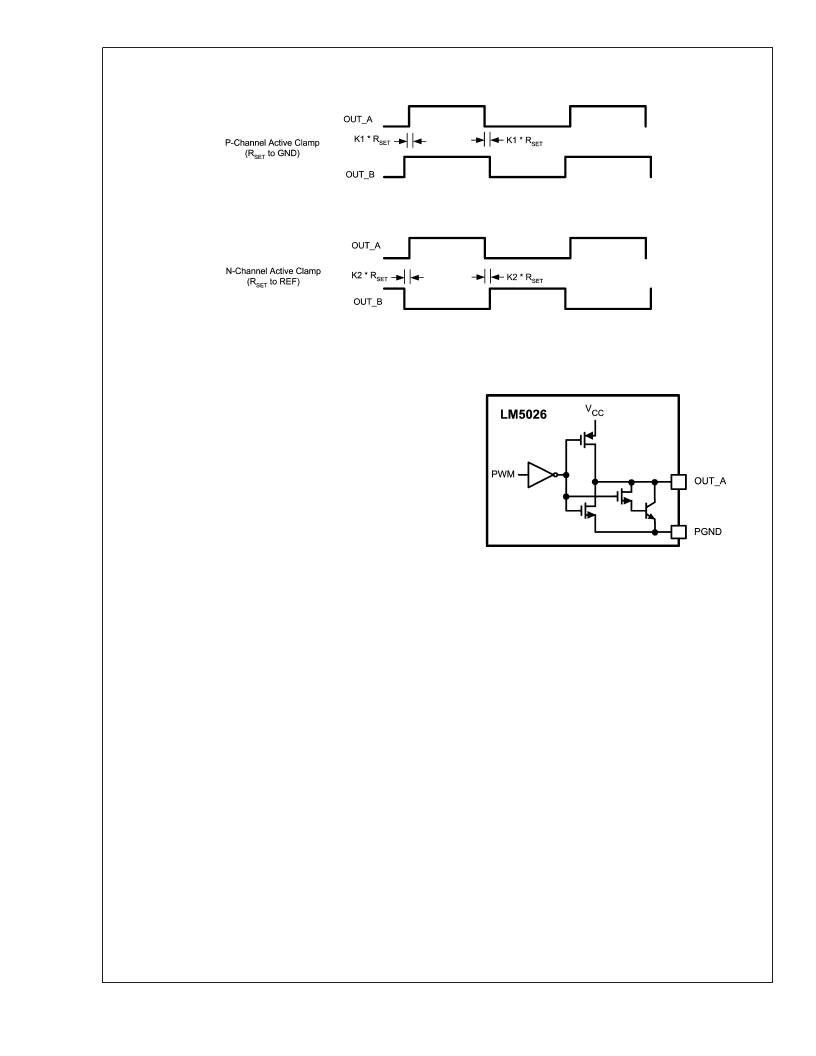
PWM Outputs
(Continued)
The rising edge overlap or deadtime and the falling edge
overlap or deadtime are identical and are independent of
operating frequency or duty cycle. The magnitude of the
overlap/deadtime can be calculated as follows:
Overlap Time = 2.8 x R
SET
+ 2
Deadtime = 2.9 x R
SET
+ 14
With R
SET
in K Ohms and overlap / deadtime in nanosec-
onds
Gate Driver Outputs
The LM5026 provides two gate driver outputs, the main
power switch control (OUT_A) and the active clamp switch
control (OUT_B). The main gate driver features a compound
configuration, consisting of both MOS and bipolar devices,
which provide superior gate drive characteristics. The bipolar
device provides most of the drive current capability and sinks
a relatively constant current, which is ideal for driving large
power MOSFETs. As the switching event nears conclusion
and the bipolar device saturates, the internal MOS device
provides a low impedance to compete the switching event.
During turn-off at the Miller plateau region, typically between
2V - 4V, the voltage differential between the output and
PGND is small and the current source characteristic of the
bipolar device is beneficial to reduce the transition time.
During turn-on, the resistive characteristics of a purely MOS
gate driver is adequate since the supply to output voltage
differential is fairly large in the Miller region.
PWM Comparator/Slope
Compensation
The PWM comparator modulates the pulse width of the
controller output by comparing the current sense ramp signal
to the loop error signal. This comparator is optimized for
speed in order to achieve minimum controllable duty cycles.
The loop error signal is input into the controller in the form of
a control current into the COMP pin. The COMP pin control
current is internally mirrored by a matched pair of NPN
transistors which sink current through a 5 k
resistor con-
nected to the 5V reference. The resulting error signal passes
through a 1.4V level shift and a gain reducing 3:1 resistor
divider before being applied to the pulse width modulator.
The opto-coupler detector can be connected between the
REF pin and the COMP pin. Because the COMP pin is
controlled by a current input, the potential difference across
the optocoupler detector is nearly constant. The bandwidth
limiting phase delay which is normally introduced by the
significant capacitance of the opto-coupler is greatly re-
duced. Greater system loop bandwidth can be realized,
since the bandwidth-limiting pole associated with the opto-
coupler is now at a much higher frequency. The PWM com-
parator polarity is configured such that with no current into
the COMP pin, the controller produces the maximum duty
cycle at the main gate driver output.
20147913
FIGURE 2. PWM Output Phasing / Timing
20147914
FIGURE 3. Compound Gate Driver
L
www.national.com
12