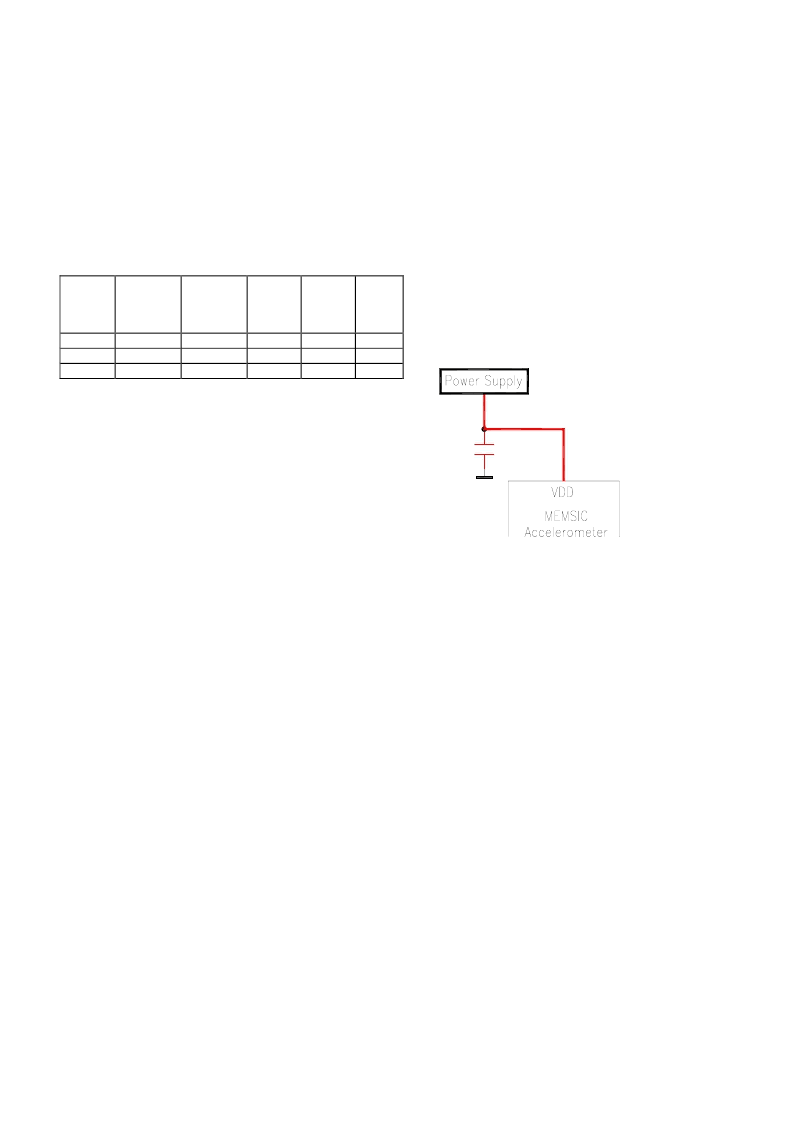
limited by the time resolution of the counting devices used
to decode the duty cycle. The faster the counter clock, the
higher the resolution of the duty cycle and the shorter the
T2 period can be for a given resolution. Table 2 shows
some of the trade-offs. It is important to note that this is the
resolution due to the microprocessors’ counter. It is
probable that the accelerometer’s noise floor may set the
lower limit on the resolution.
T2 (ms)
Rate
(MHz)
10.0
100
2.0
10.0
100
1.0
10.0
100
0.5
Table 2: Trade-Offs Between Microcontroller Counter Rate and
T2 Period.
MXD6125Q PIN DESCRIPTIONS
V
DD
– This is the supply input for the circuits and the
sensor heater in the
accelerometer
. The DC voltage should
be between 2.7 and 3.6 volts. Refer to the section on PCB
layout and fabrication suggestions for guidance on external
parts and connections recommended.
COM
– This is the ground pin for the
accelerometer
.
TP
– This pin should be connected to ground.
Xout
– This pin is the digital output of the X-axis
acceleration sensor. It is factory programmable to 100Hz.
The user should ensure the load impedance is sufficiently
high as to not source/sink >100
μ
A typical. While the
sensitivity of this axis has been programmed at the factory
to be the same as the sensitivity for the y-axis, the
accelerometer
can be programmed for non-equal sensitivities
on the x- and y-axes. Contact the factory for additional
information.
Yout
–
This pin is the digital output of the Y-axis
acceleration sensor. It is factory programmable to 100Hz.
The user should ensure the load impedance is sufficiently
high as to not source/sink >100
μ
A typical. While the
sensitivity of this axis has been programmed at the factory
to be the same as the sensitivity for the x-axis, the
accelerometer
can be programmed for non-equal sensitivities
on the x- and y-axes. Contact the factory for additional
information.
PD
–
Pin1 is the power down control pin. Pull this pin
HIGH will put the accelerometer into power down mode.
MEMSIC MXD6125Q
Page 5 of 6
2/24/2005
MEMSIC
Sample
Counter-
Clock
Rate
Counts
Per T2
Cycle
20000
10000
5000
Counts
per
g
2500
1250
625
Reso-
lution
(m
g
)
0.4
0.8
1.6
When the part does into power down mode, the total
current will be smaller than 0.1uA at 3V.
In normal operation mode, this pin should be
connected to Ground.
POWER SUPPLY NOISE REJECTION
One capacitor is recommended for best rejection of power
supply noise (reference Figure 5 below). The capacitor
should be located as close as possible to the device supply
pin (V
DD
). The capacitor lead length should be as short as
possible, and surface mount capacitor is preferred. For
typical applications, the capacitor can be ceramic 0.1 μF.
PCB LAYOUT AND FABRICATION SUGGESTIONS
1. Liberal use of ceramic bypass capacitors is
recommended. It is best to solder a 0.1uF capacitor
directly across V
DD
and COM pin.
2. Robust low inductance ground wiring should be used.
3. Care should be taken to ensure there is “thermal
symmetry” on the PCB immediately surrounding the
MEMSIC device and that there is no significant heat
source nearby.
4. A metal ground plane should be added directly beneath
the MEMSIC device. The size of the plane should be
similar to the MEMSIC device’s footprint and be as
thick as possible.
5. Vias can be added symmetrically around the ground
plane. Vias increase thermal isolation of the device
from the rest of the PCB.