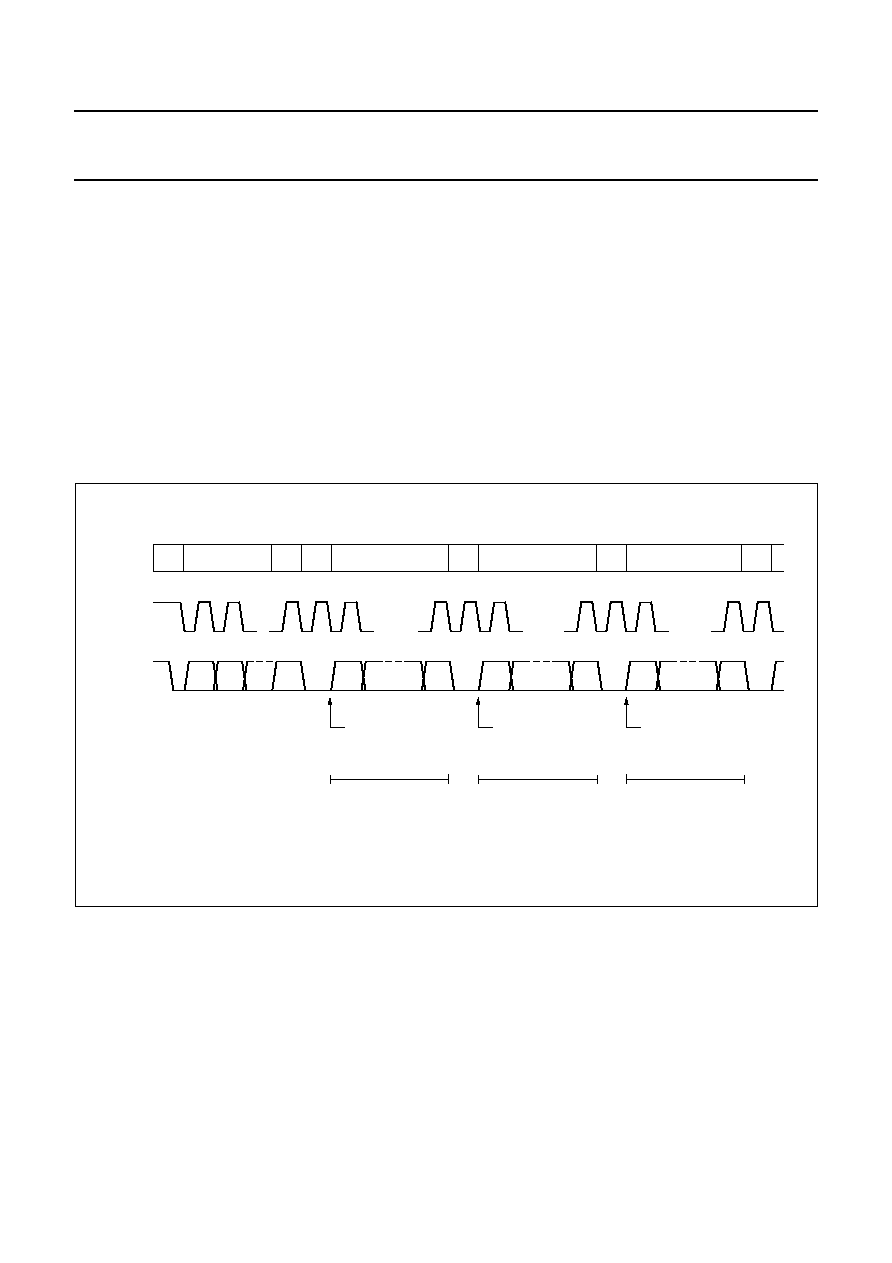
2003 Jan 27
9
Philips Semiconductors
Product specication
8-bit A/D and D/A converter
PCF8591
7.4
A/D conversion
The A/D converter makes use of the successive
approximation conversion technique. The on-chip D/A
converter and a high-gain comparator are used
temporarily during an A/D conversion cycle.
An A/D conversion cycle is always started after sending a
valid read mode address to a PCF8591 device. The A/D
conversion cycle is triggered at the trailing edge of the
acknowledge clock pulse and is executed while
transmitting the result of the previous conversion (see
Fig.9).
Once a conversion cycle is triggered an input voltage
sample of the selected channel is stored on the chip and is
converted to the corresponding 8-bit binary code. Samples
picked up from differential inputs are converted to an 8-bit
twos complement code (see Figs 10 and 11).
The conversion result is stored in the ADC data register
and awaits transmission. If the auto-increment flag is set
the next channel is selected.
The first byte transmitted in a read cycle contains the
conversion result code of the previous read cycle. After a
Power-on reset condition the first byte read is a
hexadecimal 80. The protocol of an I2C-bus read cycle is
shown in Chapter 8, Figs 16 and 17.
The maximum A/D conversion rate is given by the actual
speed of the I2C-bus.
handbook, full pagewidth
S
1
A
ADDRESS
DATA BYTE 1
DATA BYTE 2
DATA BYTE 0
12
9
81
91
PROTOCOL
SCL
SDA
conversion of byte 2
conversion of byte 3
conversion of byte 1
transmission
of previously
converted byte
sampling byte 2
sampling byte 3
sampling byte 1
transmission
of byte 1
transmission
of byte 2
MBL829
Fig.9 A/D conversion sequence.