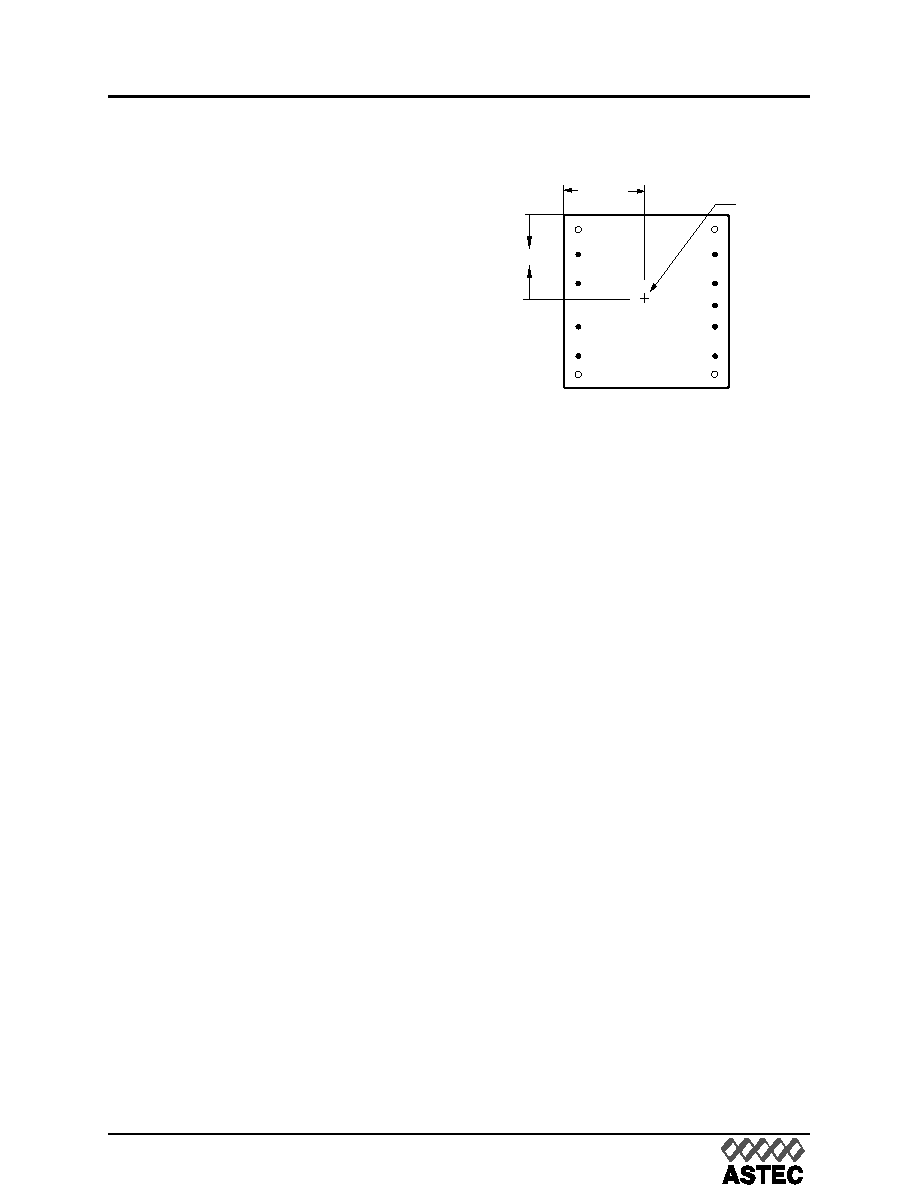
A
A
A E
E
E H
H
H 2
2
2 4
4
4 V
V
V IIIIn
n
n p
p
p u
u
u tttt H
H
H a
a
a llllffff--B
B
B rrrriiiic
c
c k
k
k S
S
S e
e
e rrrriiiie
e
e s
s
s P
P
P o
o
o w
w
w e
e
e rrrr C
C
C o
o
o n
n
n v
v
v e
e
e rrrrtttte
e
e rrrrs
s
2
2 ....5
5
5 V
V
V,,,, 3
3
3 ....3
3
3 V
V
V,,,, 5
5
5 V
V
V S
S
S iiiin
n
n g
g
g lllle
e
e O
O
O u
u
u ttttp
p
p u
u
u tttt,,,, 5
5
5 0
0
0 --1
1
1 5
5
5 0
0
0 W
W
-29-
USA
Europe
Asia
TEL:
1-760-930-4600
44-(0)1384-842-211
852-2437-9662
FAX:
1-760-930-0698
44-(0)1384-843-355
852-2402-4426
www.astec.com
Thermal Management
T
Technologies
echnologies
AEH 24V input series features high efficiency
and the module have typical efficiency high up
to 88% at full load. With less heat dissipation
and temperature-resistant components such as
ceramic capacitors, these modules exhibit good
behavior during prolonged exposure to high
temperatures. Maintaining the operating case
temperature (Tc) within the specified range help
keep internal-component temperatures within
their specifications which in turn help keep
MTBF from falling below the specified rating.
Proper cooling of the power modules is also
necessary for reliable and consistent operation.
Basic Thermal Management
Measuring the case temperature of the module
(Tc) as the method shown in Figure 24 can ver-
ify the proper cooling. Figure 24 shows the
metal surface of the module and the pin loca-
tions. The module should work under 90°C for
the reliability of operation and TC must not
exceed 100 ° C while operating in the final sys-
tem configuration. The measurement can be
made with a surface probe after the module has
reached thermal equilibrium. If a heat sink is
mounted to the case, make the measurement
as close as possible to the indicated position. It
makes the assumption that the final system
configuration exists and can be used for a test
environment.
The following text and graphs show guidelines
to predict the thermal performance of the mod-
ule for typical configurations that include heat
sinks in natural or forced airflow environments.
Note that Tc of module must always be checked
in the final system configuration to verify proper
operational due to the variation in test condi-
tions.
Thermal management acts to transfer the heat
dissipated by the module to the surrounding
environment. The amount of power dissipated
by the module as heat (PD) is got by the equa-
tion below:
PD = PI PO
where : PI is input power;
PO is output power;
PD is dissipated power.
Also, module efficiency (
η) is defined as the fol-
lowing equation:
η = PO / PI
If eliminating the input power term, from two
above equations can yield the equation below:
PD = PO (1-
η )/ η
The module power dissipation then can be cal-
culated through the equation.
Because each power module output voltage
has a different power dissipation curve, a plot of
power dissipation versus output current over
three different line voltages is given in each
module-specific data sheet. The typical power
dissipation curve of AEH series are shown as
figure 25 to figure 30.
29.0 (1.14)
30.5 (1.2)
CNT
Case
+Sense
Trim
– Sense
+Vin
MEASURE CASE
TEMPERATURE HERE
Base-plate side View
Dimensions: millimeters (inches)
-Vin
+Vout
-Vout
Fig.24. Case Temperature Measurement