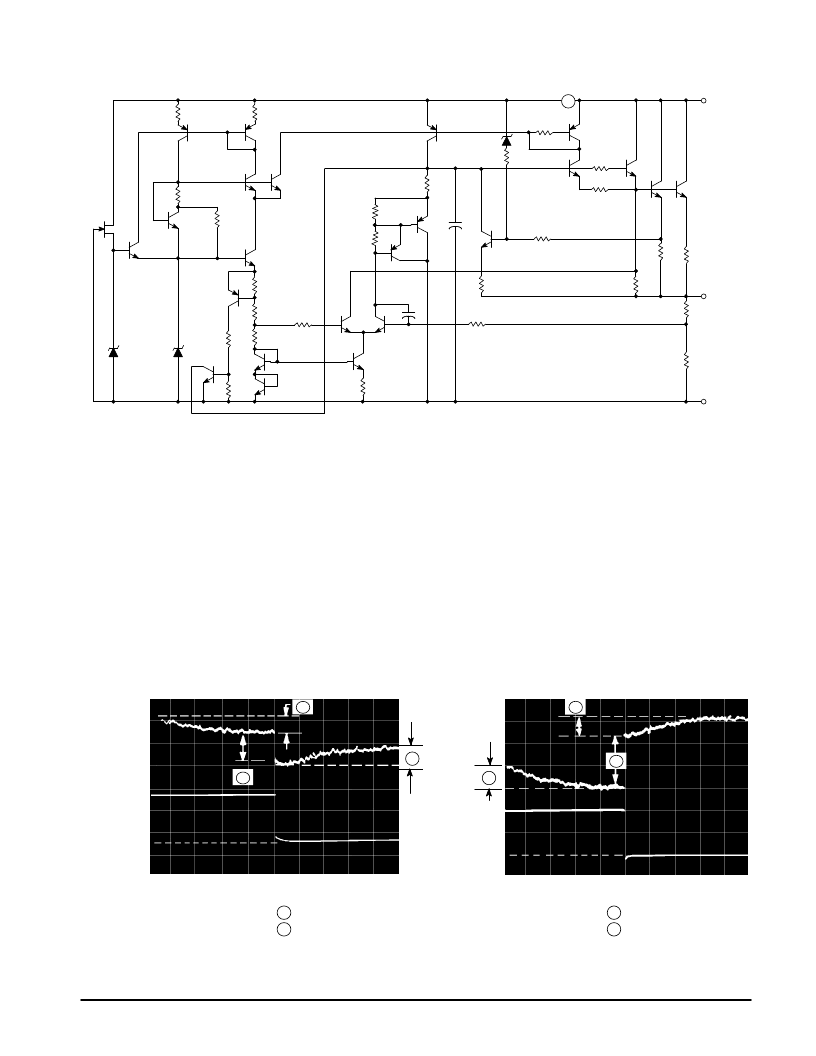
LM323, A
3
MOTOROLA ANALOG IC DEVICE DATA
1.0k
Q2
Q1
Q20
210
Q21
100
Q22
6.7V
16k
Q9
Q8
300
Q3
10k
Q4
Q5
Q10
1.0k
Q24
200
Q25
Q27
Q26
3.0k
5.6k
Q16
Q19
10pF
Q23
300
13
0.12
200
Output
50
520
Q12
2.6k
2.0k
3.9k
Q13
Q14
6.0k
Q11
Q6
Q7
40pF
Q15
2.8k
7.2k
840
1.7k
Gnd
Input
2
1.0k
6.0k
Representative Schematic Diagram
Q17
Q18
VOLTAGE REGULATOR PERFORMANCE
The performance of a voltage regulator is specified by its
immunity to changes in load, input voltage, power dissipation,
and temperature. Line and load regulation are tested with a
pulse of short duration (< 100
μ
s) and are strictly a function of
electrical gain. However, pulse widths of longer duration
(> 1.0 ms) are sufficient to affect temperature gradients
across the die. These temperature gradients can cause a
change in the output voltage, in addition to changes by line
and load regulation. Longer pulse widths and thermal
gradients make it desirable to specify thermal regulation.
Thermal regulation is defined as the change in output
voltage caused by a change in dissipated power for a
specified time, and is expressed as a percentage output
voltage change per watt. The change in dissipated power can
be caused by a change in either input voltage or the load
current. Thermal regulation is a function of IC layout and die
attach techniques, and usually occurs within 10 ms of a
change in power dissipation. After 10 ms, additional changes
in the output voltage are due to the temperature coefficient of
the device.
Figure 1 shows the line and thermal regulation response of
a typical LM323A to a 20 W input pulse. The variation of the
output voltage due to line regulation is labeled
à
and the
thermal regulation component is labeled
á
. Figure 2 shows
the load and thermal regulation response of a typical LM323A
to a 20 W load pulse. The output voltage variation due to load
regulation is labeled
à
and the thermal regulation component
is labeled
á
.
2
1
2
1
V
I
V
V
Figure 1. Line and Thermal Regulation
Figure 2. Load and Thermal Regulation
Vout = 5.0 V
Vin = 8.0 V
→
18 V
→
8.0 V
Iout = 2.0 A
= Regline = 2.4 mV
= Regtherm = 0.0015% VO/W
t, TIME (2.0 ms/DIV)
V
V
(
1
2
18 V
8.0 V
2
Vout = 5.0 V
Vin = 15 V
Iout = 0 A
→
2.0 A
→
0 A
= Regline = 5.4 mV
= Regtherm = 0.0015% VO/W
t, TIME (2.0 ms/DIV)
C
V
(
1
2
2.0
0
2