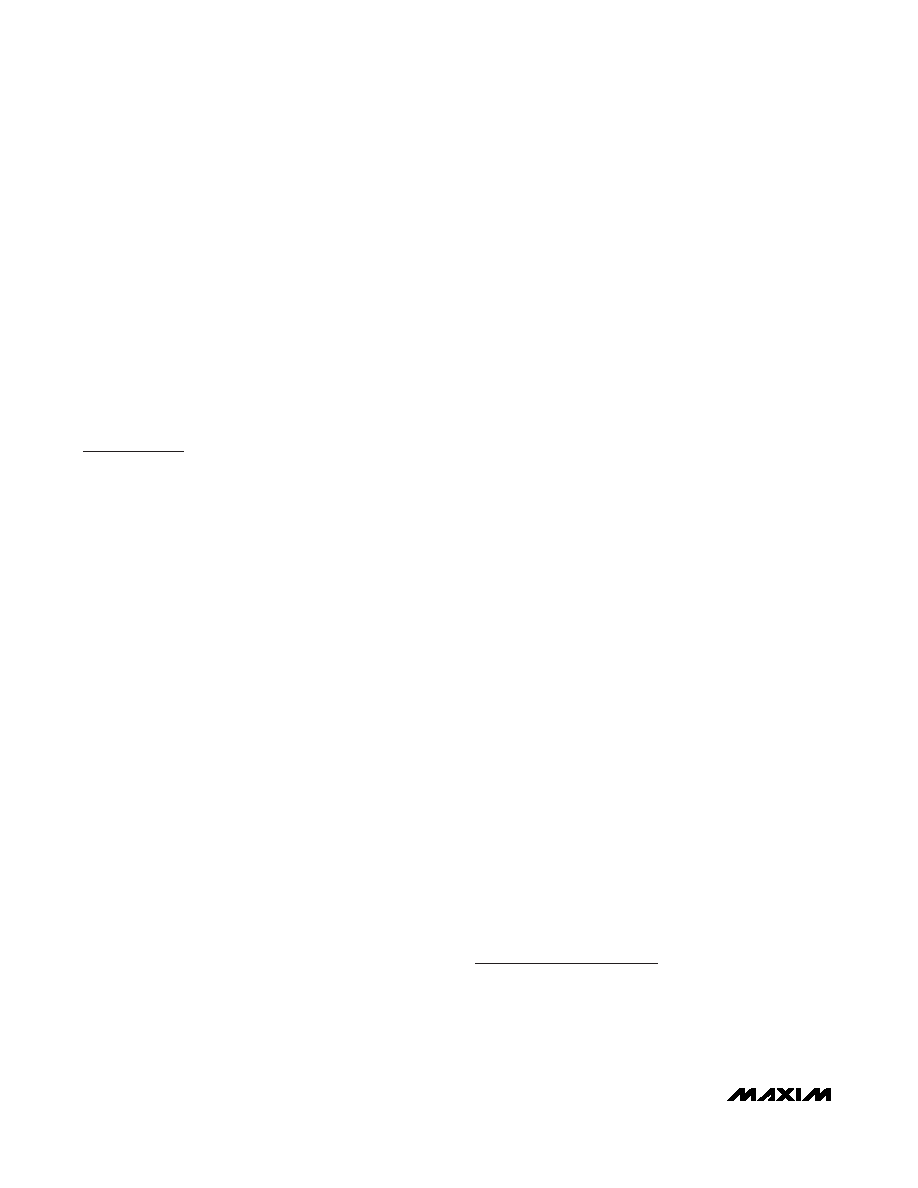
MAX13055E–MAX13058E
1.62V to 3.6V, 8-Channel, High-Speed LLT
12
______________________________________________________________________________________
Output Load Requirements
The MAX13055E–MAX13058E I/O are designed to drive
CMOS inputs. Do not load the I/O lines with a resistive
load less than 25k
Ω. Do not place an RC circuit at the
input of these devices to slow down the edges. If a
slower rise/fall time is required, refer to the MAX3000E/
MAX3001E logic-level translator data sheet.
