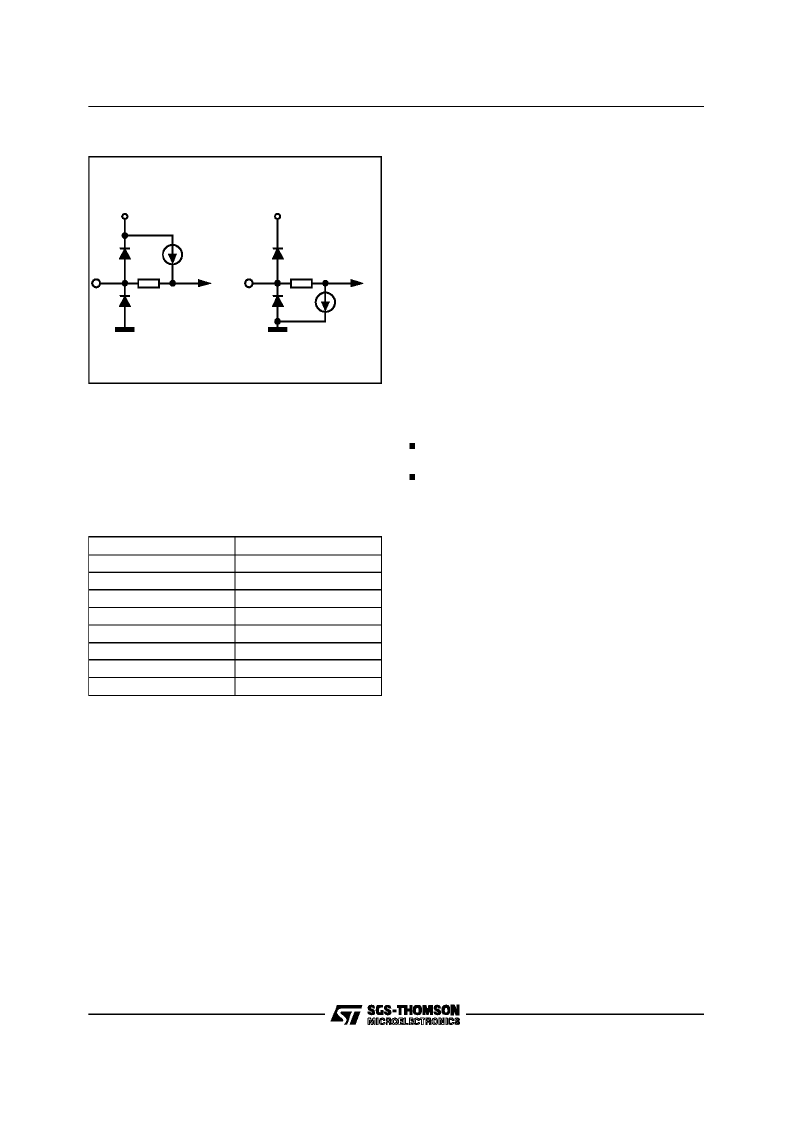
used in an application, it may either be connected
to ground or VLOGIC as required, It may also be
simply left unconnected.
If no connection is made, the pin is either pulled
high or low by internal constant current gener-
ators as shown above.
A listing of the logic and clock inputs is shown in
Table1 with the correspondingdefault state.
1.3 Modes of Operation
There are 5 basicmodes of operation.
1)
Tristate
When
Output Enable
is low, the output power
drivers are tristated.
2)
Start-Up
With
Output Enable
high, bringing
Run/Brake
from a low to a high will energize the motor and
the system will be driven by the Fully-Integrated
StartUp Algorithm.
A user-defined Start-Up Algorithm, under control
of a MicroProcessor, can also be achieved via the
sequenceincrementinput.
3)
Run
Run mode is achieved when the motor speed
(controlled
by
the
external
microprocessor)
reaches the nominalspeed.
4)
Park
When
Run/Brake
is brought low, energy to park
the heads may be derivedfrom the rectified Bemf.
The energy recovery time is a function of the
Brake Delay Time Constant. In this state, the qui-
escent current of the device is minimized (sleep
mode).
5)
Brake
After the Energy Recovery Time-Out, the device
is in Brake, with all lower Drivers in full conduc-
tion.
There are two mutually exclusive conditions
which may be present during the Tristate Mode
(wake up):
a)the spindle is stopped.
b)the system is still running at a speed that
allows for resynchronization.
In order to minimize the ramp up time, the micro-
controllerhas the possibilityto:
check the SPIN SENSE pin, (which toggles at
the Bemf zero crossing frequency)
enable the power to the motor based on the
previous information. Otherwise the
μ
P may is-
sue a Brake command, followed by the start-
up procedureafter the motor has stoppedspin-
ning.
2.0 STATEDIAGRAMS
2.1 StateDiagram
Figure 2-1 is a complete State Diagram of the
controller depicting the operationalflow as a func-
tion of the control pins and motor status.The flow
can be separatedinto four distinct operations.
2.2 Align + Go
Figure 2-2 represent the normal flow that will
achieve a spin-up of the spindle motor using the
internallygenerated startup algorithm.
Upon
power
up,
or
Run/Brake
low the controller first sets the state
machine for State=1with the Outputs Tristated.
The period counter that monitors the time be-
tween zero crossing is stopped, analog with the
phase and maskdelay counters.
When
Run/Brake
is brought high, the motor is in
the first part of the align mode at State 2
(Output
A
high and
Output C
low). If
Output Enable
is
high, the controller first checks to determine if the
motor is still spinning for a time of 21
(with
Sys_Clk = 10MHz). The drivers are now enabled
and after the align time-out, (64/Falign), the se-
quencer double increments the outputs to State 4
(Output
B high and
Output
A low). The first part
of this align mode is used to reduce the effects of
stiction
from
any
state
with
Pin Function
Tdly (0,1,2)
Select Pole
PWM/Linear
Output Enable
Run/Brake
Sequence Increment
System Clock
Faling
Configuration
Pull-Down
Pull-Down
Pull-Down
Pull-Down
Pull-Up
Pull-Down
Pull-Up
Pull-Up
Table 1
330
V
LOGIC
10
μ
A
330
V
LOGIC
10
μ
A
PULL-UP
PULL-DOWN
D95IN279
Figure 1-2
L6238S
9/31