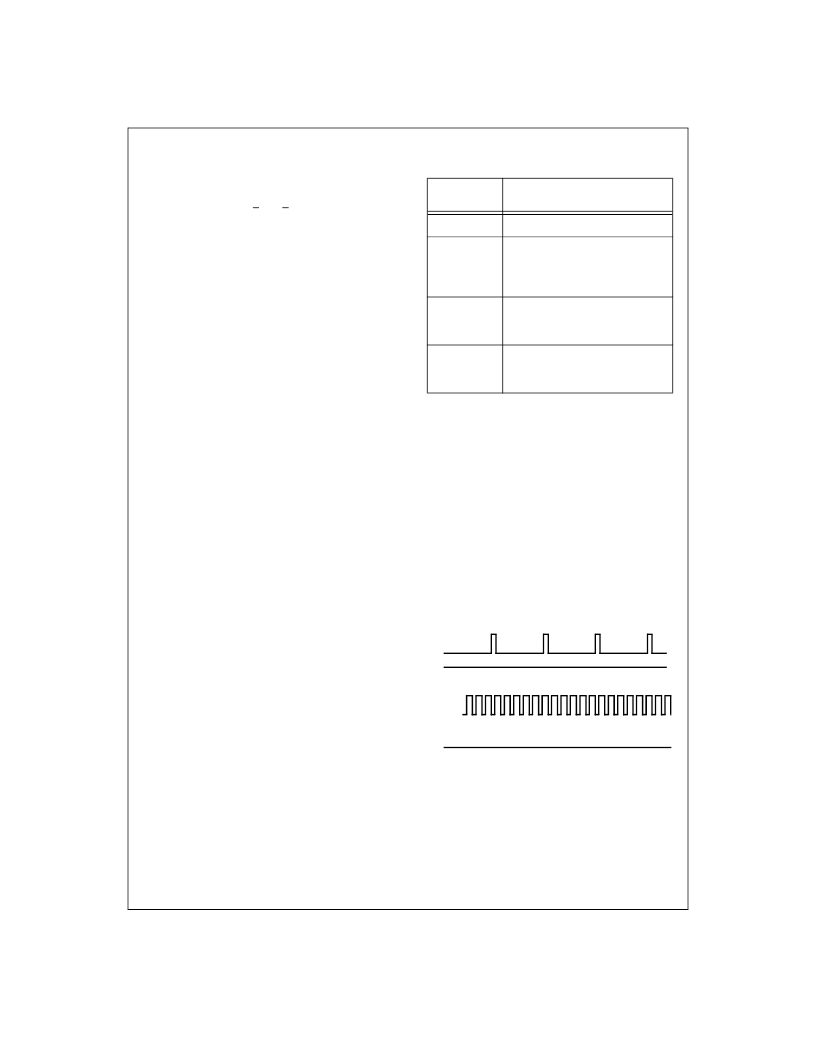
26
www.national.com
Scanning Step Size
register)
Paused until a Resume Scan signal is received, whichever
event happens first. During the hold current timeout period, the
DAC output is held at 0.110V (the hold current) for FullStep
mode, or the DAC outputs are held as they were prior to stop-
ping for the microstep mode. After the hold current timeout
period, output drivers A, B, A, and B will be deasserted.
Wait for Resume Scan signal
Wait for correct number of pixel periods to resynchronize step-
per motor with sensor timing.
25% speed forward for y full steps (1 microstep = 4*#pixels in
Scanning Step Size
register)
50% speed forward for z full steps (1 microstep = 2* #pixels in
Scanning Step Size
register).
Full speed forward (1 microstep = #pixels in
Scanning Step
Size
register), with TR pulses synchronized to same the posi-
tion on image that they would have been had scanner not
stopped.
The
Lines to Process After Pause Scan Signal
/
Lines to Dis-
card After Resume Scan Signal
register is not used in reversing
mode.
4.5 Fast Feed Step Size Register
When the motor is being moved quickly (
Paper Feed to
End
/
Paper Feed to Beginning
command or
Steps to Skip at
Start of Scan
register), the microstep period comes from this
register.
