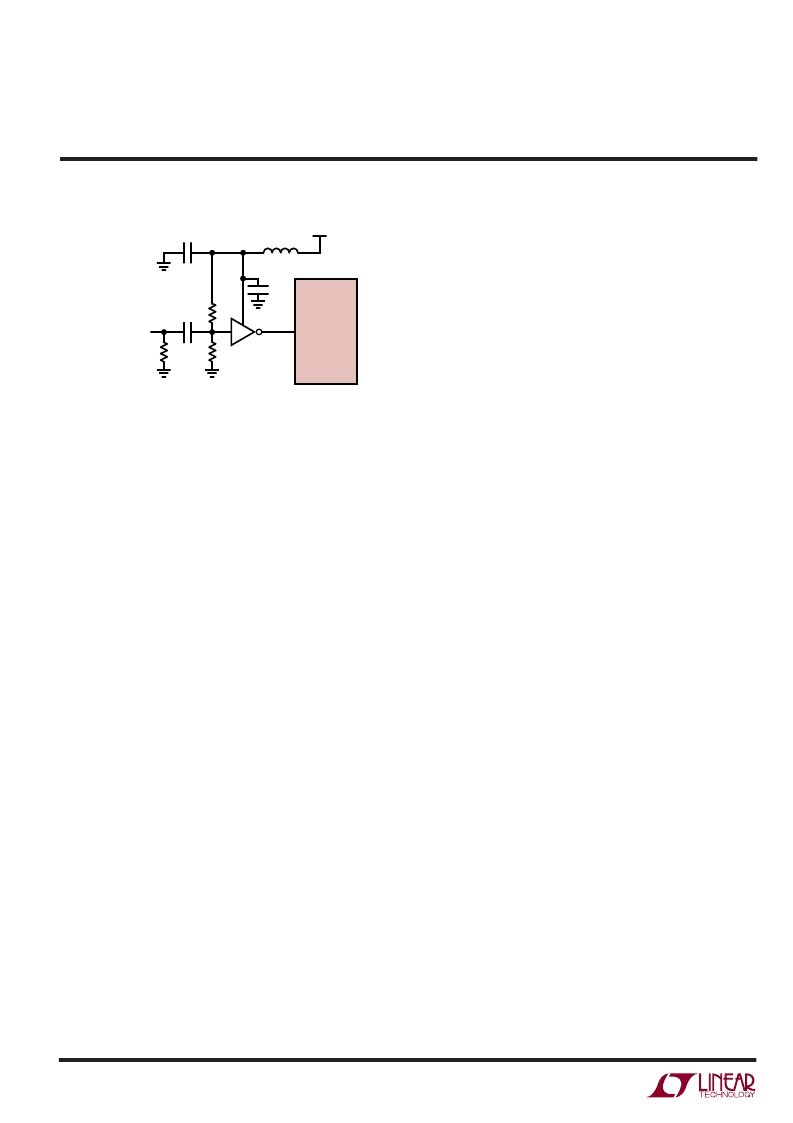
LTC2298/LTC2297/LTC2296
20
229876f
APPLICATIOU
W
U
U
The noise performance of the LTC2298/LTC2297/LTC2296
can depend on the clock signal quality as much as on the
analog input. Any noise present on the clock signal will
result in additional aperture jitter that will be RMS summed
with the inherent ADC aperture jitter.
In applications where jitter is critical, such as when digitiz-
ing high input frequencies, use as large an amplitude as
possible. Also, if the ADC is clocked with a sinusoidal
signal, filter the CLK signal to reduce wideband noise and
distortion products generated by the source.
It is recommended that CLKA and CLKB are shorted
together and driven by the same clock source. If a small
time delay is desired between when the two channels
sample the analog inputs, CLKA and CLKB can be driven
by two different signals. If this delay exceeds 1ns, the
performance of the part may degrade. CLKA and CLKB
should not be driven by asynchronous signals.
Maximum and Minimum Conversion Rates
The maximum conversion rate for the LTC2298/LTC2297/
LTC2296 is 65Msps (LTC2298), 40Msps (LTC2297), and
25Msps (LTC2296). For the ADC to operate properly, the
CLK signal should have a 50% (
±
5%) duty cycle. Each half
cycle must have at least 7.3ns (LTC2298), 11.8ns
(LTC2297), and 18.9ns (LTC2296) for the ADC internal
circuitry to have enough settling time for proper operation.
An optional clock duty cycle stabilizer circuit can be used
if the input clock has a non 50% duty cycle. This circuit
uses the rising edge of the CLK pin to sample the analog
input. The falling edge of CLK is ignored and the internal
falling edge is generated by a phase-locked loop. The
input clock duty cycle can vary from 40% to 60% and the
clock duty cycle stabilizer will maintain a constant 50%
internal duty cycle. If the clock is turned off for a long
period of time, the duty cycle stabilizer circuit will require
a hundred clock cycles for the PLL to lock onto the input
clock. To use the clock duty cycle stabilizer, the MODE pin
should be connected to 1/3V
DD
or 2/3V
DD
using external
resistors. The MODE pin controls both Channel A and
Channel B—the duty cycle stabilizer is either on of off for
both channels.
The lower limit of the LTC2298/LTC2297/LTC2296 sample
rate is determined by droop of the sample-and-hold cir-
cuits. The pipelined architecture of this ADC relies on
storing analog signals on small valued capacitors. Junc-
tion leakage will discharge the capacitors. The specified
minimum operating frequency for the LTC2298/LTC2297/
LTC2296 is 1Msps.
DIGITAL OUTPUTS
Digital Output Buffers
Figure 12 shows an equivalent circuit for a single output
buffer. Each buffer is powered by OV
DD
and OGND, iso-
lated from the ADC power and ground. The additional
N-channel transistor in the output driver allows operation
down to low voltages. The internal resistor in series with
the output makes the output appear as 50
to external
circuitry and may eliminate the need for external damping
resistors.
As with all high speed/high resolution converters, the digi-
tal output loading can affect the performance. The digital
outputs of the LTC2298/LTC2297/LTC2296 should drive a
minimal capacitive load to avoid possible interaction
Figure 11. Sinusoidal Single-Ended CLK Drive
CLK
50
0.1
μ
F
0.1
μ
F
4.7
μ
F
1k
1k
FERRITE
BEAD
CLEAN
SUPPLY
SINUSOIDAL
CLOCK
INPUT
229876 F11
NC7SVU04
LTC2298
LTC2297
LTC2296