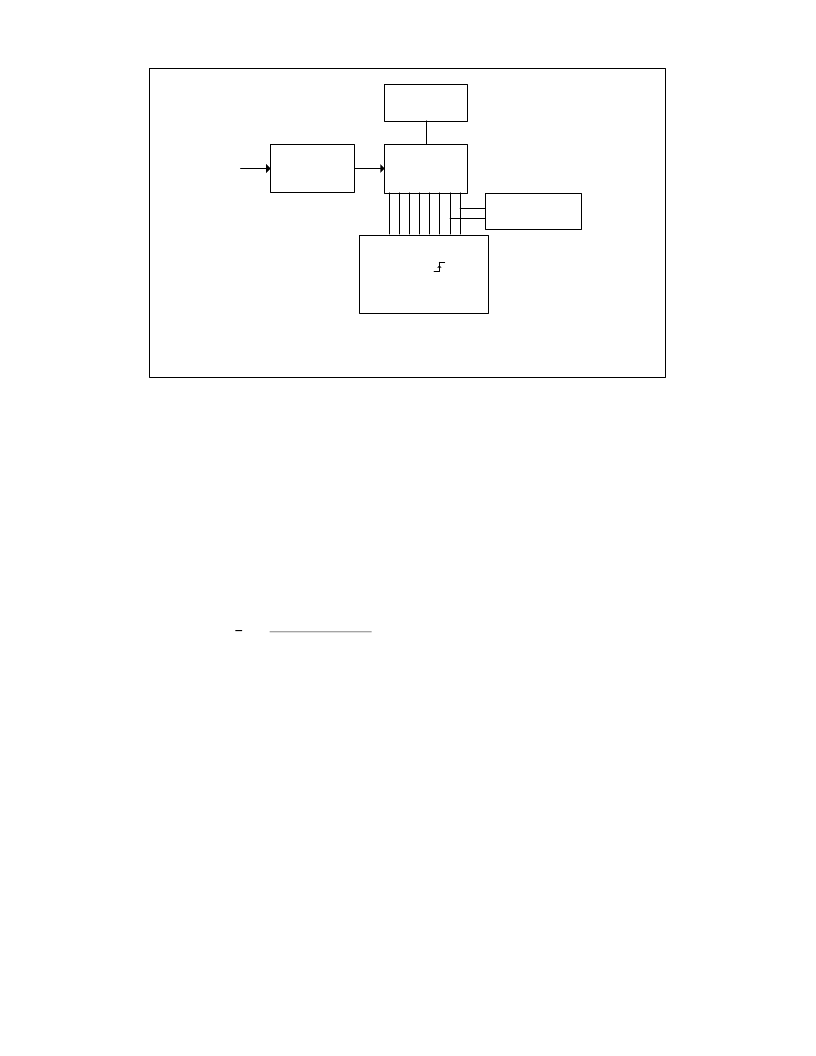
SMSC DS – LPC47M192
Page 124
Rev. 03/30/05
DATASHEET
Note
: If the fan is working the Fan Tachometer register will be latched by the Fan Tachometer
input. If the fan fails, the first time the overflow bit is generated the Fan Tachomter register will
be updated. The Fan Tachometer Registerwill not be updated again until after the Fan
Tachometer input resets the counter.
Preload
Logic to generate
PME event
Programmable
Divider
1, 2, 4, 8
Counter
32kHz
Latch
Fan Tach Register
on
Fan Tach input pulse
or
Counter=0xFF
FIGURE 9
CONCEPTUAL BLOCK DIAGRAM OF FAN MONITORING LOGIC
Fan Tachometer Register
The Fan Tachometer registers are used to store the value of the counter that monitors the speed of the associated
fan. This value may be used by the operating system to monitor how the fan is functioning.
The ACPI BIOS polls this register periodically to determine the speed at which the fan rotor is revolving. See the
Metalious ACPI/Manageability Specification
, v1.0, dated April 30, 1999. The BIOS looks for particular values in this
register to determine the rate at which the fan is functioning. (i.e. Count = FFh; means the fan has stopped). Since
the count value must correspond to a particular rate of functioning, the Preload register is used to offset any
differences. Therefore, the equation below has been derived to calculate the desired values for Count.
The fan count is determined according to the following equation:
1
1.966 x 10
6
Count =
2
RPM x Divisor
(Term 1)
In addition to the ACPI BIOS polling the register, a PME or SMI is generated at a count of 192, if enabled through the
PME or SMI enable register, which corresponds to the “upper limit” for the fan count. This value is made to
correspond to the “l(fā)ower limit” of the RPM for the fan by programming the divisor and preload value accordingly.
Typical practice is to consider 70% of normal RPM a fan failure.
Fan Preload Register
The preload value is programmable via the FAN1 Preload Register and FAN2 Preload Register. The preload is the
initial value for the fan count, which is used to adjust the count such that the value of 192 corresponds to the “l(fā)ower
limit” of the RPM. By setting the preload value and divisor properly, a PME or SMI will be generated when the RPM
reaches the percentage of the nominal RPM that indicates a fan failure.
Notice in the examples shown below the Preload value was determined to be 32 for a fan that normally operates at
4400 RPMs. This preload value was determined for the case that a PME should be initiated at 70% of normal
operation. A PME is generated when the counter reaches 192, but at 70% in this example only 160 counts are
generated during one Fan Tachometer input pulse leaving a difference of 32.
Examples
Term 1 in the equation above is of the value determined by multiplying the clock source of 32.768kHz by
60sec/min and dividing by the product of the revolutions per minute times the divisor. The factor of in Term 1
corresponds to two pulses per revolution. The default divisor, located in the Fan Control Register, is two. This results
x
+ Preload (Equation 1)