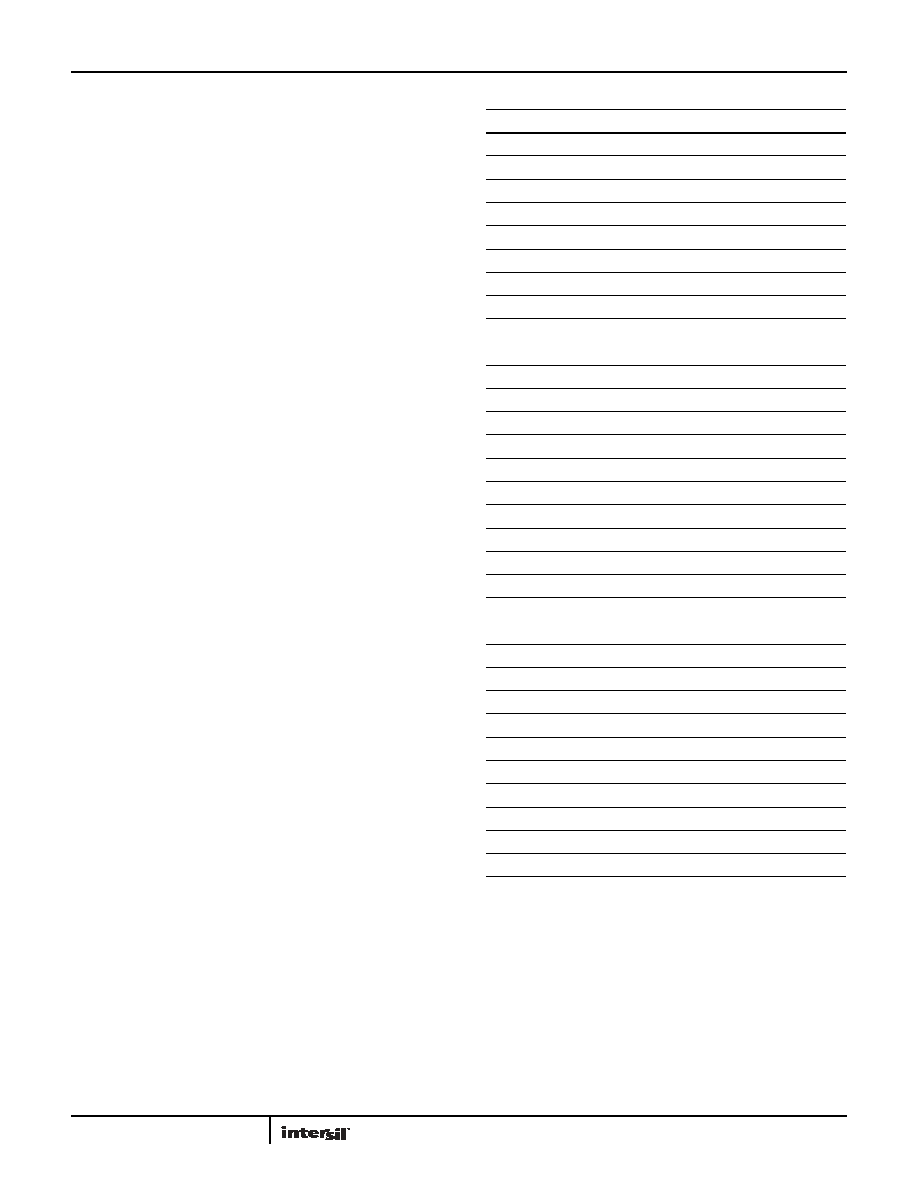
7
FN7441.7
January 12, 2012
Applications Information
EL9115 is a triple analog delay line receiver that allows skew
compensation between any three high frequency signals.
This part compensates for time skew introduced by a typical
CAT-5 cable with differing electrical lengths on each pair.
The EL9115 can be independently programmed via SPI
interface in steps of 2ns up to 62ns total delay on each
channel while achieving over 80MHz bandwidth.
Figure
13 shows the EL9115 block diagram. The three
analog inputs are ground reference single-ended signals.
After the signal is received, the delay is introduced by
switching filter blocks into the signal path. Each filter block is
an all-pass filter introducing 2ns delay. In addition to time
delay, each filter block also introduces some low pass
filtering. As a result, the bandwidth of the signal path
decreases from 120MHz at 0ns delay setting to 80MHz at
the maximum delay setting, as shown in Figure
1 of the
“Typical Performance Curves” on
page 4.In addition to delay, the extra amplifiers in the signal path
also introduce offset voltage. The output offset voltage can
shift by 100mV for X2 high setting and 50mV for X2 low.
In operation, it is best to allocate the most delayed signal
0ns delay and then increase the delay on the other channels
to bring them into line. This will result in the lowest power
and distortion solution to balancing delays.
Power Dissipation
As the delay setting increases, additional filter blocks turn on
and insert into the signal path. For each 2ns of delay per
channel, VSP current increases by 0.9mA while VSM does
not change significantly. Under the extreme settings, the
positive supply current reaches 140mA and the negative
supply current can be 35mA. Operating at ±5V power supply,
the total power dissipation is as shown in Equation
1:
θJA required for long term reliable operation can be
calculated. This is done using Equation
2:where:
TJ is the maximum junction temperature (+135°C)
TA is the maximum ambient temperature (+85°C)
For a 20 Ld package in a proper layout PCB heat-sinking
copper area, 40°C/W
θJA thermal resistance can be
achieved. To disperse the heat, the bottom heat-spreader
must be soldered to the PCB. Heat flows through the
heat-spreader to the circuit board copper then spreads and
convects to air. Thus, the PCB copper plane becomes the
heatsink (see TB389). This has proven to be a very effective
technique. A separate application note, which details the
20 Ld QFN PCB design considerations, is available.
Serial Bus Operation
On the first negative clock edge after NSEnable goes low,
read the input from DATA (Figure
14). This DATA level
should be 0 (write into registers); READ is not supported.
Read the next two data bits on subsequent negative edges
and interpret them as the register to be filled. Reg 01 = R, 02
= G, 03 = B, 00 test use. Read the next five bits of data and
send them to register. At the end of each block of 8 bits, any
further data is treated as being a new word. Data entered is
PD
5
140mA
5
35mA
875mW
=
+
=
(EQ. 1)
θ
JA
T
J
(
T
A ) PD
57
°
=
CW
–
=
(EQ. 2)
TABLE 1. SERIAL BUS DATA
vwxyz
DELAY
00000
0
00001
2
00010
4
00011
6
00100
8
00101
10
00110
12
00111
14
01000
16
01001
18
01010
20
01011
22
01100
24
01101
26
01110
28
01111
30
10000
32
10001
34
10010
36
10011
38
10100
40
10101
42
10110
44
10111
46
11000
48
11001
50
11010
52
11011
54
11100
56
11101
58
11110
60
11111
62
NOTE: Delay register word = 0abvwxyz; Red register - ab = 01;
Green register - ab = 10; Blue register - ab = 11; vwxyz selects delay.
EL9115