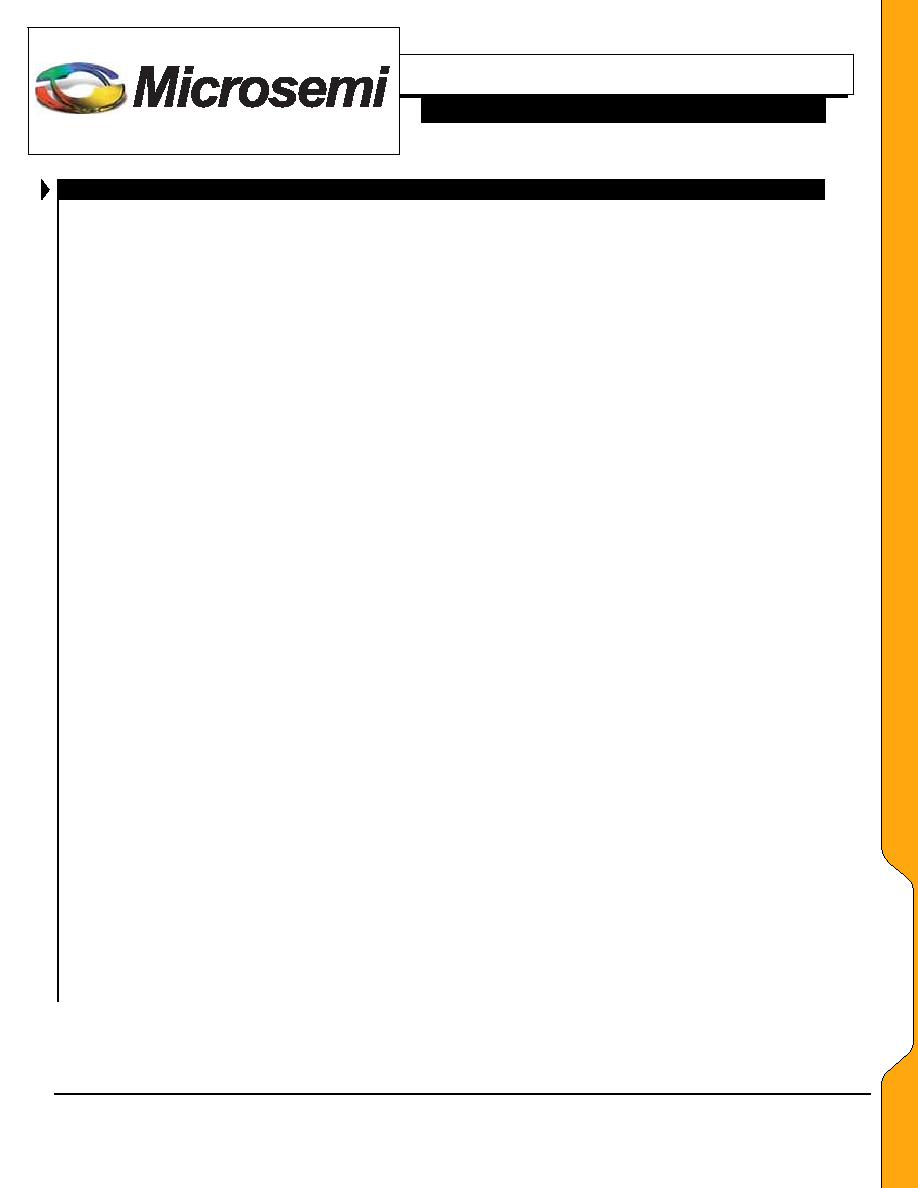
LX1705
PRODUCTION DATA SHEET
Microsemi
Analog Mixed Signal Group
11861 Western Avenue, Garden Grove, CA. 92841, 714-898-8121, Fax: 714-893-2570
Page 9
Copyright
2007
Rev. 1.2, 2007-03-20
WWW
.Microse
m
i
.CO
M
8+8W Stereo Filterless Class-D Amplifier
TM
FUNCTIONAL DESCRIPTION
FILTERLESS CLASS-D MODULATION
The LX1705 drives each output between PVDD and
PVSS using an all-NFET, bootstrapped, H-bridge driver for
each channel. High efficiency is obtained by forcing all
transistors to operate either completely on or completely off
as required for a true class-D amplifier. The entire signal
path from input to output is differential to reject any sources
of common-mode noise or distortion. Even the triangle
wave operates differentially. Filterless class-D modulation
operates such that with no input signal, the outputs switch
at the programmed clock frequency and are in-phase with
each other.
