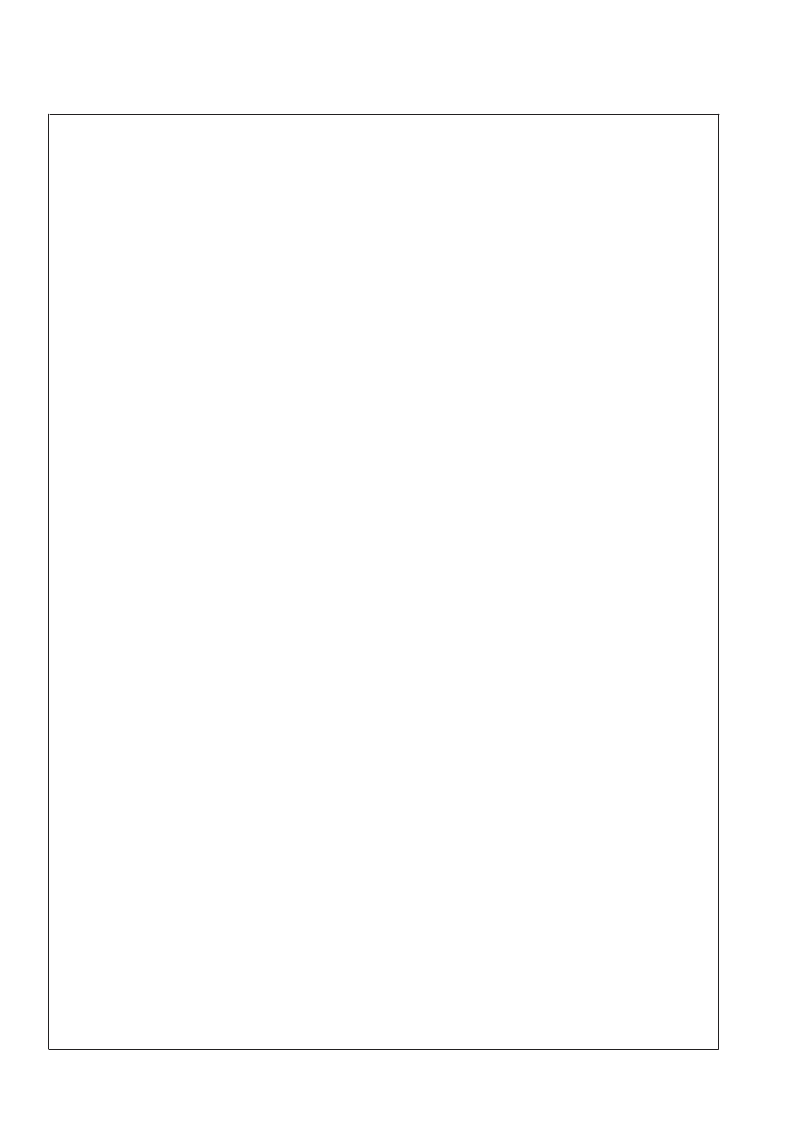
PWM Operation
(Continued)
each cycle, the clock turns on the PFET switch, causing the
inductor current to ramp up. When the current sense signal
ramps past the error amplifier signal, the PWM comparator
turns off the PFET switch and turns on the NFET synchro-
nous rectifier, ending the first part of the cycle. If an increase
in load pulls the output down, the error amplifier output
increases, which allows the inductor current to ramp higher
before the comparator turns off the PFET. This increases the
average current sent to the output and adjusts for the in-
crease in the load. Before appearing at the PWM compara-
tor, a slope compensation ramp from the oscillator is sub-
tracted from the error signal for stability of the current
feedback loop. The minimum on time of PFET in PWM mode
is 50ns (typ.)
Shutdown Mode
Setting the EN digital pin low (
<
0.5V) places the LM3207 in
a 0.01μA(typ.) Shutdown mode. During shutdown, the PFET
switch, NFET synchronous rectifier, reference voltage
source, control and bias circuitry of theLM3207 are turned
off. Setting EN high (
>
1.2V) enables normal operation.
