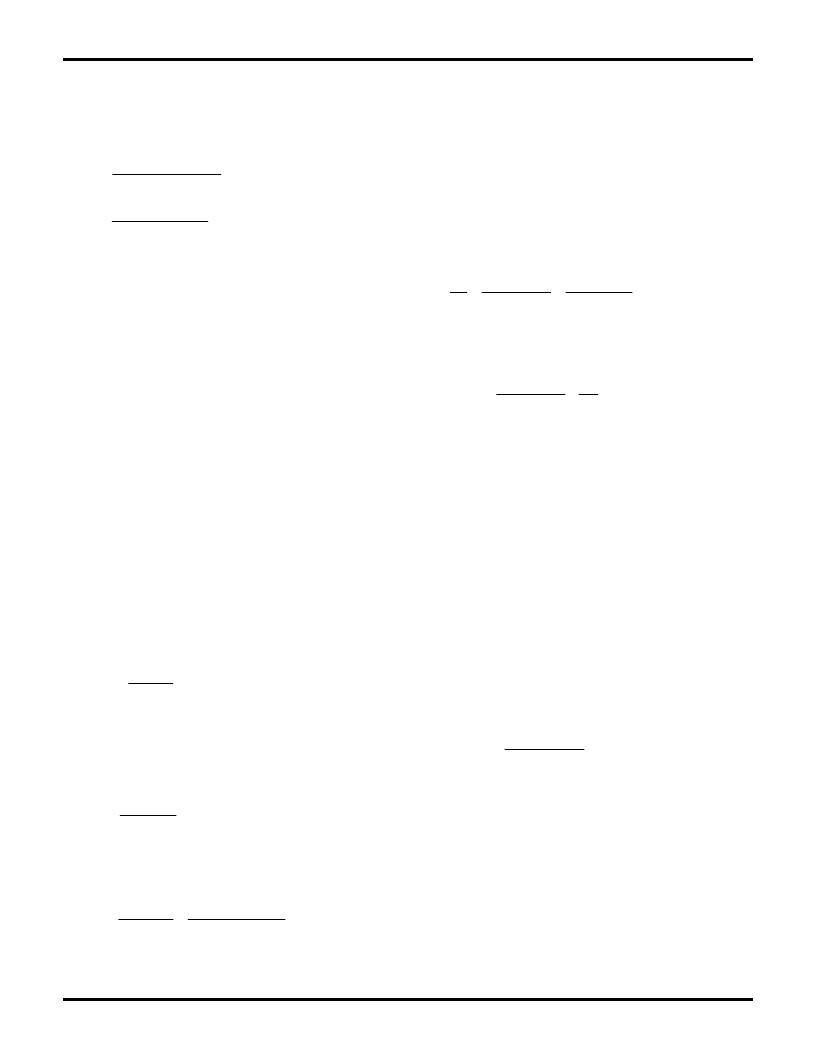
ML4819
10
REV. 1.0 10/10/2000
then:
I
LDRY
= 100mA
Step 3: The value of the inductance can now be found
using previously calculated data.
L
V
D
×
)
I
f
V
mA
kHz
mH
2
INDRY
ON MAX
(
L DRY
(
OSC
1
20
0 95
100
100
=
×
=
×
×
=
)
.
(5)
The inductor can be allowed to decrease in value when
the current sweeps from minimum to maximum value.
This allows the use of smaller core sizes. The only
requirement is that the ramp compensation must be
adequate for the lower inductance value of the core so
that there is adequate compensation at high current.
Step 4: The presence of the ramp compensation will
change the dry out point, but the value found
above can be considered a good starting point.
Based on the amount of power factor correction
the value of L1 can be optimized after a few
iterations.
Gapped Ferrites, Molypermalloy, and Powdered Iron cores
are typical choices for core material. The core material
selected should have a high saturation point and
acceptable losses at the operating frequency.
One ferrite core that is suitable at around 200W is the
#4229PL00-3C8 made by Ferroxcube. This ungapped core
will require a total gap of 0.180" for this application.
OSCILLATOR COMPONENT SELECTION
The oscillator timing components can be calculated by
using the following expression:
f
R
C
OSC
T
T
=
×
1 36
.
(6)
For example:
Step 1: At 100kHz with 95% duty cycle T
OFF
= 500ns
calculate C
T
using the following formula:
C
t
I
V
pF
T
OFF
DIS
OSC
=
×
=
1000
(7)
Step 2: Calculate the required value of the timing
resistor.
R
f
C
kHz
pF
k
ChooseR
k
T
OSC
T
T
=
×
=
×
=
=
1.
1.
100
1000
13 6
14
.
.
.
(8)
CURRENT SENSE AND SLOPE (RAMP) COMPENSATION
COMPONENT SELECTION
Slope compensation in the ML4819 is provided internally.
A current equal to V
CT
/2(R18) is added to I
SENSE
A (pin 1).
this is converted to a voltage by R10, adding slope to the
sensed current through T1. The amount of slope
compensation should be at least 50% of the downslope of
the inductor current during the off time as reflected on pin
1. Note that slope compensation is a requirement only if
the inductor current is continuous and the duty cycle is
more than 50%. The highest inductor downslope is found
at the point of inductor discontinuity:
di
dt
V
V
L
V
2
V
mH
A
s
L
B
INDRY
=
=
=
μ
380
20
0 18
.
/
(9)
The downslope as reflected to the input of the PWM
comparator is given by:
S
V
V
L
R
N
PWM
B
INDRY
1
C
=
×
11
(10)
Where N
C
is the turns ratio of the current transformer (T1)
used. In general, current transformers simplify the sensing of
switch currents, especially at high power levels where the
use of sense resistors is complicated by the amount of
power they have to dissipate. Normally the primary side
of the transformer consists of a single turn and the
secondary consists of several turns of either enameled
magnet wire or insulated wire. The diameter of the ferrite
core used in this example is 0.5" (SPANG/Magnetics
F41206-TC). The rectifying diode at the output of the
current transformer can be a 1N4148 for secondary
currents up to 75mA average.
Current-sensing MOSFETs or resistive sensing can also be
used to sense the switch current. In these cases, the
sensed signal has to be amplified to the proper level
before it is applied to the ML4819.
The value of the ramp compensation (SC
PWM
) as seen at
pin 1 is:
SC
R
×
R
C
R
PWM
=
×
×
2 5
.
9
16
6
18
(11)
The required value for R
18
can therefore be found by
equating:
SC
A
S
PWM
SC
PWM
=
×
where A
SC
is the amount of slope compensation and
solving for R
18
.