For all other motor movement, the microstep size is given in the
Scanning Step Size
register.
4.6 Stepper Motor Current Control Using PWM
There is an option to use Pulse Width Modulation of the current in
the stepper motor to increase high speed torque, optimize effi-
ciency, and allow use of a lower current, less expensive motor.
Precisely controlling the current in the motor provides several
benefits. In Full Step Mode, the motor can start moving faster and
overcome inertia by increasing the current to the motor to 100%
when it is starting from a dead stop. After a programmable num-
ber of steps, the inertia is overcome and the current can be
reduced to 70% to reduce heat in the stepper motor (allowing a
less expensive motor to be used). When stopping the stepper
motor, the current is increased to 100% for a short time to over-
come the forward momentum, then the motor is held in position
with a low-level standby current of 25%. If the motor is motionless
for more than the Hold Current Timeout period, the current goes
to 0%.
In microstepping mode, the PWM is used to approximate a sine
wave as shown in Figure 10.
The current control is accomplished by measuring the average
motor winding current through a sense resistor to ground, com-
paring it to a reference voltage, and PWMing the motor driver
transistor(s) to force the current to be equal to the reference cur-
rent. See the
Stepper Motor Current Controller Block Diagram
at the end of this document.
5.0 Scanner Support Functions
5.1 Illumination Control Block
Scanner systems require an illumination source to supply the
light to the image being scanned. This source may be white (typi-
cally a fluorescent lamp), or red, green, and/or blue LEDs. There
are four illumination modes in the LM9831:
In Illumination Mode 1, the lamp connected to the LAMP
R
pin is
controlled by the LAMP
On/Off settings in the configuration reg-
ister. The LAMP
B
output (if used) is controlled the same way. If
the lamp is supposed to be on all the time, then the On setting
should be set to a number between 0 and the value in the Line
End register, and the Off register should be set to a number
greater than the value in the Line End register. Conversely, if the
lamp is supposed to be off all the time, then the On setting should
be set to a number greater than the value in the Line End register,
and the Off register should be set to a number between 0 and the
value in the Line End register. The LAMP
G
output is a Pulse-
Width-Modulated pulse stream whose duty cycle is controlled by
the value in the PWM register (0-4095). The duty cycle is there-
fore equal to the register value/4096. The PWM counter is
clocked with the 48MHz clock so the output frequency is
48MHz/4096 = 11.7kHz. This PWM output can be used to control
the brightness of a fluorescent lamp.
In Illumination Mode 2 (which is typically used in conjunction with
1 Channel Color
), the LAMP
, LAMP
, and LAMP
outputs are
cycled through sequentially, one line at a time. An internal color
counter keeps track of the color of the line to be integrated, and
takes that color’s LAMP output high when the pixel counter
reaches the value stored in that color’s LAMP On register (Con-
figuration Registers 2C-37). If the On value is greater than the
value in the Line End register, then that lamp never turns on. That
color’s LAMP output goes low when the pixel counter reaches
that color’s Off value. If the Off value is greater than the value in
the Line End register, then the pixel counter will never reach the
Illumination
Mode
Description
0
LAMP
R
, LAMP
G
, LAMP
B
outputs = 0.
This is the power-on default.
Scanning with white light:
LAMP
and LAMP
controlled by
LAMP On/Off pointers in horizontal
pixel counter (as in Mode 3),
LAMP
G
is a PWM pulse stream
Scanning with 3 LEDs in color:
LAMP
R
turns on for Red lines
LAMP
G
turns on for Green lines
LAMP
B
turns on for Blue lines
Scanning with 3 LEDs in gray:
LAMP
R
turns on for all lines
LAMP
G
turns on for all lines
LAMP
B
turns on for all lines
Figure 19:
Illumination Modes
1
2
3
Figure 20:
Illumination Mode 1
TR
LAMP
G
LAMP
R
(LAMP
R
On < Line End, LAMP
R
Off > Line End
LAMP
B
(LAMP
B
On > Line End, LAMP
B
Off < Line End