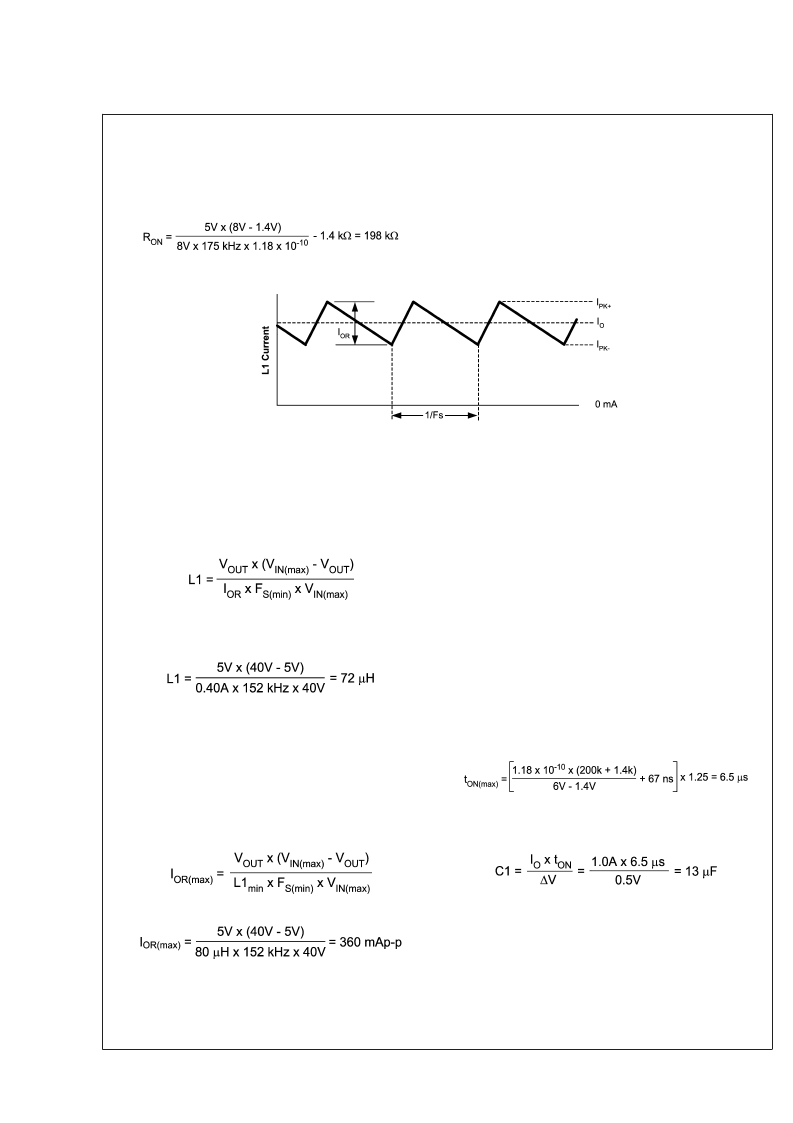
Applications Information
(Continued)
a higher efficiency, but with larger components. Generally, if
PC board space is tight, a higher frequency is better. The
resulting on-time and frequency have a
±
25% tolerance.
Using equation 7 at a nominal V
IN
of 8V,
A value of 200 k
will be used for R
, yielding a nominal
frequency of 161 kHz at V
IN
= 6V, and 203 kHz at V
IN
= 40V.
L1:
The guideline for choosing the inductor value in this
example is that it must keep the circuit’s operation in con-
tinuous conduction mode at minimum load current. This is
not a strict requirement since the LM25010 regulates cor-
rectly when in discontinuous conduction mode, although at a
lower frequency. However, to provide an initial value for L1
the above guideline will be used.
To keep the circuit in continuous conduction mode, the maxi-
mum allowed ripple current is twice the minimum load cur-
rent, or 400 mAp-p. Using this value of ripple current, the
inductor (L1) is calculated using the following:
(11)
where F
is the minimum frequency of 152 kHz (203 kHz
- 25%) at V
IN(max)
.
This provides a minimum value for L1 - the next higher
standard value (100 μH) will be used. To prevent saturation,
and possible destructive current levels, L1 must be rated for
the peak current which occurs if the current limit and maxi-
mum ripple current are reached simultaneously (I
in Figure
4). The maximum ripple amplitude is calculated by re-
arranging Equation 11 using V
, F
, and the mini-
mum inductor value, based on the manufacturer’s tolerance.
Assume, for this exercise, the inductor’s tolerance is
±
20%.
(12)
I
PK
= I
LIM
+ I
OR(max)
= 1.5A + 0.36A = 1.86A
where I
LIM
is the maximum guaranteed current limit thresh-
old. At the nominal maximum load current of 1.0A, the peak
inductor current is 1.18A.
R
:
Since it is obvious that the lower peak of the inductor
current waveform does not exceed 1.0A at maximum load
current (see Figure 5), it is not necessary to increase the
current limit threshold. Therefore R
is not needed for this
exercise. For applications where the lower peak exceeds
1.0A, see the section entitled Increasing The Current Limit
Threshold.
C1:
This capacitor limits the ripple voltage at VIN resulting
from the source impedance of the supply feeding this circuit,
and the on/off nature of the switch current into VIN. At
maximum load current, when the buck switch turns on, the
current into VIN steps up from zero to the lower peak of the
inductor current waveform (I
PK-
in Figure 5), ramps up to the
peak value (I
PK+
), then drops to zero at turn-off. The average
current into VIN during this on-time is the load current. For a
worst case calculation, C1 must supply this average current
during the maximum on-time. The maximum on-time is cal-
culated at V
IN
= 6V using Equation 5, with a 25% tolerance
added:
The voltage at VIN should not be allowed to drop below 5.5V
in order to maintain V
CC
above its UVLO.
Normally a lower value can be used for C1 since the above
calculation is a worst case calculation which assumes the
power source has a high source impedance. A quality ce-
ramic capacitor with a low ESR should be used for C1.
C2 and R3:
Since the LM25010 requires a minimum of 25
mVp-p of ripple at the FB pin for proper operation, the
required ripple at V
OUT
is increased by R1 and R2, and is
equal to:
V
RIPPLE
= 25 mVp-p x (R1 + R2)/R2 = 50 mVp-p
20172722
FIGURE 5. Inductor Current
L
www.national.com
12