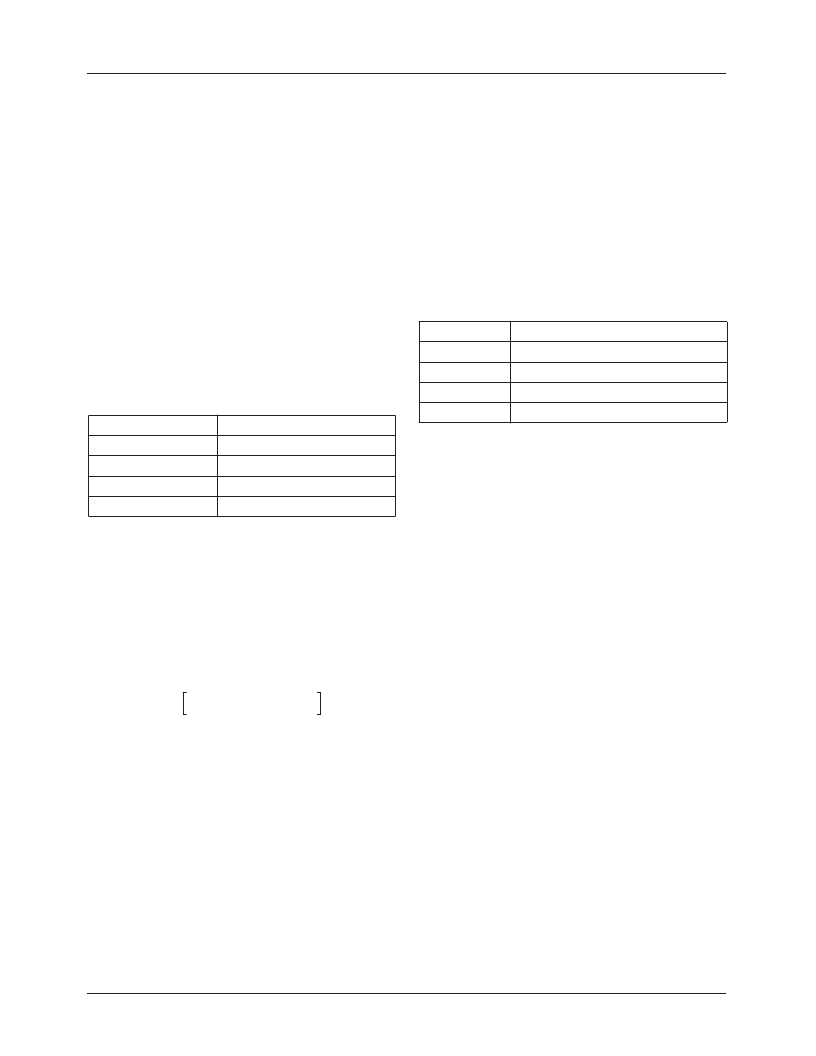
PRODUCT SPECIFICATION
ML4854
10
REV. 1.0.7 5/6/03
improve the design by enlarging the capacitor or using
smaller capacitors in parallel to reduce the ESR or by using
better capacitors with lower ESR.
Tradeoffs have to be made between performance and costs of
the external parts of the converter circuit. For common, gen-
eral purpose applications, a ceramic output capacitor with a
capacitance of 47μF and ESR less than 0.1
could be a good
choice. If a tantalum capacitor is used, a 100nF ceramic
capacitor in parallel, placed close to the IC, is recommended.
Input Capacitor Selection
Since the ML4854 does not require a large decoupling
capacitor at the input to operate properly, a 47μF capacitor is
sufficient for most applications requiring a good transient
response of the regulator. Optimum efficiency occurs when
the capacitor value is large enough to decouple the source
impedance. This usually occurs for capacitor values in
excess of 47μF.
Table 1. Recommended capacitors
Inductor Selection
To select the boost inductor, it is necessary to keep the possi-
ble peak inductor current below the absolute peak current
limit of the power switch of the device. The highest peak
current through the inductor and the switch depends on the
load current (I
LOAD
), the input voltage(V
IN
) and the output
voltage (V
OUT
).
The maximum load current depends upon the inductance L,
according to the equation:
where, by design, t
OFFmin
= 0.5μS, I
LIM
= 0.8A and the
efficiency
η
is usually 0.9. For V
IN
=3V, V
OUT
=5V the
resulting I
LOADmax
will be around 0.4A.
The second parameter for choosing the inductor is the
desired current ripple in the inductor. Normally, it is advis-
able to work with a ripple of less than 20% of the average
inductor current. A larger inductor value provides a smaller
ripple which reduces the magnetic hysteresis losses in the
inductor, as well as output voltage ripple and EMI. But in the
same way, regulation time at load changes will rise. Due to
the nature of the “go/no go” control, larger inductor values
typically result in larger overall voltage ripple, because once
the output voltage level is satisfied, the converter goes dis-
continuous, resulting in the residual energy of the inductor,
causing overshoot. The losses in the inductor caused by
magnetic hysteresis losses and copper losses are a major
parameter for total circuit efficiency. For better efficiency the
ESR of the inductor should be kept as low as possible. Lower
value inductors typically offer lower ESR and smaller
physical size.
An inductor value of 10 μH works well in most applications,
but values between 5 μH to 22 μH are also acceptable. A
MuRata LQ66C100M4, 10μH surface-mount inductor is
suitable, having a current rating of 1.6A and a max. ESR of
36 m
. Other choices for surface-mount inductors are
shown in Table 2.
Table 2. Recommended Inductors
Thermal considerations
Implementation of integrated circuits in low-profile surface-
mount packages typically requires special attention to power
dissipation. Many system-dependent issues such as thermal
coupling, airflow, added heat sinks and convection surfaces,
and the presence of other heat-generating components affect
the power-dissipation limits of a given component.
Three basic approaches for enhancing thermal performance
are:
Improving the power dissipation capability of the PCB
design
Improving the thermal coupling of the component to the
PCB
Introducing airflow in the system
The maximum junction temperature, T
J (MAX)
of the
ML4854 devices is 150°C. The thermal resistance of the
8-pin TSSOP package (T08) is
θ
JA
= 124°C/W. Specified
regulator operation is assured to a maximum ambient
temperature T
A(MAX)
of 85°C. Therefore, the maximum
power dissipation is about 320 mW. More power can be dis-
sipated if the maximum ambient temperature of the applica-
tion is lower, according to the relation:
P
D(MAX)
= [T
J(MAX)
–T
A(MAX)
] /
θ
JA
Layout and Grounding
Considerations
Careful design of printed circuit board is recommended since
high frequency switching and high peak currents are present
in DC/DC converters applications. A general rule is to place
the converter circuitry well away from any sensitive analog
Vendor
MuRata
AVX
Sprague
Kemet
Description
X5R Ceramic
TAJ,TPS series tantalum
595D series tantalum
T494 series tantalum
I
LOADmax
V
IN
I
LIM
---------------------------------V
t
OFFmin
V
------------------------------
V
–
–
OUT
η
×
=
Supplier
MuRata
Coilcraft
Coiltronics
Sumida
Manufacturer Part Number
LQ66C100M4
DT1608C-103
UP1B100
CDR63B-100