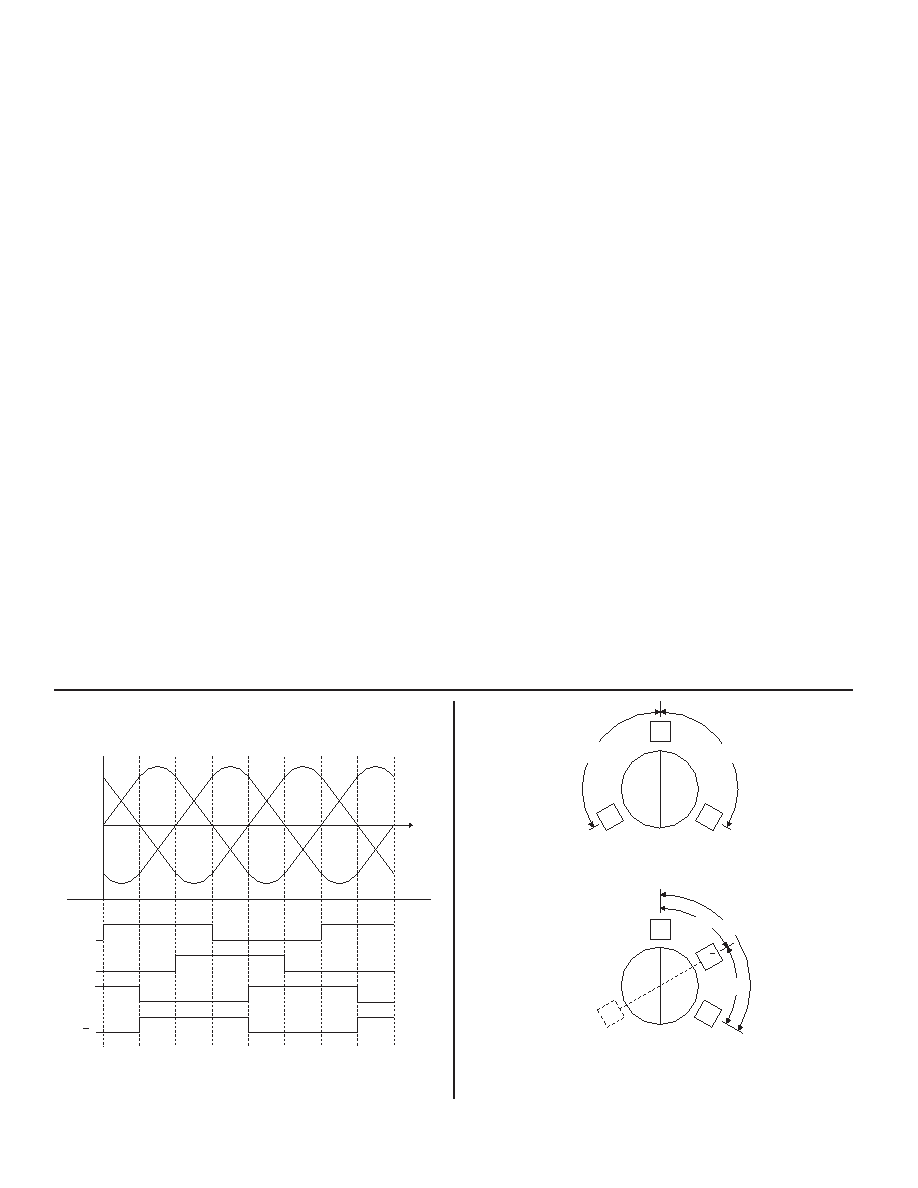
8
Data Device Corporation
www.ddc-web.com
PW-82520/21N
G-06/05-0
“1” (or HIGH ) is defined by an input greater than 3.5Vdc or an
open circuit to the controller; Logic “0”(or LOW) is defined as any
Hall voltage input less than 1.5Vdc. Internal to the PW-
82520/21N are 10K pull-up resistors tied to +5Vdc on each Hall
input.
The PW-82520/21N will alternately operate with Hall phasing of
60° electrical spacing. If 60° commutation is used, then the out-
put of HC must be inverted as shown in FIGURES 4 and 5.
FIGURE 4 illustrates the Hall sensor outputs along with the cor-
responding back emf voltage they are in phase with.
HALL INPUT SIGNAL CONDITIONING
When the motor is located more than two feet away from the PW-
82520/21N controller or is in a noisy electrical environment the
Hall inputs require filtering from noise. It is recommended to use
a 100
resistor in series with the Hall signal and a 2000 pF
capacitor from the Hall input pin to the Hall supply ground pin as
shown in FIGURES 6 and 7.
PHASE A, B, C
These are the power drive outputs to the motor and switch
between VBUS+ Input and VBUS- Input or become high imped-
ance (see TABLE 3).
VDR (+15V SUPPLY)
This input is used to power the gate driver circuitry for the output
MOSFETs. There is no power consumption from VDR when the
hybrid is disabled.
VDD (+5V TO +15V SUPPLY), VEE (-5V TO -15V SUPPLY)
These inputs can vary from ±5V to ±15V as long as they are
symmetrical. VDD and VEE are used to power the small signal
analog circuitry of the hybrid. Please note that using ±5V supply
will reduce the quiescent power consumption by approximately
60% when compared to ±15V operation.
SUPPLY GND
This pin is the return for the VDR, VEE and VDD supplies. The
phase current sensing technique of the PW-82520N/21N
requires that VBUS- and SUPPLY GND (see FIGURES 6 and 7)
be connected together externally (see VBUS- supply).
CASE GND
This pin is internally connected to the hybrid case. In some applica-
tions the user may want to tie this to Ground for EMI considerations.
HALL A, B, C SIGNALS
These are logic signals from the motor Hall-effect sensors. They
use a phasing convention referred to as 120 degree spacing; that
is, the output of HA is in phase with motor back EMF voltage
VAB, HB is in phase VBC, and HC is in phase with VCA. Logic
HALL-EFFECT SENSOR PHASING vs.
MOTOR BACK EMF FOR CW ROTATION (120
° Commutations)
300
°
0
°
60
°
120
°
180
°
240
°
300
° 360°/0°
60
°
V
AB
V
BC
V
CA
BACK EMF
OF MOTOR
ROTATING
CW
HA
HB
HC
In Phase
with V
AB
In Phase
with V
BC
In Phase
with V
CA
In Phase
with V
AC
(60)
FIGURE 4. HALL PHASING
S
HC
HA
120
°
N
HB
120
°
N
HC
120
°
REMOTE POSITION SENSOR (HALL) SPACING FOR
120 DEGREE COMMUTATION
60
°
60
°
REMOTE POSITION SENSOR (HALL) SPACING FOR
60 DEGREE COMMUTATION
S
HA
HB
HC
FIGURE 5. HALL SENSOR SPACING