EN should be set low to turn off the LM3207 during power-up
and under voltage conditions when the power supply is less
than the 2.7V minimum operating voltage. The LM3207 is
designed for compact portable applications, such as mobile
phones. In such applications, the system controller deter-
mines power supply sequencing and requirements for small
package size outweigh the additional size required for inclu-
sion of UVLO (Under Voltage Lock-Out) circuitry.
Internal Synchronous Rectification
While in PWM mode, the LM3207 uses an internal NFET as
a synchronous rectifier to reduce rectifier forward voltage
drop and associated power loss. Synchronous rectification
provides a significant improvement in efficiency whenever
the output voltage is relatively low compared to the voltage
drop across and ordinary rectifier diode.
The internal NFET synchronous rectifier is turned on during
the inductor current down slope in the second part of each
cycle. The synchronous rectifier is turned off prior to the next
cycle. The NFET is designed to conduct through its intrinsic
body diode during transient intervals before it turns on, elimi-
nating the need for an external diode.
Current Limiting
A current limit feature allows the LM3207 to protect itself and
external components during overload conditions. In PWM
mode, a 1200mA (max.) cycle-by-cycle current limit is nor-
mally used. If an excessive load pulls the output voltage
down to approximately 0.375V, then the device switches to a
timed current limit mode. In timed current limit mode the
internal PFET switch is turned off after the current compara-
tor trips and the beginning of the next cycle is inhibited for
3.5us to force the instantaneous inductor current to ramp
down to a safe value. The synchronous rectifier is off in
timed current limit mode. Timed current limit prevents the
loss of current control evident in some products when the
output voltage is pulled low in serious overload conditions.
Dynamically Adjustable Output
Voltage
The LM3207 features dynamically adjustable output voltage
to eliminate the need for external feedback resistors. The
output can be set from 0.8V(typ.) to 3.6V(typ.) by changing
the voltage on the analog V
pin. This feature is useful in
PA applications where peak power is needed only when the
handset is far away from the base station or when data is
being transmitted. In other instances the transmitting power
can be reduced. Hence the supply voltage to the PA can be
reduced, promoting longer battery life. See
Setting the Out-
put Voltage
in the
Application Information section
for further
details.
Thermal Overload Protection
The LM3207 has a thermal overload protection function that
operates to protect itself from short-term misuse and over-
load conditions. When the junction temperature exceeds
150C, the device inhibits operation. The PFET and NFET
are turned off in PWM mode. The LDO is turned off as well.
When the temperature drops below 130C, normal operation
resumes. Prolonged operation in thermal overload condi-
tions may damage the device and is considered bad prac-
tice.
LDO Operation
An LDO is used to provide a regulated 2.875V Vref supply to
a RF PA. The LDO can be enabled only after the PWM is
running. The LDO will automatically be disabled whenever
the EN or EN
is disabled. Included in the LDO are active
charge and discharge circuits to quickly move a 100nF ca-
pacitor to meet the 3us timing requirements, or an 220nF
capacitor to meet the 5us timing requirements. The charging
and discharging currents are controlled to minimize supply
disturbances. The LM3207 was designed specifically to work
with a 100nF or a 220nF ceramic capacitor and no bypass
capacitor.
Application Information
SETTING THE DC-DC CONVERTER OUTPUT VOLTAGE
The LM3207 features a pin-controlled variable output volt-
age to eliminate the need for external feedback resistors. It
can be programmed for an output voltage from 0.8V (typ.) to
3.6V (typ.) by setting the voltage on the V
CON
pin, as in the
following formula:
V
OUT
= 2.5 x V
CON
When V
is between 0.32V and 1.44V, the output voltage
will follow proportionally by 2.5 times of V
CON
.
If V
is over 1.44V (V
= 3.6V), sub-harmonic oscilla-
tion may occur because of insufficient slope compensation. If
V
voltage is less than 0.32V (V
= 0.8V), the output
voltage may not be regulated due to the required on-time
being less than the minimum on-time (50ns). The output
voltage can go lower than 0.8V providing a limited V
range
is used. Refer to datasheet curve (V
Voltage vs Output
Voltage) for details. This curve is for a typical part and there
could have part-to-part variation for output voltages less than
0.8V over the limited V
IN
range.
L
www.national.com
15