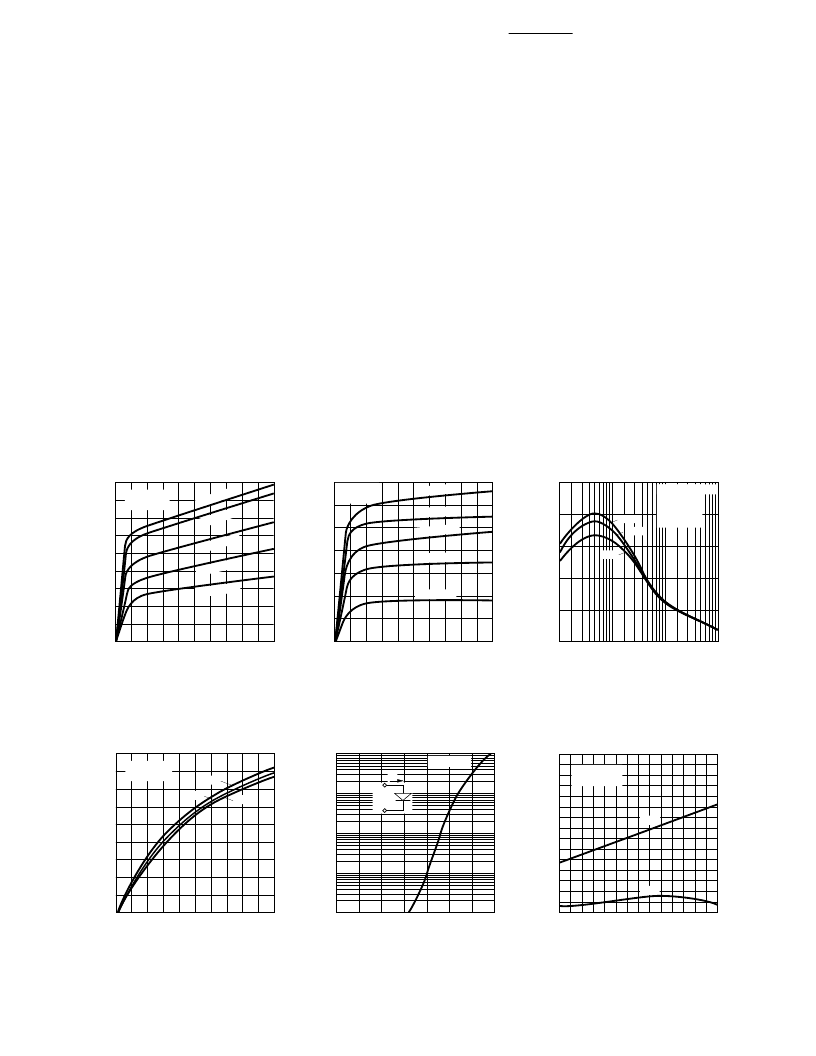
11
Notes:
1. Specification information is available
form the factory for 1.6 V operation.
Call your local field sales office for
further information.
2. DC CURRENT TRANSFER RATIO is
defined as the ratio of output
collector current, I
O
, to the forward
LED input current, I
F
, times 100%.
3. Device considered a two terminal
device: pins 1, 2, 3, and 4 shorted
together, and pins 5, 6, 7, and 8
shorted together.
4. In accordance with UL 1577, each
optocoupler is proof tested by
applying an insulation test voltage
≥
3000 V
RMS
for 1 second (leakage
detection current limit, I
I-O
≤
5
μ
A.
4a. In accordance with UL 1577, each
optocoupler is proof tested by
applying an insulation test voltage
≥
6000 V
RMS
for 1 second (leakage
detection current limit, I
I-O
≤
5
μ
A.
This test is performed before the
100% production test for partial
discharge (Method b) shown in the
VDE 0884 Insulation Characteristics
Table.
5. Measured between pins 1 and 2
shorted together, and pins 3 and 4
shorted together.
6. Common transient immunity in a
Logic High level is the maximum
tolerable (positive) dV
CM
/dt on the
leading edge of the common mode
pulse, V
CM
, to assure that the output
will remain in a Logic High state (i.e.,
V
O
> 2.0 V). Common transient
immunity in a Logic Low level is he
maximum tolerable (negative)
dV
CM
/dt on the trailing edge of the
common mode pulse, V
CM
, to assure
that the output will remain in a Logic
Low state (i.e., V
O
< 0.8 V).
7. In applications where dV/dt may
exceed 50,000 V/
μ
s (such as static
discharge) a series resistor, R
CC
,
should be included to protect the
detector IC form destructively high
surge currents. The recommended
value is R
CC
= 220
.
8. Use of a 0.1
μ
F bypass capacitor con-
nected between pins 8 and 5 adjacent
to the device is recommended.
9. Pin 7 open for single channel product.
10. Use of resistor between pins 5 and 7
will decrease gain and delay time.
Significant reduction in overall gain
can occur when using resistor values
below 47 k
for single channel
product.
11. The Applications Information section
of this data sheet references the
HCPL-47XX part family, but applies
equally to the HCPL-070A and HCPL-
073A parts.
Figure 2. DC Transfer Characteristics
(I
F
= 0.5 mA to 2.5 mA).
Figure 3. DC Transfer Characteristics
(I
F
= 50
μ
A to 250
μ
A).
Figure 4. Current Transfer Ratio vs.
Forward Current.
Figure 5. Output Current vs. Input
Diode Forward Current.
Figure 6. Input Diode Forward
Current vs. Forward Voltage.
Figure 7. Propagation Delay vs.
Temperature.
I
O
0
7
0
V
O
– OUTPUT VOLTAGE – V
2.0
6
5
4
3
2
1
1.0
T
A
= 25°C
V
CC
= 5 V
I
F
= 250
μ
A
I
F
= 200
μ
A
I
F
= 150
μ
A
I
F
= 100
μ
A
I
F
= 50
μ
A
I
F
0.8
0.01
V
F
– FORWARD VOLTAGE
1.5
10
1.0
0.1
0.9
1.3
100
1.0
1.1
1.2
1.4
T
A
= 25°C
I
F
V
F
+
–
I
O
0
27
0
V
O
– OUTPUT VOLTAGE – V
2.0
24
21
18
15
12
9
6
3
1.0
T
A
= 25°C
V
CC
= 5 V
I
F
= 2.5 mA
I
F
= 2.0 mA
I
F
= 1.5 mA
I
F
= 1.0 mA
I
F
= 0.5 mA
N
0.01
1.25
0
I
F
– FORWARD CURRENT – mA
10
0.75
0.5
0.25
0.1
1.0
1.0
25°C
70°C
0°C
NORMALIZED
I
F
= 40
μ
A
V
O
= 0.4 V
V
CC
= 5 V
I
O
0
9
0
I
F
– INPUT DIODE FORWARD CURRENT – mA
0.5
8
7
6
5
4
3
2
1
0.1
V
O
= 0.4 V
V
CC
= 5 V
0.2
0.3
0.4
25°C
0°C
70°C
I
P
0
0
T
A
– TEMPERATURE – °C
70
70
60
50
40
30
20
10
50
I
F
= 0.5 mA
R
L
= 4.7 k
10
20
30
40
60
t
PLH
t
PHL