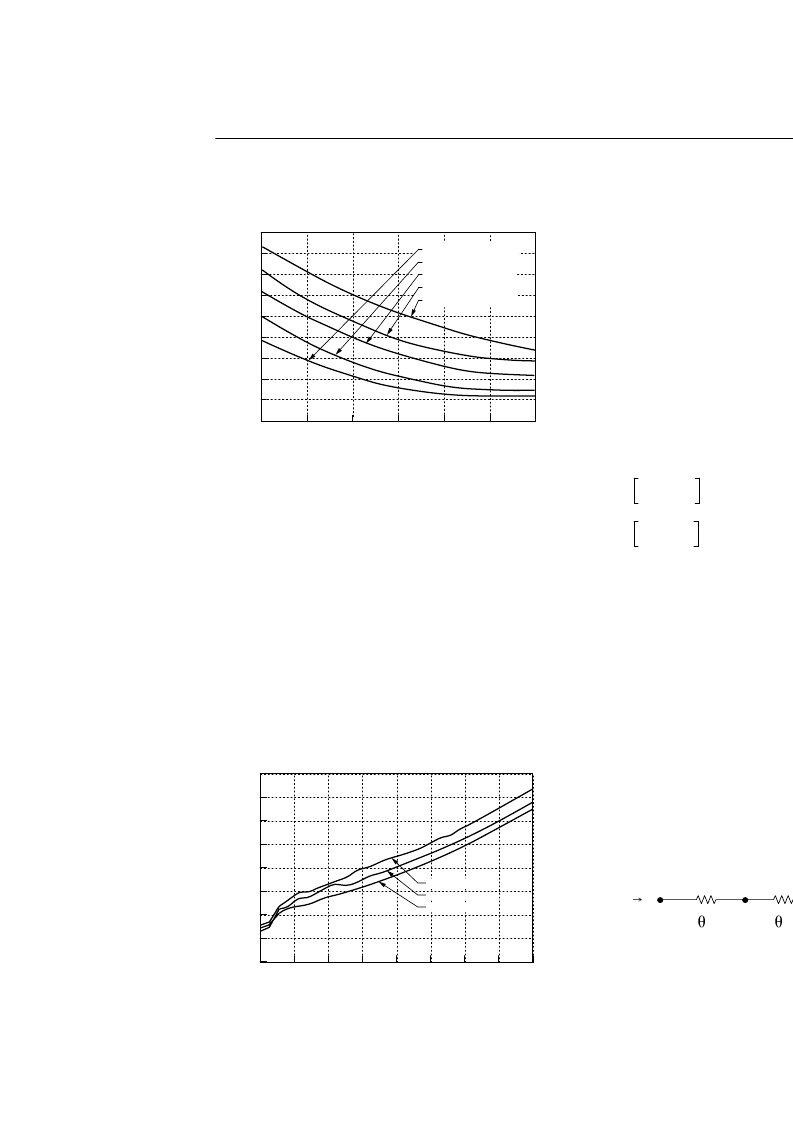
Tyco Electronics Corp.
13
Data Sheet
May 1999
dc-dc Converter; 18 Vdc to 36 Vdc Input, 28 Vdc Output; 250 W
FC250R Power Module:
Thermal Considerations
(continued)
Heat Transfer With Heat Sinks
(continued)
8-1320 (C)
Figure 22. Case-to-Ambient Thermal Resistance
Curves; Longitudinal Orientation
These measured resistances are from heat transfer
from the sides and bottom of the module as well as the
top side with the attached heat sink; therefore, the
case-to-ambient thermal resistances shown are gener-
ally lower than the resistance of the heat sink by itself.
The module used to collect the data in Figures 21 and
22 had a thermal-conductive dry pad between the case
and the heat sink to minimize contact resistance.
To choose a heat sink, determine the power dissipated
as heat by the unit for the particular application.
Figure 23 shows typical heat dissipation for a range of
output currents and three voltages for the FC250R.
8-2471 (C)
Figure 23. FC250R Power Dissipation vs. Output
Current
Example
If an 85 °C case temperature is desired, what is the
minimum airflow necessary Assume the FC250R
module is operating at nominal line and an output cur-
rent of 9.0 A, maximum ambient air temperature of
40 °C, and the heat sink is 0.5 inch.
Solution
Given: V
I
= 28 V
I
O
= 9.0 A
T
A
= 40 °C
T
C
= 85 °C
Heat sink = 0.5 inch.
Determine P
D
by using Figure 23:
P
D
= 34 W
Then solve the following equation:
Use Figures 21 and 22 to determine air velocity for the
0.5 inch heat sink. The minimum airflow necessary for
this module depends on heat sink fin orientation and is
shown below:
I
1.6 m/s (320 ft./min.) (oriented along width)
I
2.0 m/s (400 ft./min.) (oriented along length)
Custom Heat Sinks
A more detailed model can be used to determine the
required thermal resistance of a heat sink to provide
necessary cooling. The total module resistance can be
separated into a resistance from case-to-sink ( cs) and
sink-to-ambient (
θ
sa) as shown in Figure 24.
Figure 24. Resistance from Case-to-Sink and Sink-
to-Ambient
0
0.5
(100)
1.0
(200)
1.5
(300)
2.0
(400)
2.5
(500)
3.0
(600)
AIR VELOCITY, m/s (ft./min.)
0.0
0.5
3.0
3.5
4.0
4.5
2.5
2.0
1.0
C
R
C
°
C
1 1/2 in. HEAT SINK
1 in. HEAT SINK
1/2 in. HEAT SINK
1/4 in. HEAT SINK
NO HEAT SINK
1.5
2
3
4
5
6
7
0
35
OUTPUT CURRENT, I
O
(A)
25
20
30
40
1
5
V
I
= 36 V
V
I
= 28 V
V
I
= 18 V
10
15
P
D
9
8
θ
ca
T
C
-------P
T
A
–
(
)
D
=
θ
ca
85
-------34
40
–
(
)
=
θ
ca
1.32
°C/W
=
P
D
T
C
T
S
cs
sa