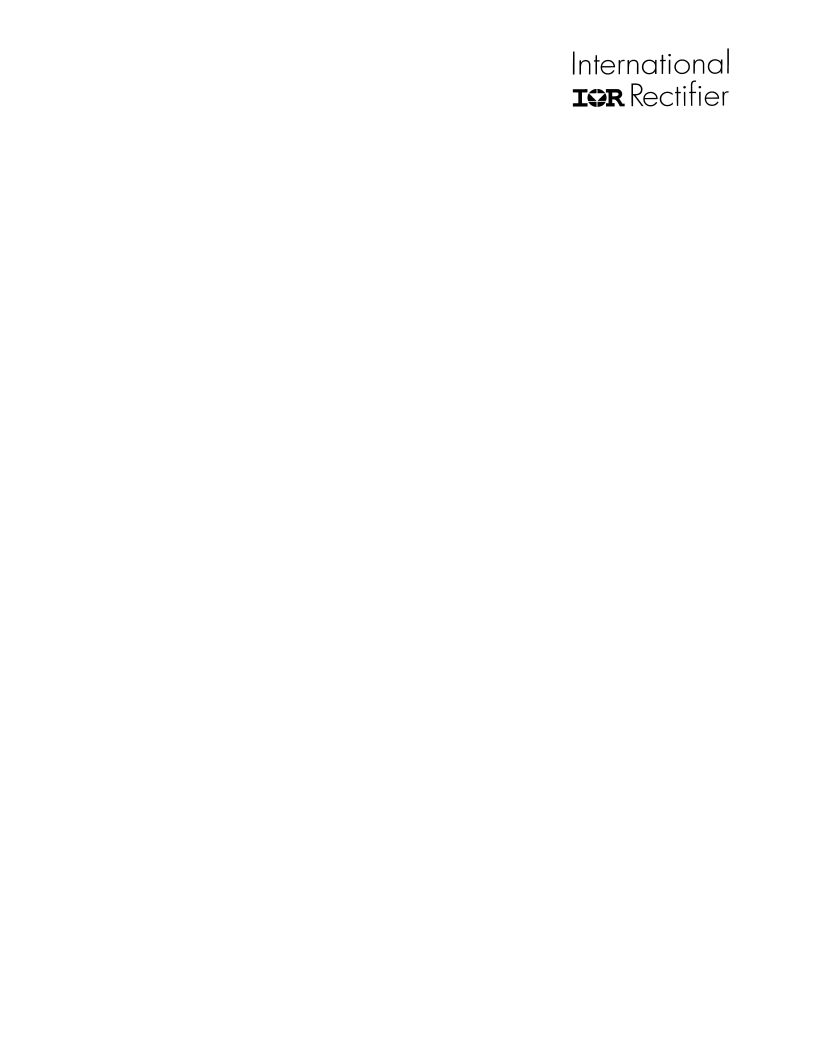
www.irf.com
11
PIIPM25P12B008
I27147 01/03
General Description
The PI-IPM is a new generation of Intelligent
Power
Module
designed
implement itself a complete motor driver system.
The device contains all peripherals needed to
control a six IGBTs inverter, including voltage,
temperature
and
current
completely interfaced with a 40Mips DSP, the
TMS320LF2406A from Texas Instruments. All
communication between the DSP and the local
host, including DSP software installing and
debugging, is realized through an asynchronous
isolated serial port (SCI), an isolated port for
incremental encoder inputs or synchronous serial
port communication (SPI) is also provided
making
this
module
programmable solution connected to the system
only through a serial link cable.
System Description
The PI-IPM is realized in two distinct parts: the
Power Module “EMP” and the Embedded
Driving Board “EDB,” these two elements
assembled together constitute the complete
device with all performances described in the
following.
specifically
to
output
sensing,
a
complete
user
The complete block schematic showing all
functions implemented in the product is
represented on the System Block Schematic on
page 1. The new module concept includes
everything depicted within the dotted line, the
EMP power module includes IGBTs, Diodes and
Sensing Resistors while all remaining electronics
is assembled on the EDB that is fitted on the top
of it as a cover with also mechanical protective
functions.
Connections between the two parts are realized
through a single-in-line connector and the EDB
only, without disassembling the power module
from the system mechanic, can be easily
substituted “at the factory” for an upgrade, a
system configuration change (different control
architecture) or a board replacement. Also
software upgrades are possible but this does not
even require any hardware changes thanks to the
DSP programmability through the serial or JTAG
ports.
T
HE
“EMP
TM
” P
OWER
M
ODULE
This module contains six IGBTs + HexFreds
Diodes in a standard inverter configuration.
IGBTs used are the new NPT 1200V-25A
(current rating measured @ 100C), generation V
from International Rectifier; the HexFred diodes
have been designed specifically as pair elements
for these power transistors. Thanks to the new
design and technologic realization, this gen V
devices do not need any negative gate voltage for
their complete turn off and the tail effect is also
substantially reduced compared to competitive
devices of the same family. This feature
simplifies the gate driving stage that will be
described in a dedicated chapter. Another not
standard feature in this type of power modules is
the presence of sensing resistors in the three
output phases, for precise motor current sensing
and short circuit protections, as well as another
resistor of the same value in the DC bus minus
line, needed only for device protections purposes.
A complete schematic of the EMP module is
shown on page 1 where sensing resistors have
been clearly evidenced, a thermal sensor is also
embedded and directly coupled with the DSP
inputs.
The package chosen is mechanically compatible
with the well known EconoPack outline, also the
height of the plastic cylindrical nuts for the
external PCB positioned on its top is the same, so
that, with the only re-layout of the main
motherboard, this module can fit into the same
mechanical fixings of the standard Econo II
package thus speeding up the device evaluation
in an already existing driver.
An important feature of this new device is the
presence of Kelvin points for all feedback and
command signals between the board and the
module with the advantage of having all emitter
and resistor sensing independent from the power
path. The final benefit is that all low power
signal from/to the controlling board are
unaffected by parasitic inductances or resistances
inevitably present in the module power layout.