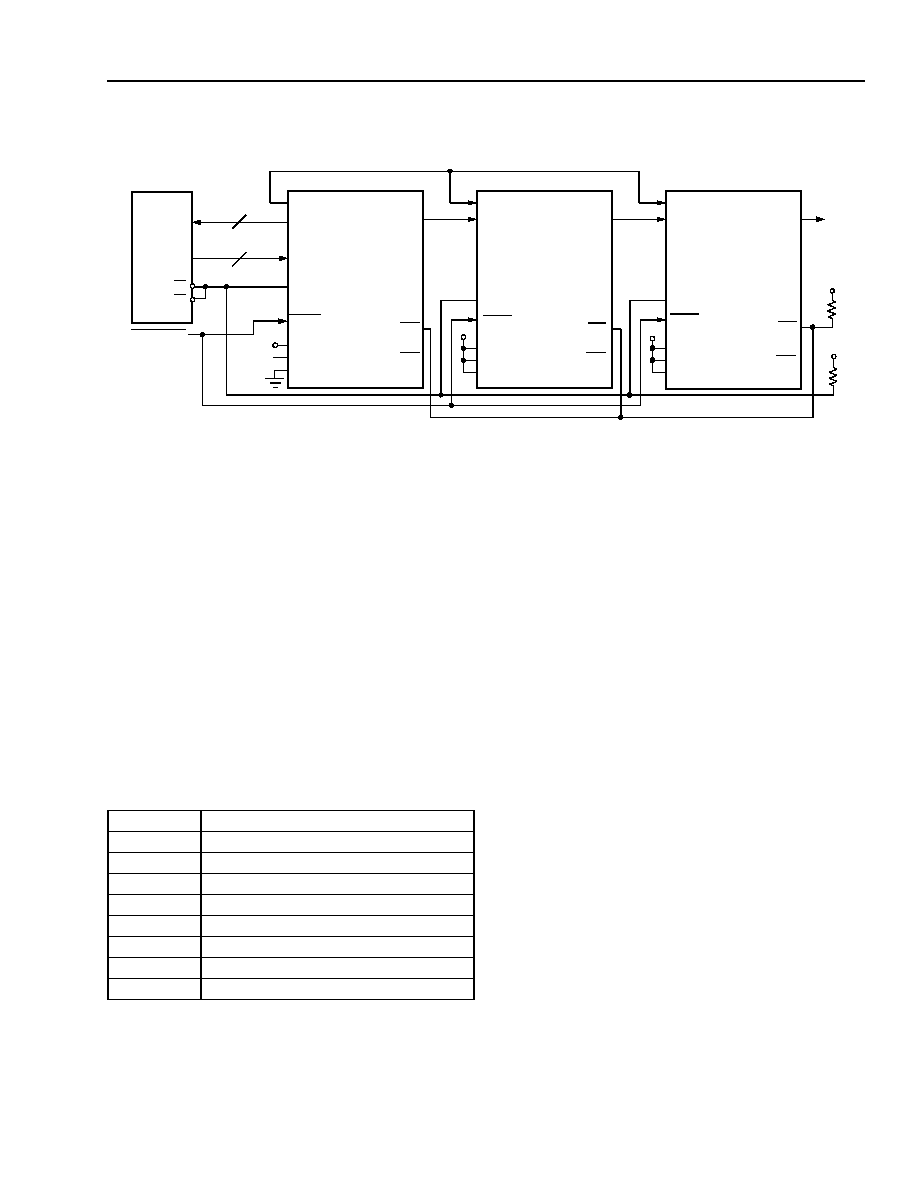
Data Sheet
June 1999
ORCA Series 2 FPGAs
Lucent Technologies Inc.
55
Special Function Blocks (continued)
5-4488(F)
Figure 48. Boundary-Scan Interface
VDD
EPROM
PROGRAM
D[7:0]
OE
CE
A[17:0]
D[7:0]
DONE
M2
M1
M0
DONE
HDC
LDC
RCLK
CCLK
DOUT
DIN
DOUT
DIN
CCLK
DONE
DOUT
INIT
CCLK
VDD
VDD OR
GND
PRGM
M2
M1
M0
PRGM
M2
M1
M0
VDD
HDC
LDC
RCLK
HDC
LDC
RCLK
VDD
ORCA
SERIES
FPGA
SLAVE #2
ORCA
SERIES
FPGA
MASTER
ORCA
SERIES
FPGA
SLAVE #1
The BSM also increases test throughput with a dedi-
cated automatic test-pattern generator and with com-
pression of the test response with a signature analysis
register. The PC-based boundary-scan test card/soft-
ware allows a user to quickly prototype a boundary-
scan test setup.
Boundary-Scan Instructions
The
ORCA Series boundary-scan circuitry is used for
three mandatory
IEEE 1149.1 tests (EXTEST, SAM-
PLE/PRELOAD, BYPASS) and four
ORCA-defined
instructions. The 3-bit wide instruction register sup-
ports the eight instructions listed in
Table 12.Table 12. Boundary-Scan Instructions
The external test (EXTEST) instruction allows the inter-
connections between ICs in a system to be tested for
opens and stuck-at faults. If an EXTEST instruction is
performed for the system shown in
Figure 47, the con-
nections between U1 and U2 (shown by nets a, b, and
c) can be tested by driving a value onto the given nets
from one device and then determining whether the
same value is seen at the other device. This is deter-
mined by shifting 2 bits of data for each pin (one for the
output value and one for the 3-state value) through the
BSR until each one aligns to the appropriate pin.
Then, based upon the value of the 3-state signal, either
the I/O pad is driven to the value given in the BSR, or
the BSR is updated with the input value from the I/O
pad, which allows it to be shifted out TDO.
The SAMPLE instruction is useful for system debug-
ging and fault diagnosis by allowing the data at the
FPGA’s I/Os to be observed during normal operation.
The data for all of the I/Os is captured simultaneously
into the BSR, allowing them to be shifted-out TDO to
the test host. Since each I/O buffer in the PICs is bidi-
rectional, two pieces of data are captured for each I/O
pad: the value at the I/O pad and the value of the
3-state control signal.
Code
Instruction
000
EXTEST
001
PLC Scan Ring 1
010
RAM Write (RAM_W)
011
Reserved
100
SAMPLE/PRELOAD
101
PLC Scan Ring 2
110
RAM Read (RAM_R)
111
BYPASS