Shutdown Mode
The MAX13055E–MAX13058E feature an enable (EN)
input that places the devices into a low-power shutdown
mode when driven low. The MAX13055E–MAX13058E
feature an automatic shutdown mode that disables the
part when VCC is unconnected or less than VL.
Applications Information
Layout Recommendations
Use standard high-speed layout practices when laying
out a board with the MAX13055E–MAX13058E. For
example, to minimize line coupling, place all other signal
lines not connected to the MAX13055E–MAX13058E at
least 1x the substrate height of the PCB away from the
input and output lines of the MAX13055E–MAX13058E.
Power-Supply Decoupling
To reduce ripple and the chance of introducing data
errors, bypass VL and VCC to ground with 0.1F ceram-
ic capacitors. Place all capacitors as close to the
power-supply inputs as possible. For full ESD protec-
tion, bypass VCC with a 1F ceramic capacitor located
as close to the VCC input as possible.
Unidirectional vs. Bidirectional
Level Translator
The MAX13055E–MAX13058E bidirectional level trans-
lators can operate as a unidirectional device to trans-
late signals without inversion. These devices provide a
small solution for unidirectional level translation without
inversion.
ESD Test Conditions
ESD performance depends on a variety of conditions.
Contact Maxim for a reliability report that documents
test setup, test methodology, and test results.
Use with External Pullup/
Pulldown Resistors
Due to the architecture of the MAX13055E–
MAX13058E, it is not recommended to use external
pullup or pulldown resistors on the bus. In certain appli-
cations, the use of external pullup or pulldown resistors
is desired to have a known bus state when there is no
active driver on the bus. The MAX13055E–MAX13058E
include internal pullup current sources that set the bus
state when the device is enabled. In shutdown mode,
the state of I/O VCC_ and I/O VL_ is dependent on the
selected part version (see the
Ordering Information/
Selector Guide).
Open-Drain Signaling
The MAX13055E–MAX13058E are designed to pass
open-drain as well as CMOS push-pull signals. When
used with open-drain signaling, the rise time is dominated
by the interaction of the internal pullup current source and
the parasitic load capacitance. The MAX13055E–
MAX13058E include internal rise-time accelerators to
speed up transitions, eliminating any need for external
pullup resistors. For applications such as I2C or 1-Wire
that require an external pullup resistor, refer to the
MAX3378E and MAX3396E data sheets.
Human Body Model
Figure 5a shows the Human Body Model and Figure 5b
shows the current waveform it generates when dis-
charged into a low impedance. This model consists of a
100pF capacitor charged to the ESD voltage of interest,
which is then discharged into the test device through a
1.5k
Ω resistor.
IEC 61000-4-2
The IEC 61000-4-2 standard covers ESD testing and per-
formance of finished equipment; it does not specifically
refer to integrated circuits. The MAX13055E–MAX13058E
help in designing equipment that meets level 4 (the high-
est level) of IEC 61000-4-2, without the need for addition-
al ESD-protection components. The major difference
between tests done using the Human Body Model and
IEC 61000-4-2 is higher peak current in IEC 61000-4-2,
because series resistance is lower in the IEC 61000-4-2
model. Hence, the ESD withstand voltage measured to
IEC 61000-4-2 is generally lower than that measured
using the Human Body Model. Figure 6a shows the IEC
61000-4-2 model and Figure 6b shows the current wave-
form for the ±8kV, IEC 61000-4-2, level 4, ESD Contact
Discharge Method.
The Air Gap Method involves approaching the device
with a charged probe. The Contact Discharge Method
connects the probe to the device before the probe is
energized.
Chip Information
PROCESS: CMOS
1-Wire is a registered trademark of Maxim Integrated Products,
Inc.