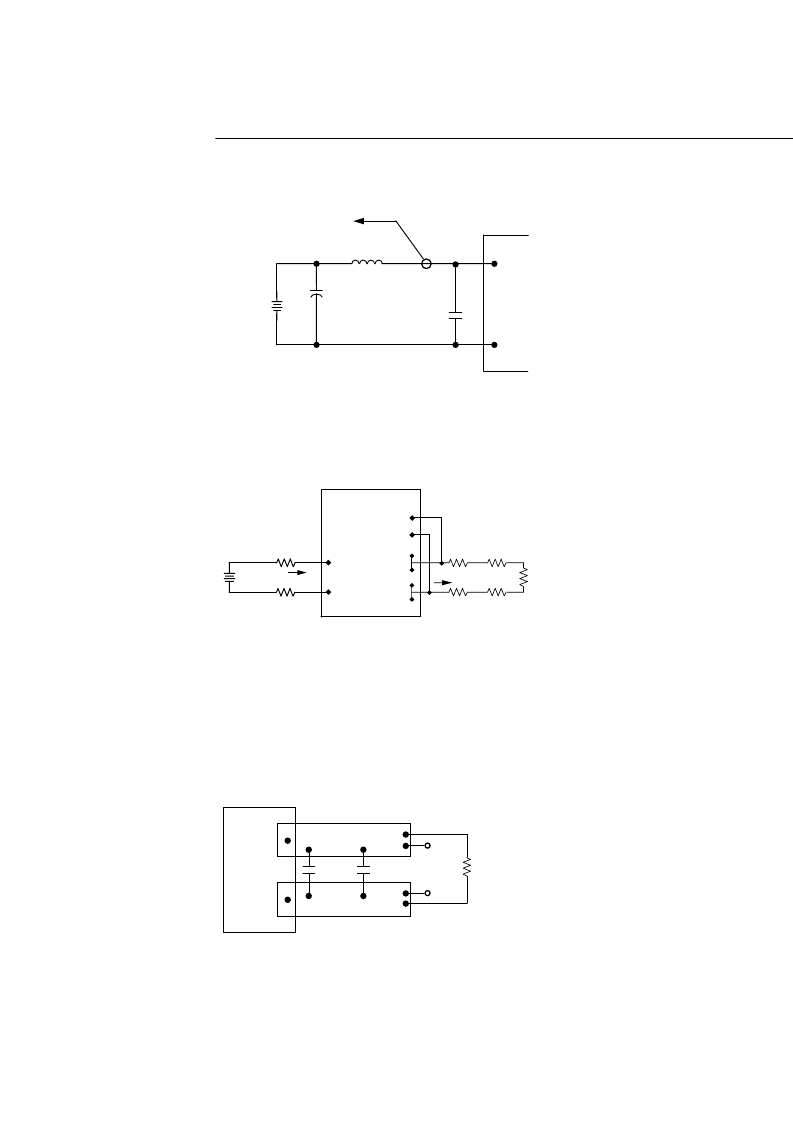
Tyco Electronics Corp.
7
Data Sheet
May 1999
dc-dc Converter; 18 Vdc to 36 Vdc Input, 28 Vdc Output; 250 W
FC250R Power Module:
Test Configurations
8-203 (C).o
Note: Measure input reflected-ripple current with a simulated source
inductance (L
TEST
) of 12 μH. Capacitor C
S
offsets possible bat-
tery impedance. Measure current as shown above.
Figure 8. Input Reflected-Ripple Test Setup
8-683 (C).f
Note: All measurements are taken at the module terminals. When
socketing, place Kelvin connections at module terminals to
avoid measurement errors due to socket contact resistance.
Figure 9. Output Voltage and Efficiency
Measurement Test Setup
8-513 (C).n
Note: Use a 0.1 μF ceramic capacitor and a 330 μF aluminum or
tantalum capacitor. The 330 μF capacitor is needed for stability.
Scope measurement should be made using a BNC socket.
Position the load between 50 mm and 76 mm (2 in. and 3 in.)
from the module.
Figure 10. Peak-to-Peak Output Noise
Measurement Test Setup
Design Considerations
Input Source Impedance
The power module should be connected to a low
ac-impedance input source. Highly inductive source
impedances can affect the stability of the power mod-
ule. For the test configuration in Figure 8, a 100 μF
electrolytic capacitor (ESR < 0.3
at 100 kHz)
mounted close to the power module helps ensure sta-
bility of the unit. For other highly inductive source
impedances, consult the factory for further application
guidelines.
Safety Considerations
For safety-agency approval of the system in which the
power module is used, the power module must be
installed in compliance with the spacing and separation
requirements of the end-use safety agency standard,
i.e., UL1950, CSAC22.2 No. 950-95, and VDE 0805
(EN60950, IEC950).
For the converter output to be considered meeting the
requirements of safety extra-low voltage (SELV), the
input must meet SELV requirements.
The power module has extra-low voltage (ELV) outputs
when all inputs are ELV.
The input to these units is to be provided with a maxi-
mum 25 A normal-blow fuse in the ungrounded lead.
Feature Descriptions
Overcurrent Protection
To provide protection in a fault (output overload) condi-
tion, the unit is equipped with internal current-limiting
circuitry and can endure current limiting for an unlim-
ited duration. At the point of current-limit inception, the
unit shifts from voltage control to current control. If the
output voltage is pulled very low during a severe fault,
the current-limit circuit can exhibit either foldback or
tailout characteristics (output-current decrease or
increase). The unit operates normally once the output
current is brought back into its specified range.
TO OSCILLOSCOPE
12 μH
V
I
(+)
V
I
(–)
BATTERY
L
TEST
Cs 220 μF
ESR < 0.1
@ 20
°
C, 100 kHz
100 μF
ESR < 0.3
@ 100 kHz
V
I
(–)
V
O
(+)
SENSE(+)
SENSE(–)
V
O
(–)
V
I
(+)
I
O
LOAD
CONTACT AND
DISTRIBUTION LOSSES
SUPPLY
I
I
CONTACT
RESISTANCE
η
V
+
V
[
O
I
+
( )
– V
I
–
–
( )
------------------- – V
]
I
O
]
I
I
x 100 %
=
V
O
(+)
V
O
(–)
1.0 μF
RESISTIVE
LOAD
SCOPE
COPPER STRIP
330 μF