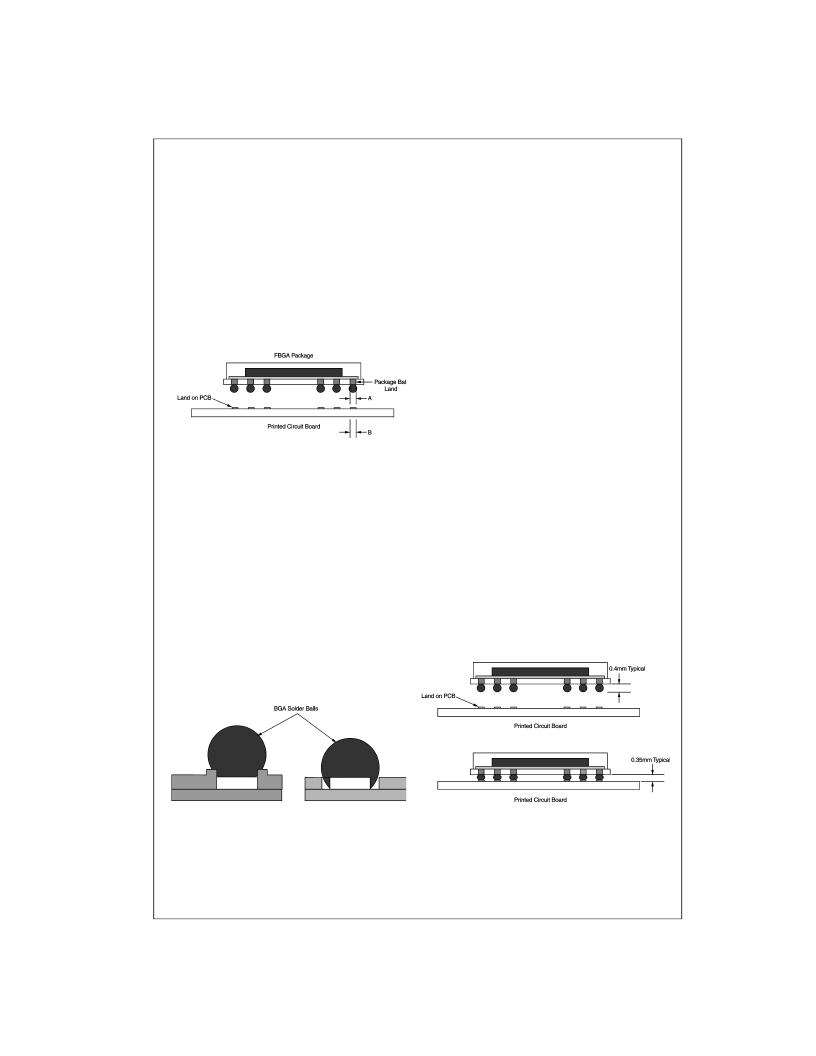
www.fairchildsemi.com
6
A
BGA Board Design
To achieve maximum reliability, the design of the PCB on
which the BGA is mounted should be considered. In partic-
ular, the diameter of package lands and board lands are
very important. The actual sizes of these dimensions are
key factors, but their ratio is also of critical importance. Fig-
ure 14 shows a BGA Board Layout with the optimum 1 to 1
ratio for package land to PCB land. This optimized ratio
equalizes stresses, reducing the chances of a stress
cracked solder ball, which will lead to premature system
failure. Ratios other than 1 to 1 will lead to unequal distribu-
tion of stress loads. For example, solder lands that are
larger than the package lands will place a greater amount
of stress on the ball at the package land to ball interface.
This can cause cracking and premature failure at the pack-
age land to ball interface.
FIGURE 14. BGA Board Layout
In practice optimum land diameters are as follows:
Experience has shown that solder lands can be either sol-
der mask defined, or non-solder mask defined. However,
non-solder mask defined designs provide additional
ball-to-land contact area, making them the favored option.
The additional contact area is created from the solder ball
to pad side connection made during the soldering process.
As shown in Figure 15 this creates an improved mechani-
cal connection.
FIGURE 15. Cross-section Comparison of
Solder Mask Defined Pad (left) to
Non-Solder Mask Defined Pad (right)
with BGA Solder Ball Connections
BGA Mounting Process
Replacing leaded packages with BGA
’
s offers several
board assembly advantages:
1. Improved device planarity
2. No chance to bend leads
3. Greater pad to pad spacing
With no chance to bend or deform leads, BGA products
offer PCB manufacturers a significant yield improvement
over similar lead count fine-pitch surface mount devices.
Another important feature of BGA products is their ability to
self-align over the PCB solder lands.
This feature is caused by the surface tension of the solder
balls pulling the BGA over the pads.
The use of solder paste is recommended for mounting
BGA devices, although it is possible to omit the paste, and
only use a flux. The advantages of using paste are:
1. Paste acts as a flux, and aids wetting of the solder ball
to the PCB land.
2. Paste, being sticky, helps hold the component in place
during reflow.
3. Paste helps to overcome any minor variations in pla-
narity of the solder balls.
4. Paste contributes to the final volume of solder in the
joint, and thus allows this volume to be varied to give
an optimum joint.
No-clean type pastes are recommended, due to difficulty in
cleaning under the mounted component.
In order to produce the optimum solder joint, it is important
to understand the amount of collapse of the solder balls,
and the overall shape of the joint. These are a function of:
1. The diameter of the BGA solder ball vias.
2. The volume and type of solder paste screened onto the
PCB.
3. The diameter of the PCB land.
4. The board assembly re-flow conditions.
5. The weight of the package.
As shown in Figure 16, the original ball height on the pack-
age is 0.40mm. The ball height typically drops to 0.35mm
after the package is mounted.
FIGURE 16. BGA Solder Ball Collapse
A
=
Land diameter on package
B
=
Land diameter on printed circuit board
Ratio A/B
=
1 for best case reliability
Solder Mask defined pads:
Non-Solder Mask defined pads: 0.350mm
0.375mm