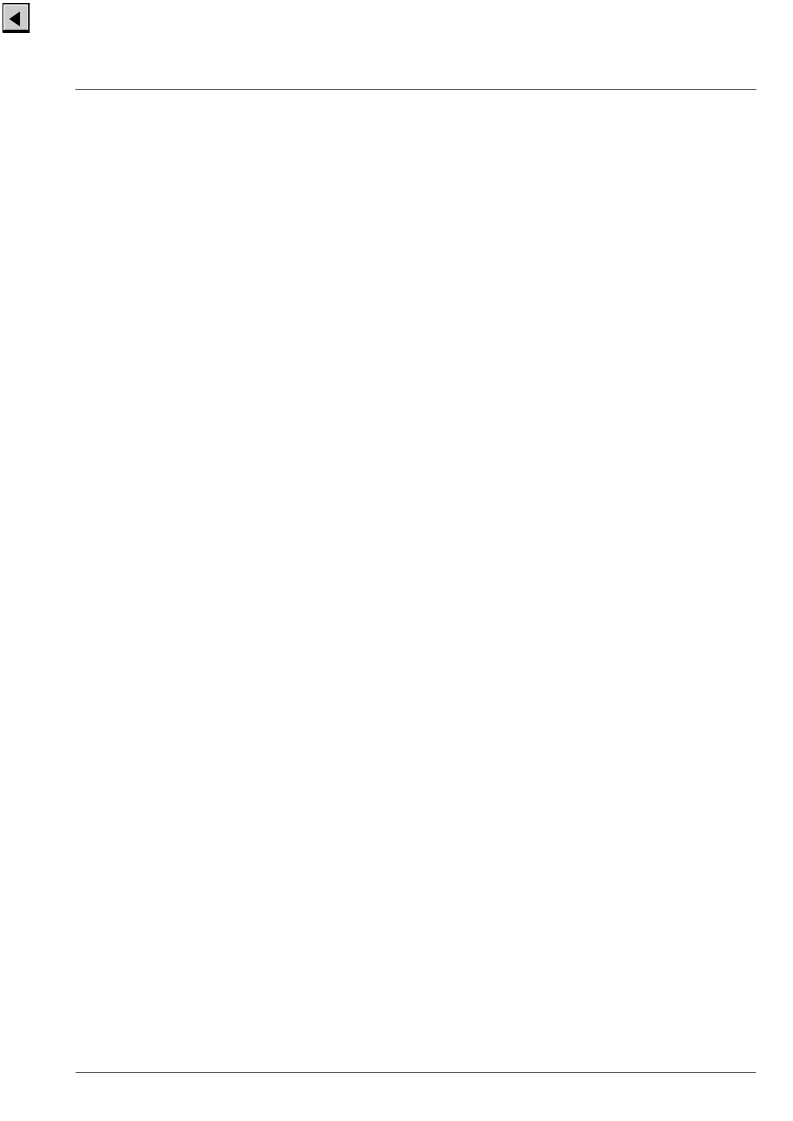
ADVANCE INFORMATION
HAL710
Micronas
11
4. Application Notes
4.1. Ambient Temperature
Due to the internal power dissipation, the temperature
on the silicon chip (junction temperature T
J
) is higher
than the temperature outside the package (ambient
temperature T
A
).
T
J
= T
A
+
T
At static conditions, the following equation is valid:
T = I
DD
* V
DD
* R
th
For typical values, use the typical parameters. For
worst case calculation, use the max. parameters for
I
DD
and R
th
, and the max. value for V
DD
from the appli-
cation.
For all sensors, the junction temperature range T
J
is
specified. The maximum ambient temperature T
Amax
can be calculated as:
T
Amax
= T
Jmax
T
4.2. Extended Operating Conditions
All sensors fulfil the electrical and magnetic character-
istics when operated within the Recommended Oper-
ating Conditions (see page 8)
Supply Voltage Below 3.8 V
Typically, the sensors operate with supply voltages
above 3 V, however, below 3.8 V some characteristics
may be outside the specification.
Note:
The functionality of the sensor below 3.8 V is not
tested. For special test conditions, please contact Mic-
ronas.
4.3. Signal Delay
The extra circuitry required for the direction detection
increases the latency of the
‘
Count and Direction Sig-
nal
’
compared to a simple switch (e.g. HAL 525). This
extra delay corresponds to 0.5 and 1 clock period for
the
‘
Direction Signal
’
and
‘
Count Signal
’
respectively.
4.4. Test Mode Activation
In order to obtain the normal operation as described
above, two external pull-up resistors with appropriate
values are required to connect each output to an exter-
nal supply, such that the potential at the open-drain
output rises to at least 3 V in less than 10
μ
s after hav-
ing turned off the corresponding pull-down transistor or
after having applied V
DD
.
If the
‘
Direction Output
’
is pulled low externally (the
potential does not rise after the internal pull-down tran-
sistor has been turned off), the device enters Manufac-
turer Test Mode.
Direction Detection is not functional in Manufacturer
Test Mode. The device returns to
‘
Normal Operation
’
as soon as the
‘
Count Output
’
goes high.
Please note, that the presence of a Manufacturer Test
Mode requires appropriate measures to prevent acci-
dental activation (e.g. in response to EMC events).
4.5. Start-up Behavior
Due to the active offset compensation, the sensors
have an initialization time (enable time t
en(O)
) after
applying the supply voltage. The parameter t
en(O)
is
specified in the Electrical Characteristics (see page 9)
During the initialization time, the output states are not
defined and the outputs can toggle. After t
en(O)
both
outputs will be either high or low for a stable magnetic
field (no toggling) and the
‘
Count Output
’
will be low if
the applied magnetic field B exceeds B
ON
. The
‘
Count
Output
’
will be high if B drops below B
OFF
. The
‘
Direc-
tion Output
’
will have the correct state after the second
edge (rising or falling) in the same direction.
The device contains a Power-On Reset circuit (POR)
generating a reset when V
DD
rises. This signal is used
to initialize both outputs in the
‘
Off-state
’
(i.e. Output
High) and to disable Test Mode. The generation of this
Reset Signal is guaranteed when V
DD
at the chip rises
to minimum 3.8 V in less than 4
μ
s monotonically. If
this condition is violated, the internal reset signal might
be missing. Under these circumstances the chip will
still operate according to the specification, but the risk
of toggling outputs during t
en(O)
increases and for mag-
netic fields between B
OFF
and B
ON
, the output states
of the Hall sensor after applying V
DD
will be either low
or high. In order to achieve a well defined output state,
the applied magnetic field then must exceed B
ONmax
,
respectively drop below B
OFFmin
.