Because the two signals are identical, the
differential signal to the speaker is zero. As a direct result,
there is no requirement for a low-pass LC filter to present
high impedance at the modulation frequency. This allows a
cheaper and simpler audio amplifier to be designed. As the
input signal goes positive, the duty cycle to the positive
output increases while the duty cycle of the negative output
decreases. This produces a net positive current flow into
the load. A negative signal reduces the positive output duty
cycles and increases the negative output duty cycle. The
differential signal actually appears at twice the modulation
frequency and alternates between +PVDD, 0, and –PVDD
which allows the parasitic inductance of the load to
effectively filter the switching signal so that only the audio
band portion remains.
Because each speaker is driven by an in-phase signal, the
common mode voltage to the speaker switches at the full
PVDD amplitude at the clock frequency. This is a possible
source of EMI radiation. Typically, a ferrite bead is placed
with a small common-mode filter capacitor to reduce EMI
generation by filtering the edges of the output signals.
NOISE-FREE TURN-ON AND OFF
Noise-free turn-on and off is accomplished by carefully
sequencing the signal path when the amplifier is enabled or
disabled. Prior to turn-on, the outputs are initially both at
PVSS so there is no differential signal. The internal error
amplifier is held in a reset condition so that the internal
loop compensation components are “ready to go”. When
the outputs begin to toggle, the audio signal path is muted
for about 1.6ms. Following that time, the internal mute
signal is de-asserted and the audio input signal is allowed
to drive the pulse-width–modulator which then adjusts the
output duty cycle as necessary to drive the speaker. At
turn-off, the internal mute signal is asserted to silence the
input audio signal. The outputs continue switching in this
muted condition for about 0.6ms prior to being pulled low.
Once the outputs are forced low, the error amplifier is reset
so that the part is ready to begin a new power-up sequence.
This scheme basically limits the pop noise at turn-on or off
to be no larger than the differential offset voltage of the
error amplifier.
AC-COUPLING AND BOOTSTRAP CAPACITORS
Input AC-coupling capacitors should be used to block
any input DC and low frequency components below the
desired low frequency corner. Since the input resistance to
the LX1705 is 25k, a 20Hz low frequency corner can be
achieved with a 0.33F AC-coupling capacitor.
1F
bootstrap capacitors are required at each output to supply
the gate drive voltage for the upper level NFET in each
half-bridge.
THERMAL OVERLOAD PROTECTION
The LX1705 protects itself by monitoring its operating
temperature in two different ways. A general thermal
protection scheme monitors the overall die temperature.
Above 140°C, the amplifier gain is reduced by 6dB so that
the audio signal is still amplified, but the on-chip power
dissipation is halved.
When the die temperature goes
below 110°C, the amplifier gain is restored. Above 150°C,
the LX1705 forces all outputs to PVSS so that no power is
dissipated until the chip cools down to 110°C.
A dynamic thermal protection scheme operates by
placing temperature sensors near each of the output
devices. When a differential temperature rise of about
60°C occurs above the core die temperature, the outputs
are disabled to protect the part. This provides short circuit
protection for differential shorts across the output. Shorts
to PVDD and ground (PVSS) are not protected.
AA
PP
LL
IICC
AA
TT
IIOO
NN
SS