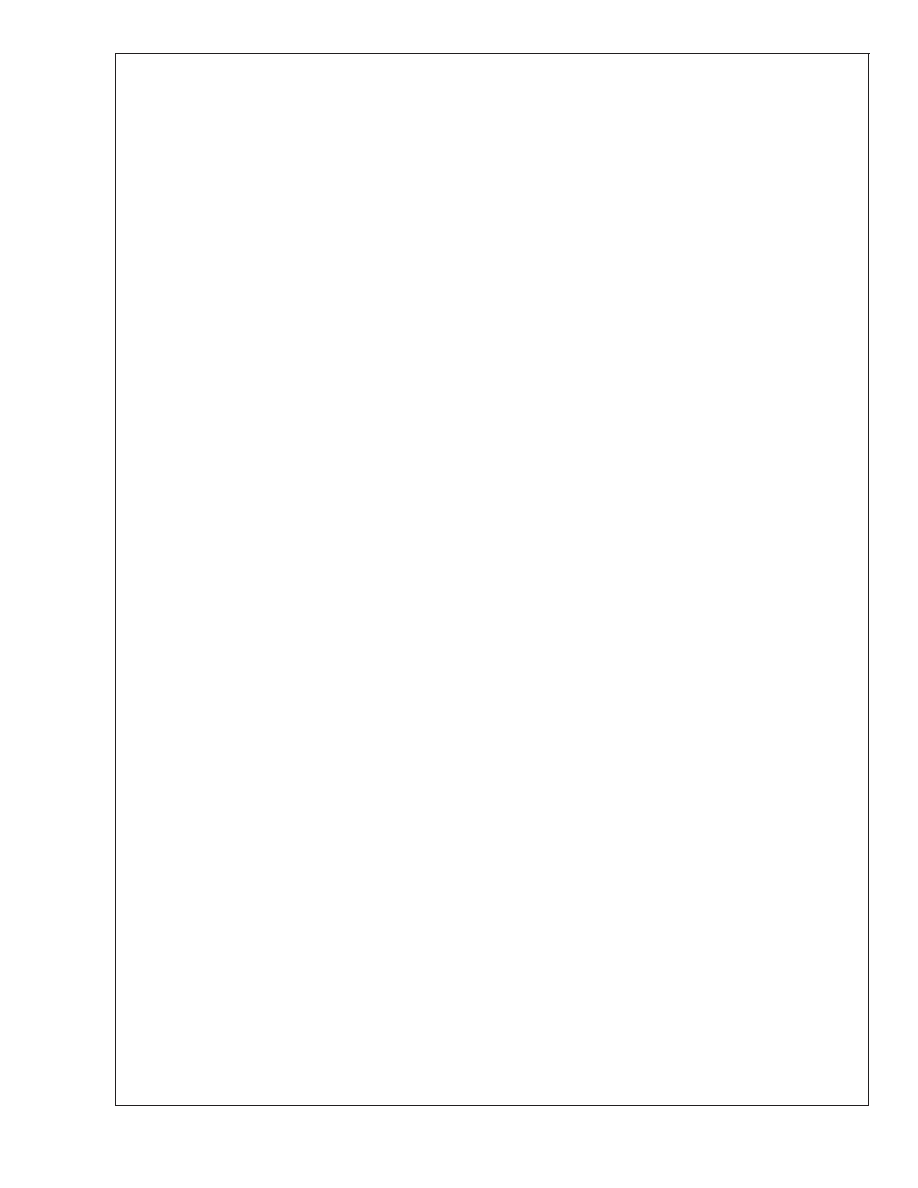
Application Information
BRIDGE CONFIGURATION EXPLANATION
As shown in
Figure 1, the LM4918 consists of two pairs of
operational amplifiers, forming a two-channel (channel L and
channel R) stereo amplifier. (Though the following discusses
channel L, it applies equally to channel R.) External resistors
Rf and Ri (set as R0 and R1, respectively for the L channel,
and R7 and R6, respectively for the R channel on the demo
board circuit) set the closed-loop gain of the first op-amp,
whereas two internal 20k
resistors set the second op-amps
gain at -1. The LM4918 drives a load, such as a speaker,
connected between the two amplifier outputs, VoL- and VoL+
first op-amp’s output serves as the second op-amp’s input.
