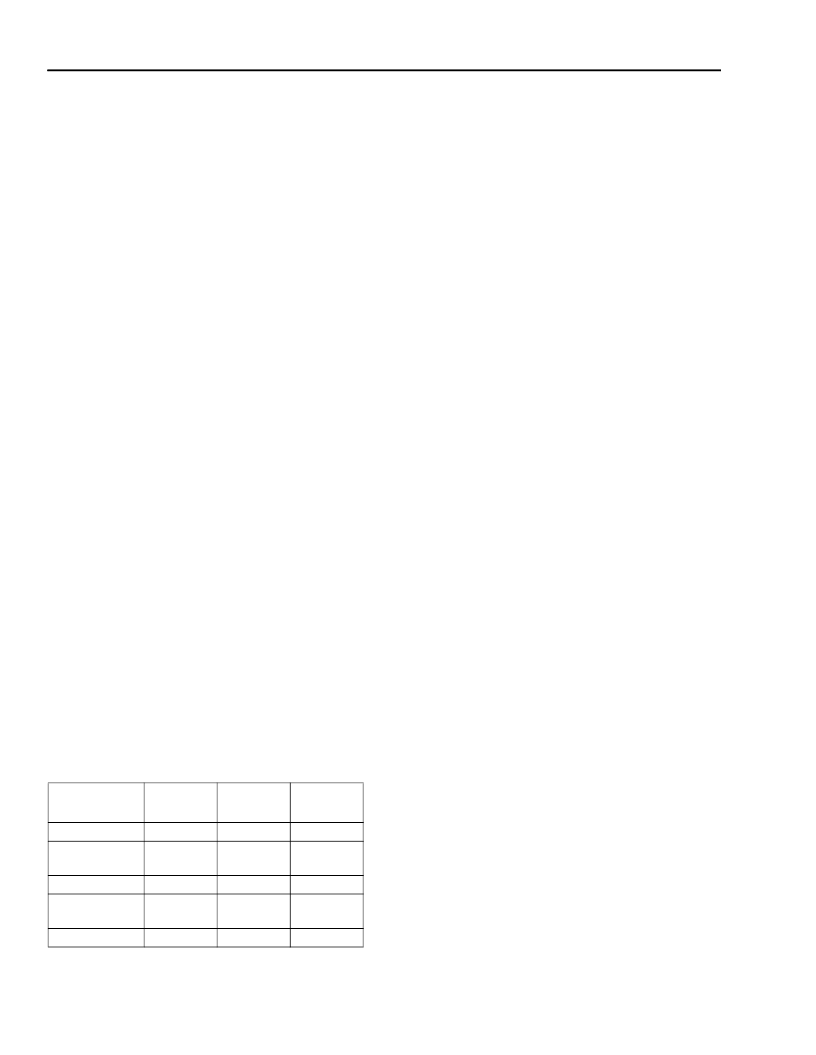
Data Sheet
September 2001
Full-Feature SLIC and Ringing Relay for TR-57 Applications
L9313 Line Interface and Line Access Circuit
30
Agere Systems Inc.
Supervision
(continued)
Make-Before-Break Operation
(continued)
On the ring side, going from the ring mode to the active
or scan mode, the pnpn will not turn off until the ring
current drops below the hold current of the pnpn device
(which is typically 500
μ
A); this is effectively zero cur-
rent for zero current turn off. This can take up to one-
half cycle of ringing to occur. With this inherent delay in
switching by the pnpn ring access switch, the break
switches will make contact before the ring access
switch breaks contact; so again, make-before-break
switching is achieved.
With the make-before-break switch, there will be a
period of time (depending on ring signal frequency but
measured in tens of microseconds) where all four
switch contacts will be on. This means that the ring
generator will be connected through the current-limited
break switches to the input of the SLIC device. Current
will be limited by the break switch current limit, and this
will not damage the SLIC. This current may, however,
cause a false glitch at the NSTAT supervision output
that will need to be digitally filtered. The board designer
should consider any ramifications of this state on the
overall system or ring generator and battery design.
The major benefit of make-before-break switching is
that it will minimize any impulse noise generated during
ringing cadence. In many cases when operating the
switch in the make-before-break mode, no special
design to switch at zero current and voltage crossing is
required. Impulse noise generation when using solid-
state relays is documented in the Impulse Noise and
the L758X Series of Solid State Switches Application
Note.
Break-Before-Make Operation
To achieve break-before-make, use the logic control
sequence device switching as shown below.
Table 16. Break-Before-Make Logic Control
Sequence Device Switching
The advantage of break-before-make operation is that
it eliminates the current spike when the ring access
relay changes state. The disadvantage is that it forces
an all-off state. Under inductive ringing loads, due to
Ldi/dt effects, it may cause a reduction in the impulse
noise performance compared to make-before-break
switching.
Protection
External Protection
An external overvoltage clamp is required to ensure
that the off-state and on-state ratings of the solid-state
break switch and solid-state ring access switch are not
exceeded. The solid-state switches in the L9313 are
constructed in a dielectrically isolated high-voltage
technology. Because of the high device-to-device isola-
tion that is inherent in the dielectric isolation, only a tip
to ground and a ring to ground clamp is required. A tip
to ring overvoltage clamp is not needed. A foldback or
crowbar type device is recommended to minimize
power across the solid-state switches under a fault
condition.
The break switches and tip return switch are con-
structed from DMOS transistors. Because the on resis-
tance of the break switches is less than the tip side ring
return switch, the break switches are physically bigger
and have a higher current handling capability. Addition-
ally, the break switches have a foldback characteristic
which enables them to survive a higher on-state volt-
age (320 V) than the tip ring return switch (130 V),
which does not have the foldback characteristic. (See
On-State Switch I-V Characteristics section.) The ring
access switch is a pnpn type device. Additionally, the
ring side will see the full power ring voltage, and the tip
side switch will see the power ringing voltage that is
attenuated by the ringing load, subscriber loop, feed
resistor, and protection resistors. Because of these dif-
ferences, the protection requirements on the tip side
are different from the protection requirements on the
ring side. Thus, it is recommended that an asymmetri-
cal (with respect to tip and ring) overvoltage protection
scheme be used.
Please contact your Agere Account Representative for
a recommended protection device.
Additionally, a series protection resistor with a fusible
characteristic or a PTC resistor is recommended to
limit current during lightning and power cross faults. A
minimum 50
is recommended in tip and ring.
The overall device protection is achieved through a
combination of the external overvoltage and overcur-
rent devices, along with the integrated thermal shut-
down feature, the integrated window comparator,
the break switch foldback characteristic, and the
dc/dynamic current-limit response of the break and tip
return switches.
State
Break
Switches
closed
open
Ring
Switches
open
open
Comment
Active/Scan
Disconnect
(all-off)
Ring
Disconnect
(all-off)
Active/Scan
—
hold
> 8 ms
—
hold
> 8 ms
—
open
open
closed
open
closed
open