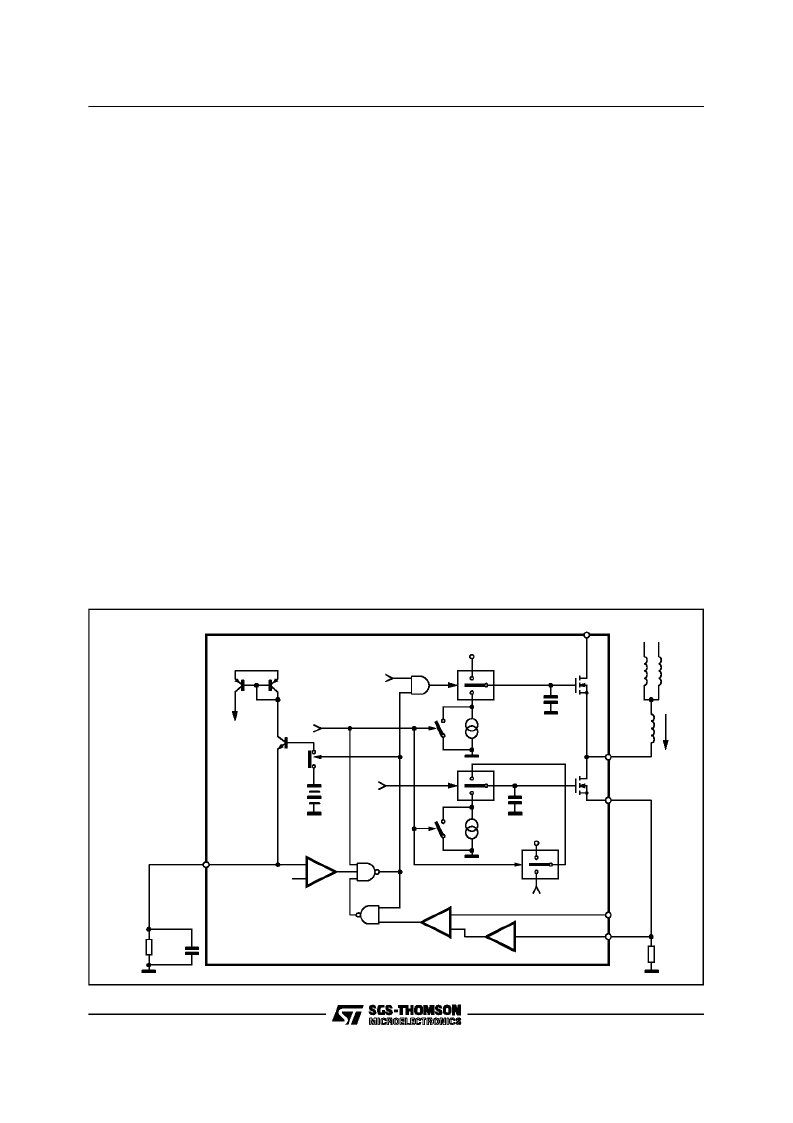
The high current flows from the grounded sub-
strate of the integrated circuit (p-type material),
throughone or more epitaxial pockets(n-type ma-
terial) and out the centerpar pin.
This current can cause adverse operation of the
controllet due to substrate injection and might
possibility damage the internal metalization runs.
The normal current for this input is in the 200
μ
A
range.
Referring to figure 4-13, a simple protection
scheme consisting of a 1K resistor and a low cur-
rent Schottky diode should be added if the appli-
cation causes excessive current (i.e. >1mA) to
flow through the center tap pin.
5.0 PWM MOTOR CURRENT CONTROL
A unique feature of the L6238S in the optional
Pulse Width Modulation (PWM) control of motor
current.
Using Variable-frequency, Constant-OFF time
Current-Mode control, the L6238S can drive
higher power motors without the need for external
drivers, while minimizing internal power dissipa-
tion.
Additional benefits include reduced power supply
consumption(up to 50% savings)and lower watt-
age requirements for the current sensingresistor.
Constant-OFF time Current-Mode control, oper-
ates on the principle of monitoring the motor cur-
rent and comparison it to a reference or control
level.
When the motorcurrent reachesthis commanded
level, the output drivers turn OFF and remain
OFFfor a Constant-OFF time. After this OFF time
the drivers turn back ON to repeat the cycle.
Figure 5.1 is a block diagram of the PWM control
circuitry. When using PWM as opposed to linear
control, two changes are made to the control
loop:
1.The slew rate control is disabled,allowing the
outputs to slew at a minimum rate of 10V/
μ
s.
This is accomplished by closing SW3 and
SW5.
2.The OTA amplifier is taken out of the control
loop via SW6. The lower drivers are now
driven into hard conductionby tying the gates
to the analogsupply during the On time of the
PWM cycle.
The currentin the motor windingsis monitored via
the voltage dropped in the sensing resistor,
R
sense
.
This voltage is multiplied by a factor of 4 in the
Current Sense Amplifier (CSA) and sent to nega-
tive inputof the PWMComparator (A2).
The control voltage, V
control
, is applied to the posi-
tive input of A2. When the output of the CSA
reaches a level that is equal to the commanded
level, the output of A2 switches low, toggling the
latch comprised of N1 and N2. This causes the
upper drivers to turn off andopens SW1. Q3 turns
OFF allowing the Constant-OFF time capacitors,
I1
Islew
V
PUMP
SW2
1
0
Cfet
UPPER A
+
-
A1
PWM/SLEW
X4
A3
VPOWER
I2
Islew
SW3
1
0
Cfet
OUTPUT
B
C
OUTA
L1
L2
L3
Q4
Q5
SLEW RATE
REFERENCE
CURRENT
R
SLW
RSENSE
CSA
VCTRL
LOWER A
D95IN318
N3
Q1
Q2
VANALOG
3.1V
SW1
Q3
1.2V
SW5
N1
SW4
N2
A2
+
-
PWM/LIN
CONTROL
1
0
FROM TRANS. LOOP
CSA
SW6
V
ANALOG
COFF
RSLEW
Figure 5-1
L6238S
22/31