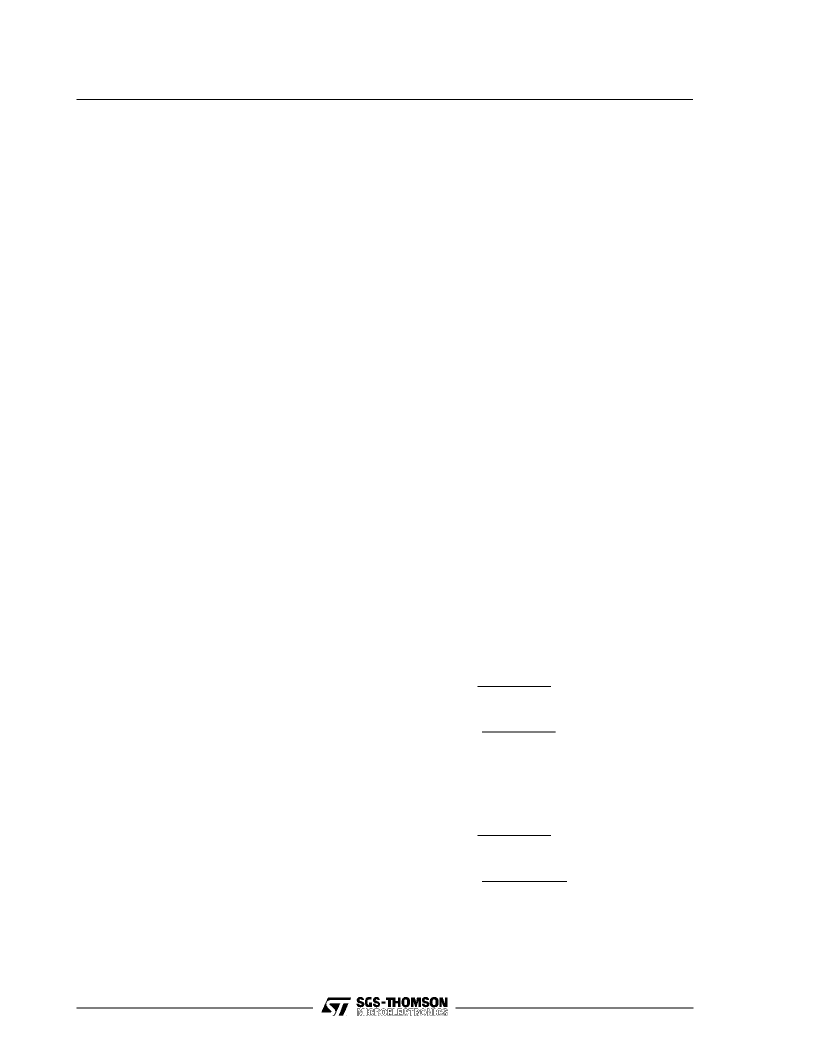
11/17
USER NOTES
Supply Voltage
The recommended operating maximum supply
voltage must include the ripple voltage for the V
s
rail, and a 5V
±
5% for the V
ss
line is required.
The two supply voltages must to be correctly se-
quenced to avoid any possible erroneous position-
ing of the power stages.The correct power-up and
power-down sequences are:
Power-up
1) V
ss
(5V)isapplied withEnable =Low
2) Vs (the motor supply voltage)
is applied
3) Enable is brougth High
Power-down 1) Enable is brougth Low
2) V
s
is switched off
3) V
ss
is switched off.
Case Grounding
The module case is internally connected to pin 1
and 13. To obtain additional effective EMI shield,
the PCBarea below the module can be used as an
effective sixth side shield.
Thermal Characteristics
The case-to-ambient thermal resistance ofthe GS-
D modules is 5
°
C/W. This produces a 50
°
C tem-
perature increase of the module surfacefor 10Wof
internal dissipation.
According to ambient temperature and/or to power
dissipation, an additional heatsink or forced venti-
lation may be required. (See derating curves).
Supply Line Impedance
The module has an internal capacitor connected
accross the supply pins (18 and 13) to assure the
circuit stability. This capacitor cannot handle high
values of currentripple, and would be permanently
damaged if the primary energy source impedance
is not adequate.
The use of a low ESR, high ripple current 470
μ
F
capacitor located as close to the module as possi-
ble is recommended. Suitable units are the SPRA-
GUE type 672D, the SPRAGUE 678D, the RIFA
type PEG 126 or any equivalent unit. When space
is a limitation, a 22
μ
F ceramic multilayer capacitor
connected across the module input pins must be
used.
Module Protections
The GS-D200 outputs are protected against occa-
sional and permanent short-circuits of the output
pin to the supply voltage. The GS-D200S outputs
are also protected against short circuits to ground
and to another output. When the current exceeds
the maximum value, the output is automatically
disabled.
The GS-D200S protection is of the latching type,
i.e. when an overload condition is detected the
unit outputs are disabled. To restart the opera-
tions it is necessary to disable the unit (pin
11=Low) or to switch off the supply voltage for at
least 100ms.
Motor Connection
The motorisnormallyquite far from themodule and
long cables are needed for connection. The use of
a twisted pair cable with appropriate cross section
for each motor phase is recommended to minimize
DC lossesand RFIproblems.
Unused Inputs
All the GS-D200 and GS-D200S logic inputs have
an internal pull-up, and they are high when uncon-
nected.
Phase Current Programming
The outputcurrent of the GS-D200 is factory set to
1A while the GS-D200S has a standard 2A value.
The phase current value can be changed by con-
necting an appropriate resistor between pin 9 and
ground or V
ss
(see fig. 14). In the first case the
phase current will decrease, in the latter it will
increase.
The maximum phase current must be limited to 2A
for the GS-D200 and 2.5A for the GS-D200S to
avoid permanent damage to the module.
GS-D200 phase current programming:
I
>
1A
Ri
=
10
I
0.993
I
1
=
k
Ri
≥
8.2k
I
<
1A
Rd
=
I
1
0.993
I
=
k
GS-D200S phase current programming:
I
>
2A
Ri
=
10
0.33
I
0.473
I
1
=
k
Ri
≥
50 k
I
<
2A
Rd
=
I
3.03
1.43
I
=
k
GS-D200/GS-D200S