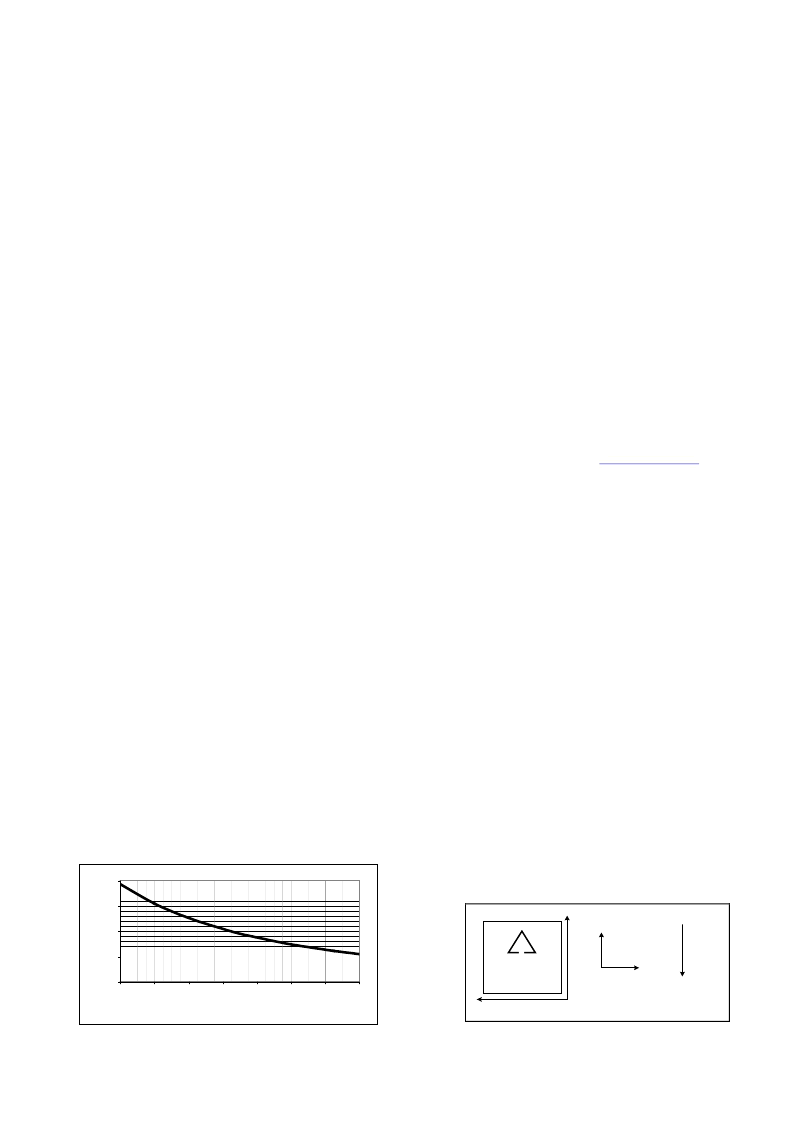
or 400 Hz. The user should ensure the load impedance is
sufficiently high as to not source/sink >100
μ
A typical.
While the sensitivity of this axis has been programmed at
the factory to be the same as the sensitivity for the x-axis,
the
accelerometer
can be programmed for non-equal
sensitivities on the x- and y-axes. Contact the factory for
additional information.
T
OUT
– This pin is the buffered output of the temperature
sensor. The analog voltage at T
OUT
is an indication of the
die temperature. This voltage is useful as a differential
measurement of temperature from ambient and not as an
absolute measurement of temperature. After correlating the
voltage at T
OUT
to 25
°
C ambient, the change in this voltage
due to changes in the ambient temperature can be used to
compensate for the change over temperature of the
accelerometer offset and sensitivity. Please refer to the
section on Compensation for the Change in Sensitivity
Over Temperature for more information.
Sck
– The standard product is delivered with an internal
clock option (800kHz).
This pin should be grounded
when operating with the internal clock.
An external
clock option can be special ordered from the factory
allowing the user to input a clock signal between 400kHz
And 1.6MHz
V
ref
– A reference voltage is available from this pin. It is
set at 2.50V typical and has 100
μ
A of drive capability.
COMPENSATION FOR THE CHANGE IN
SENSITIVITY OVER TEMPERATURE
All thermal accelerometers display the same sensitivity
change with temperature. The sensitivity change depends
on variations in heat transfer that are governed by the laws
of physics. Manufacturing variations do not influence the
sensitivity change, so there are no unit to unit differences in
sensitivity change. The sensitivity change is governed by
the following equation (and shown in Figure 1 in
°
C):
S
i
x T
i
where S
i
is the sensitivity at any initial temperature T
i
, and
S
f
is the sensitivity at any other final temperature T
f
with
the temperature values in
°
K and the sensitivity expressed
in % duty cycle/g.
MEMSIC MXD2002A/B Rev.E
Page 4 of
8
5/15/2004
2.67
= S
f
x T
f
2.67
0.0
0.5
1.0
1.5
2.0
-40
-20
0
20
40
60
80
100
Temperature (C)
S
Figure 1: Thermal Accelerometer Sensitivity
In gaming applications where the game or controller is
typically used in a constant temperature environment,
sensitivity might not need to be compensated in hardware
or software. The compensation for this effect could be
done instinctively by the game player.
For applications where sensitivity changes of a few percent
are acceptable, the above equation can be approximated
with a linear function. Using a linear approximation, an
external circuit that provides a gain adjustment of –0.9%/
°
C
would keep the sensitivity within 10% of its room
temperature value over a 0
°
C to +50
°
C range.
For applications that demand high performance, a low cost
micro-controller can be used to implement the above
equation. A reference design using a Microchip MCU (p/n
16F873/04-SO) and MEMSIC developed firmware is
available by contacting the factory. With this reference
design, the sensitivity variation over the full temperature
range (-40
°
C to +105
°
C) can be kept below 3%. Please
visit the MEMSIC web site at
www.memsic.com
for
reference design information on circuits and programs
including look up tables for easily incorporating sensitivity
compensation.
DISCUSSION OF TILT APPLICATIONS AND
MINIMUM RESOLUTION
Tilt Applications:
One of the most popular applications of
the MEMSIC accelerometer product line is in
tilt/inclination measurement. An accelerometer uses the
force of gravity as an input to determine the inclination
angle of an object.
A MEMSIC accelerometer is most sensitive to changes in
position, or tilt, when the accelerometer’s sensitive axis is
perpendicular to the force of gravity, or parallel to the
Earth’s surface. Similarly, when the accelerometer’s axis is
parallel to the force of gravity (perpendicular to the Earth’s
surface), it is least sensitive to changes in tilt.
Table 1 and Figure 2 help to illustrate the output changes in
the X- and Y-axes as the unit is tilted from +90
°
to 0
°
.
Notice that when one axis has a small change in output per
degree of tilt (in m
g
), the second axis has a large change in
output per degree of tilt. The complementary nature of
these two signals permits low cost accurate tilt sensing to
be achieved with the MEMSIC device (reference
application note AN-00MX-007).
X
Top View
Y
+90
0
0
0
gravity
M
Figure 2: Accelerometer Position Relative to Gravity