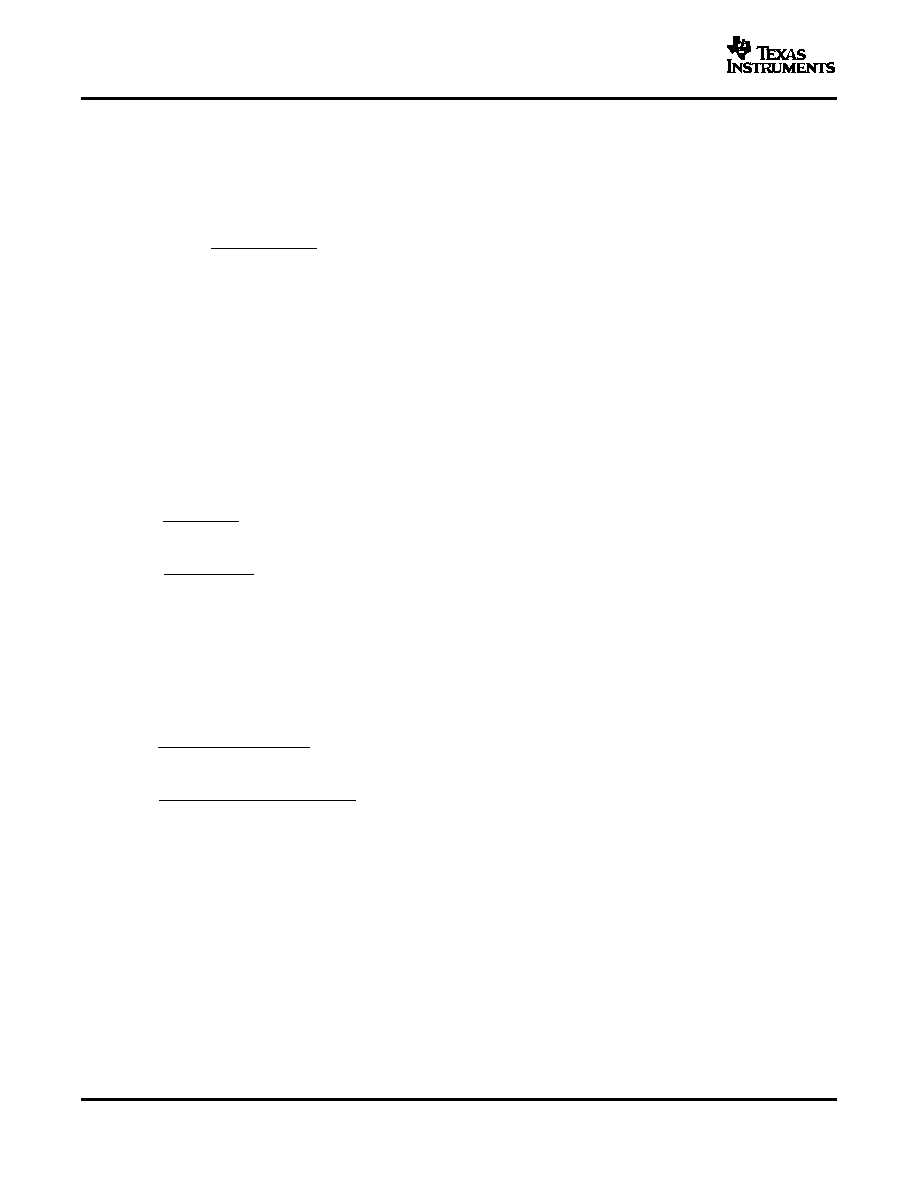
www.ti.com
R3 + R4
V
REF *
V
NEG
V
REF
* 1
(2)
Inductor Selection
I
LP +
V
POS
V
IN
0.64
I
OUTP
(3)
I
LN +
V
IN *
V
NEG
V
IN
0.64
I
OUTN
(4)
L
P +
V
IN
V
POS *
V
IN
DILP
f
S
V
POS
(5)
L
N +
V
IN
V
NEG
DILN
f
S
V
NEG *
V
IN
(6)
TPS65130, TPS65131
SLVS493B – MARCH 2004 – REVISED SEPTEMBER 2004
APPLICATION INFORMATION (continued)
considerations are similar to the considerations at the boost converter. For the same reasons, the feedback
divider current should be in the range of 5 A or higher. The voltage across R4 is 1.213 V. Based on those
values, the recommended value for R4 should be lower than 200 k in order to set the divider current at the
required value. The value of the resistor R3, depending on the needed output voltage (VNEG), can be calculated
using Equation 2:
If as an example an output voltage of –5 V is needed and a resistor of 180 k
has been chosen for R
4, a 750-k
resistor is needed to program the desired output voltage.
An inductive converter normally requires two main passive components for storing energy during the conversion.
An inductor and a storage capacitor at the output are required. In selecting the right inductor, it is recommended
to keep the possible peak inductor current below the current-limit threshold of the power switch in the chosen
configuration. For example, the current-limit threshold of the switch for the boost converter and for the inverting
converter, is nominally 800 mA at TPS65130 and 1950 mA at TPS65131. The highest peak current through the
switches and the inductor depend on the output load, the input voltage (VIN), and the output voltages (VPOS,
VNEG). Estimation of the peak inductor current in the boost converter can be done using Equation 3. Equation 4
shows the corresponding formula for the inverting converter.
The second parameter for choosing the inductor is the desired current ripple in the inductor. Normally, it is
advisable to work with a ripple of less than 20% of the average inductor current. A smaller ripple reduces the
losses in the inductor, as well as output voltage ripple and EMI. But in the same way, output voltage regulation
gets slower, causing higher voltage changes at fast load changes. In addition, a larger inductor usually increases
the total system cost. Keeping those parameters in mind, the possible inductor value can be calculated using
Equation 5 for the boost converter and Equation 6 for the inverting converter.
Parameter f is the switching frequency and
I
L is the ripple current in the inductor, i.e., 20% x IL. VIN is the input
voltage, which is assumed to be at 3.3 V in this example. So, the calculated inductance value for the boost
inductor is 5.1 H and for the inverting converter inductor is 5.1 H. With these calculated values and the
calculated currents, it is possible to choose a suitable inductor. In typical applications, a 4.7-H inductor is
recommended. The device has been optimized to work with inductance values between 3.3 H and 6.8 H.
Nevertheless, operation with higher inductance values may be possible in some applications. Detailed stability
analysis is then recommended. Care has to be taken for the possibility that load transients and losses in the
circuit can lead to higher currents as estimated in Equation 3 and Equation 4. Also, the losses caused by
magnetic hysteresis losses and copper losses are a major parameter for total circuit efficiency.
24