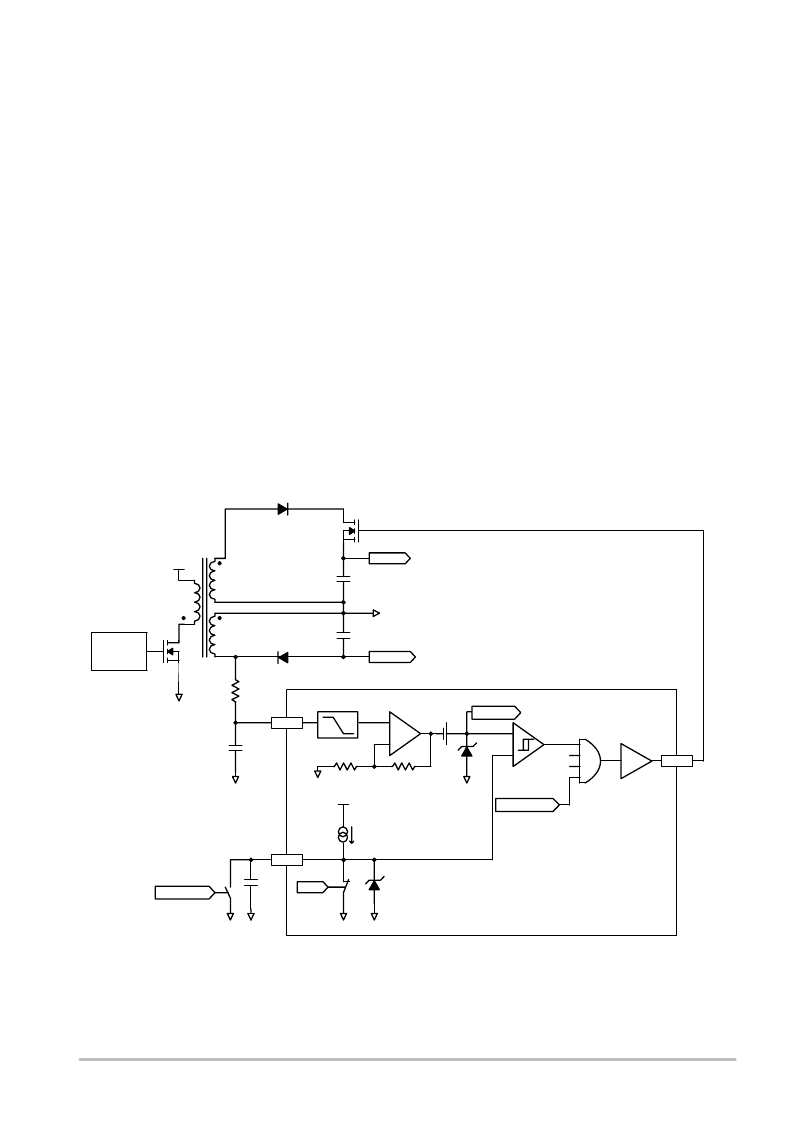
NCP4326
http://onsemi.com
23
Flux Image Reconstruction
With a primary controller working in critical conduction
mode the core flux inside the transformer is null at each
beginning primary switching cycle.
Measuring the flux means integrating the voltage present
on a transformer winding. But a simple integration yields a
saw tooth voltage waveform centered to zero volts. Thus this
saw tooth represents the flux variation in the transformer
core and must be offset in order to have a true image of the
flux with a minimum voltage close to zero volts.
What we need is a triangle with a FIXED lower level,
being equal to or somewhat above zero. This necessitates the
resetting of the integrator at the beginning of each primary
ontime. In practice, it means we quickly discharge the
integrator capacitor just before the primary ontime and
release this capacitor at the start of the primary ontime.
A negative auxiliary winding or a forward winding can be
used to build the flux image via a simple RC network, which
it ensures the integration then the NCP4326 fixes the lower
level.
Figure 46 shows how the flux image is built and used for
the softstart sequence.
The RC network (Rint & Cint) connected to the negative
output winding does the integration of the voltage present on
this winding that it yields the flux image. Then the voltage
available on Flux pin is clamped between a low and high
level (respectively V
Flux_L
and V
Flux_H
) in order to ensure
a positive saw tooth on Flux pin. After that the voltage on
Flux pin is amplified 10 times and an offset is inserted to
ensure the disable function when the enable pin is below
V
ENX_TH1
. More over the internal voltage clamp
(V
ENX_TH2
= 4.5 V) ending the softstart duty cycle
generation when the voltage on enable pin is between
V
ENX_TH2
and V
ENX_max1
.
Next the internal Flux image (label Int_Flux on Figure 46)
is compared with the enable pin voltage for generating the
softstart duty cycle in leading edge mode control.
On enable pin we have an internal current source that it
charge the external capacitor and fix the softstart time by
playing with the capacitor value. If the controller is placed
in standby mode then the enable capacitor is discharged by
the internal switch. The internal clamp limits the voltage
range on the enable pin.
Flux
ENx
IENx
GND
+
5V0
GND
0V
1V
+
9R
R
GND
Clamp
Int_Flux
4V5
Offset
0V5
Cint
GND
Rint
D2
C2
Neg Out
GND
T1
D1
C1
Pos Out
GND
Normal_Reg
C_SS
GND
DRVx
PWM_SS
PWM_REG
Q1
GND
ENx_CMD
Q2
HV Rail
GND
Primary
Controller
SoftStart Secondary Controller
Figure 46. SoftStart Detailed Schematic View
V
DD
V
DD
+
+
+