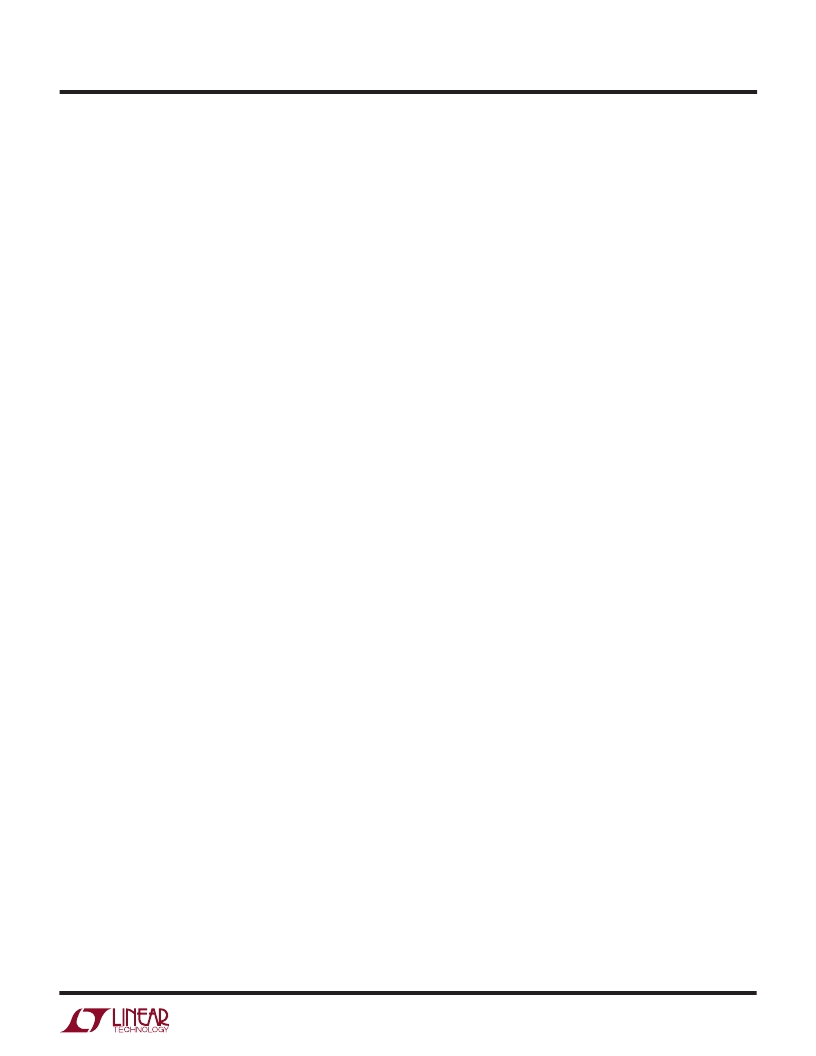
15
LTC1929/LTC1929-PG
Where f = operating frequency of each stage, C
OUT
=
output capacitance and
I
RIPPLE
= combined inductor
ripple currents.
The output ripple varies with input voltage since
I
L
is a
function of input voltage. The output ripple will be less than
50mV at max V
IN
with
I
L
= 0.4I
OUT(MAX)
/2 assuming:
C
OUT
required ESR < 4(R
SENSE
) and
C
OUT
> 1/(16f)(R
SENSE
)
The emergence of very low ESR capacitors in small,
surface mount packages makes very physically small
implementations possible. The ability to externally com-
pensate the switching regulator loop using the I
TH
pin
(OPTI-LOOP compensation) allows a much wider selec-
tion of output capacitor types. OPTI-LOOP compensation
effectively removes constraints on output capacitor ESR.
The impedance characteristics of each capacitor type are
significantly different than an ideal capacitor and therefore
require accurate modeling or bench evaluation during
design.
Manufacturers such as Nichicon, United Chemicon and
Sanyo should be considered for high performance through-
hole capacitors. The OS-CON semiconductor dielectric
capacitor available from Sanyo and the Panasonic SP
surface mount types have the lowest (ESR)(size) product
of any aluminum electrolytic at a somewhat higher price.
An additional ceramic capacitor in parallel with OS-CON
type capacitors is recommended to reduce the inductance
effects.
In surface mount applications, multiple capacitors may
have to be paralleled to meet the ESR or RMS current
handling requirements of the application. Aluminum elec-
trolytic and dry tantalum capacitors are both available in
surface mount configurations. New special polymer sur-
face mount capacitors offer very low ESR also but have
much lower capacitive density per unit volume. In the case
of tantalum, it is critical that the capacitors are surge tested
for use in switching power supplies. Several excellent
choices are the AVX TPS, AVX TPSV or the KEMET T510
series of surface mount tantalums, available in case heights
ranging from 2mm to 4mm. Other capacitor types include
Sanyo OS-CON, Nichicon PL series and Sprague 595D
series. Consult the manufacturer for other specific recom-
mendations. A combination of capacitors will often result
in maximizing performance and minimizing overall cost
and size.
INTV
CC
Regulator
An internal P-channel low dropout regulator produces 5V
at the INTV
CC
pin from the V
IN
supply pin. The INTV
CC
regulator powers the drivers and internal circuitry of the
LTC1929. The INTV
CC
pin regulator can supply up to 50mA
peak and must be bypassed to power ground with a
minimum of 4.7
μ
F tantalum or electrolytic capacitor. An
additional 1
μ
F ceramic capacitor placed very close to the
IC is recommended due to the extremely high instanta-
neous currents required by the MOSFET gate drivers.
High input voltage applications in which large MOSFETs
are being driven at high frequencies may cause the maxi-
mum junction temperature rating for the LTC1929 to be
exceeded. The supply current is dominated by the gate
charge supply current, in addition to the current drawn
from the differential amplifier output. The gate charge is
dependent on operating frequency as discussed in the
Efficiency Considerations section. The supply current can
either be supplied by the internal 5V regulator or via the
EXTV
CC
pin. When the voltage applied to the EXTV
CC
pin
is less than 4.7V, all of the INTV
CC
load current is supplied
by the internal 5V linear regulator. Power dissipation for
the IC is higher in this case by (I
IN
)(V
IN
– INTV
CC
) and
efficiency is lowered. The junction temperature can be
estimated by using the equations given in Note 1 of the
Electrical Characteristics. For example, the LTC1929 V
IN
current is limited to less than 24mA from a 24V supply:
T
J
= 70
°
C + (24mA)(24V)(95
°
C/W) = 125
°
C
Use of the EXTV
CC
pin reduces the junction temperature
to:
T
J
= 70
°
C + (24mA)(5V)(95
°
C/W) = 81.4
°
C
The input supply current should be measured while the
controller is operating in continuous mode at maximum
V
IN
and the power dissipation calculated in order to pre-
vent the maximum junction temperature from being
exceeded.
APPLICATIU
W
U
U
Powered by ICminer.com Electronic-Library Service CopyRight 2003