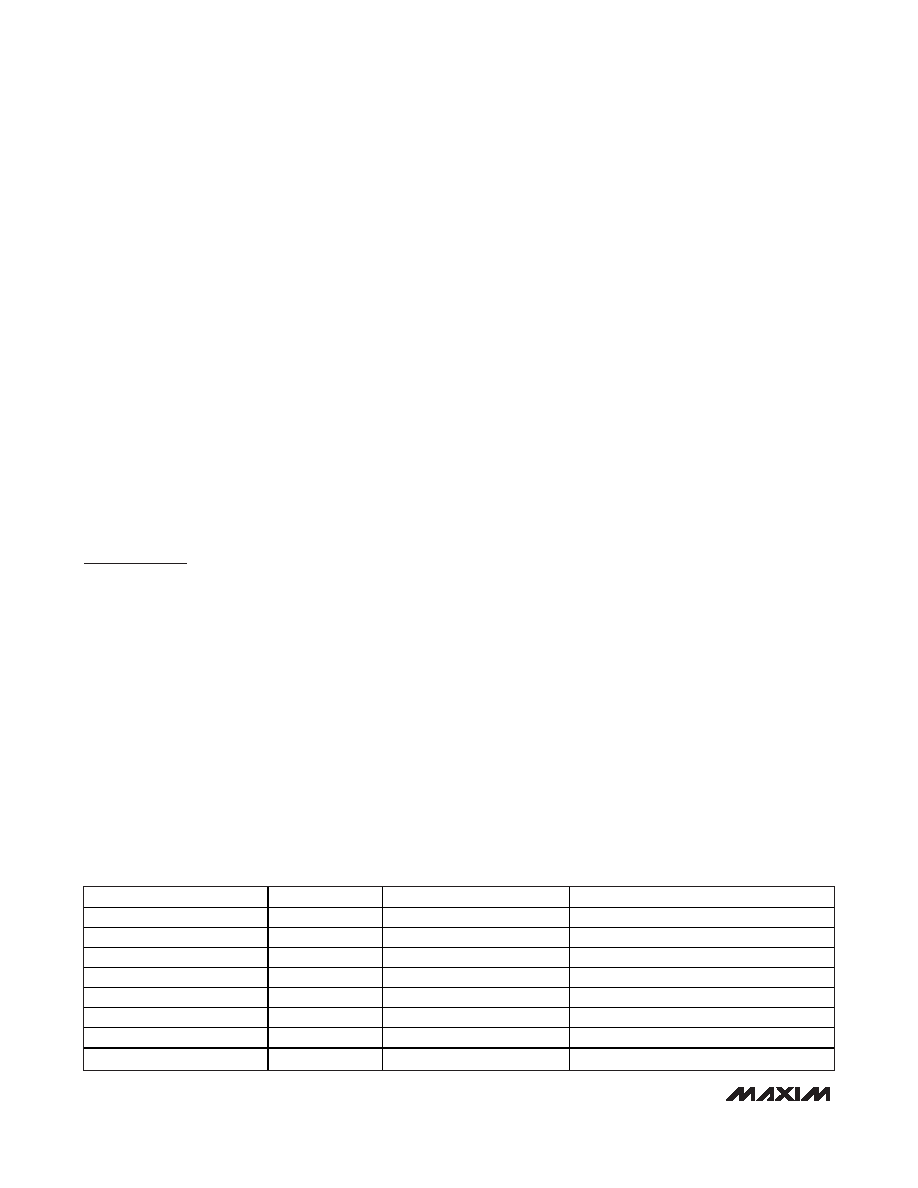
MAX1153/MAX1154
Stand-Alone, 10-Channel, 10-Bit System Monitors
with Internal Temperature Sensor and VDD Monitor
24
______________________________________________________________________________________
where:
VHIGH = sensor-diode voltage with high current flowing
(IHIGH)
VLOW = sensor-diode voltage with low current flowing
(ILOW)
q = charge of electron = 1.602 10-19 coulombs
k = Boltzman constant = 1.38 10-23 J/K
n = ideality factor (slightly greater than 1)
The temperature measurement process is fully auto-
mated in the MAX1153/MAX1154. All steps are
sequenced and executed by the MAX1153/MAX1154
each time an input channel (or an input channel pair)
configured for temperature measurement is scanned.
The resulting 10-bit, two’s complement number repre-
sents the sensor temperature in degrees Celsius, with
1 LSB = +0.5
°C.
The MAX1153/MAX1154 support both single-ended
and differential temperature measurements.
Applications Information
Setting Up the
MAX1153/MAX1154 Subsystem
The MAX1153/MAX1154 are autonomous subsystems,
requiring only initialization to scan, convert, and monitor
the voltage signals or the temperature sensors con-
nected to their input channels.
For simple applications, using any number of the input
channels and any combination of voltage/temperature
and unipolar/differential, with no interrupt generation
required, use the following intitialization procedure:
Issue a Write Global Configuration Registers com-
mand. This is a single, 5-byte write operation that
configures the input channels, enables the chan-
nels to be used, sets the sample wait time between
scans, configures the interrupt output INT, selects
the reference mode, and starts the automatic scan
mode. See the Write Global Configuration Registers
Command section, Table 2, and Tables 5–10.
Immediately after the global configuration register is
loaded, the MAX1153/MAX1154 begin to update the
current data registers. Acquire conversion data from
the MAX1153/MAX1154 by issuing a command to read
a specific channel with the Read Current Data Register
for Selected Channel command. Read all current data
register at once with the Read Current Data Registers
for All Channels command.
For more complex applications, the monitoring and
interrupt generation features of the MAX1153/MAX1154
require a second step of initialization. Each enabled
channel to be monitored requires configuration using a
Write Configuration Register for Selected Channel com-
mand. Each command is a 5-byte write that sets the
upper and lower fault thresholds, the number of faults for
an alarm before an interrupt is generated, and an aver-
age algorithm parameter if the application requires input
signal filtering.
Applications can read the current data registers and
respond to interrupts signaled by the INT output (see
the
Servicing Interrupts at INT section).
All the MAX1153/MAX1154 registers can be verified by
reading back written data, including the configuration
registers. This feature is useful for development and
testing (see Table 2).
Power-Up/Reset Defaults Summary
Setup Register Power-Up/Reset Defaults
At initial power-up or after a RESET command, the
setup register resets to 00 hex. Consequently, the
MAX1153/MAX1154 are configured as follows:
Sample wait time is 0s.
INT output is open drain and outputs an active-low
signal to signify an alarm.
Table 15. Power-Up/Reset Defaults Summary
REGISTER
BIT RANGE
POWER-UP/RESET STATE
COMMENT
Setup
B0 to B7
All 0s
See Setup Register Power-Up/Reset Defaults
Channel enable
B0 to B11
All 1s
All channels (int/ext) enabled
Input configuration
B0 to B11
All 0s
All single-ended voltage inputs
Alarm register
B0 to B23
All 0s
No alarms set
Channel configuration
B0 to B7
All 0s
Faults = 0, no averaging
Upper threshold
B0 to B9
All 1s
All upper thresholds max range
Lower threshold
B0 to B9
All 0s
All lower thresholds min range
Current data registers
B0 to B9
200hex
Set at midrange