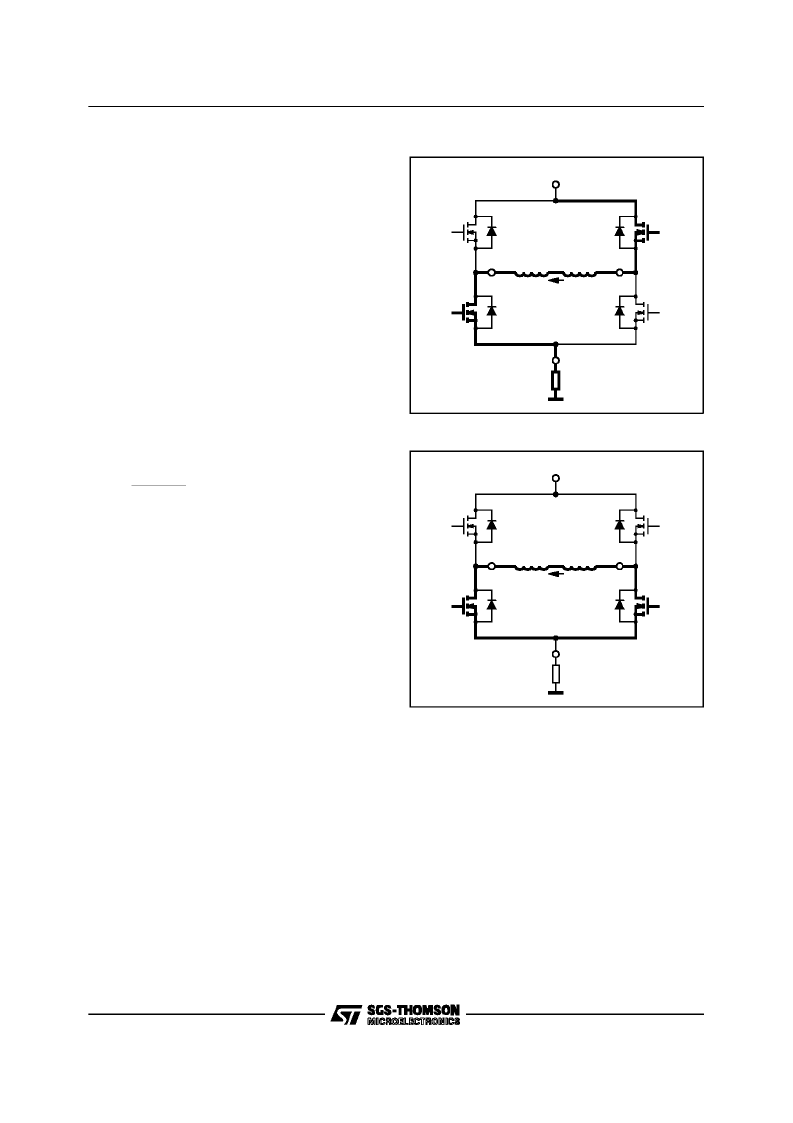
C
off
to discharge to dischargtethrough R
slew
, initi-
ating the Constant-OFF time-out. When the volt-
age on C
off
reaches 1.2V, comparator A1switches
state toggling the latch in the opposite state, turn-
ing the upper driver back ON. SW1 also closed
quickly charging up C
off
for the nextcycle.
5.1 PWM Design Considerations
In order to select the parameters associated with
PWM operation, the following factors must be
takeninto consideration:
1. PWM Switching Frequency
2. Duty Cycle
3. Motor Currents
4. Minimum ON Time
5. Noise Blanking
6. Bemf Masking/Sampling
5.1.1. PWM Switching Frequency
The PWM switching frequency F
pwm
is found
from:
F
pwm
=
1
T
on
+
T
off
(5.1.1)
where:
T
on
= The time required for the motor current
to reach the commanded level.
T
off
= The programmedOFF time.
The two main considerations for this parameter
are the minimum and maximum switching fre-
quency.
The maximum switching frequency occurs during
the Start-up and should be kept below 50KHzdue
tointentional bandwidth limitations and output
switching losses.
5.1.2 Duty Cycle
Besides reducing the power dissipation of the
controller output stage, running in PWM offers 2
additional”free” benefits:
A. Reduced Powe SupplyCurrent at StartUp
B. Lower PowerRating for the Motor Current
SenseResistor.
Figure 5-2 is the current path during the ON time
of a phase period. The current from the supply
passes through the upper sourcing DMOS, Q3
transistor through the two driven winding, the
lower DMOS, Q2 and finally through the current
sensing resistor R
sns
. Since both Q3 and Q4 are
ON, while Q3 is turnedOFF. The voltage,causing
the current to continue to flow through Q2, and
Q4.
If the duty cycle is nearor at 50%, then for 1/2 the
PWM cycle, no current is flowing from the power
supply or the sense resistor while current is still
flowing in the motor. This lowers the requirement
for both the Power Supply and the Power Rating
for the sensing resistor.
5.1.3 Motor Currents
Note:
It is not the objective of thissection to describe the principles
of brushless DCmotor, buttoprovide sufficient informationabout the
parameters associated with PWM operation in order to optimize an
application.
A simplifiedmodel of a motoris shown in figure 5-
4. For this discussion, lower order effects due to
mutual inductance between windings, resistance
due to losses in the magnetic circuit, etc. are not
shown.
The motor at
stall
is equal to a resistance,
Rmtr
,
in serieswith an inductance,
Lmtr
. When the mo-
tor is rotating, there is an induced emf that ap-
pears across the armaure terminals and is shown
in figure 5-4 as an internally generated voltage
Ibemf),
Eg
.
L1
L2
OUTPUTA
OUTPUTB
D2
D1
D4
D3
Q1
Q2
Q3
Q4
V
POWER
R
SENSE
R
SNS
D95IN319
Figure5-2
L1
L2
OUTPUTA
OUTPUTB
D2
D1
D4
D3
Q1
Q2
Q3
Q4
V
POWER
R
SENSE
R
SNS
D95IN320
Figure5-3
L6238S
23/31