This results in both amplifiers producing signals identical in
magnitude, but 180 out of phase. Taking advantage of this
phase difference, a load is placed between VoL- and VoL+
and driven differentially (commonly referred to as “bridge
mode”). This results in a differential gain of
A
VD=2*(Rf /Ri)
(1)
Bridge mode amplifiers are different from single-ended am-
plifiers that drive loads connected between a single amplifi-
er’s output and ground. For a given supply voltage, bridge
mode has a distinct advantage over the single-ended con-
figuration: its differential output doubles the voltage swing
across the load. This produces four times the output power
when compared to a single-ended amplifier under the same
conditions. This increase in attainable output power as-
sumes that the amplifier is not current limited or that the
output signal is not clipped. Another advantage of the differ-
ential bridge output is no net DC voltage across the load.
This is accomplished by biasing channel A’s and channel B’s
outputs at half-supply. This eliminates the coupling capacitor
that single supply, single-ended amplifiers require (such as
when using the LM4918 to drive single-ended headphone
loads). Eliminating an output coupling capacitor in a single-
ended configuration forces a single-supply amplifier’s half-
supply bias voltage across the load. This increases internal
IC power dissipation and may permanently damage loads
such as speakers.
POWER DISSIPATION
Power dissipation is a major concern when designing a
successful single-ended or bridged amplifier. Equation (2)
states the maximum power dissipation point for a single-
ended amplifier operating at a given supply voltage and
driving a specified output load.
P
DMAX =(VDD)
2 /(2
π2R
L)
Single-Ended
(2)
However, a direct consequence of the increased power de-
livered to the load by a bridge amplifier is higher internal
power dissipation for the same conditions.
The LM4918 has two operational amplifiers per channel. The
maximum internal power dissipation per channel operating in
the bridge mode is four times that of a single-ended ampli-
fier. From Equation (2), assuming a 5V power supply and a
8
load, the maximum single channel power dissipation is
0.158W or 0.317W for stereo operation.
P
DMAX =4*(VDD)
2 /(2
π2R
L)
Bridge-Mode
(3)
The LM4918’s power dissipation is twice that given by Equa-
tion (2) or Equation (3) when operating in the single-ended
mode or bridge mode, respectively. Twice the maximum
power dissipation point given by Equation (3) must not ex-
ceed the power dissipation given by Equation (4):
P
DMAX’ =(TJMAX -TA)/
θ
JA
(4)
The LM4918’s T
JMAX = 150C. In the LQ package soldered
to a DAP pad that expands to a copper area of 1in
2 on a
PCB, the LM4918’s
θ
JA is 51C/W. At any given ambient
temperature T
A, use Equation (4) to find the maximum inter-
nal power dissipation supported by the IC packaging. Rear-
ranging Equation (4) and substituting P
DMAX for PDMAX’ re-
sults in Equation (5). This equation gives the maximum
ambient temperature that still allows maximum stereo power
dissipation without violating the LM4918’s maximum junction
temperature.
T
A =TJMAX - 2*PDMAX
θ
JA
(5)
For a typical application with a 5V power supply and an 8
load, the maximum ambient temperature that allows maxi-
mum stereo power dissipation without exceeding the maxi-
mum junction temperature is approximately 85C for the LQ
package.
T
JMAX =PDMAX
θ
JA +TA
(6)
Equation (6) gives the maximum junction temperature
T
J-
MAX
. If the result violates the LM4918’s 150C, reduce the
maximum junction temperature by reducing the power sup-
ply voltage or increasing the load resistance. Further allow-
ance should be made for increased ambient temperatures.
The above examples assume that a device is a surface
mount part operating around the maximum power dissipation
point. Since internal power dissipation is a function of output
power, higher ambient temperatures are allowed as output
power or duty cycle decreases.
If the result of Equation (2) is greater than that of Equation
(3), then decrease the supply voltage, increase the load
impedance, or reduce the ambient temperature. If these
measures are insufficient, a heat sink can be added to
reduce
θ
JA. The heat sink can be created using additional
copper area around the package, with connections to the
ground pin(s), supply pin and amplifier output pins. External,
solder attached SMT heatsinks such as the Thermalloy
7106D can also improve power dissipation. Refer to the
Typical Performance Characteristics curves for power dissi-
pation information at lower output power levels.
EXPOSED-DAP MOUNTING CONSIDERATIONS
The LM4918’s exposed-DAP (die attach paddle) packages
(LD) provide a low thermal resistance between the die and
the PCB to which the part is mounted and soldered. This
allows rapid heat transfer from the die to the surrounding
PCB copper area heatsink, copper traces, ground plane, and
finally, surrounding air. The result is a low voltage audio
power amplifier that produces 1.1W dissipation in an 8
load
at
≤ 1% THD+N. This power is achieved through careful
consideration of necessary thermal design. Failing to opti-
LM4918
www.national.com
10