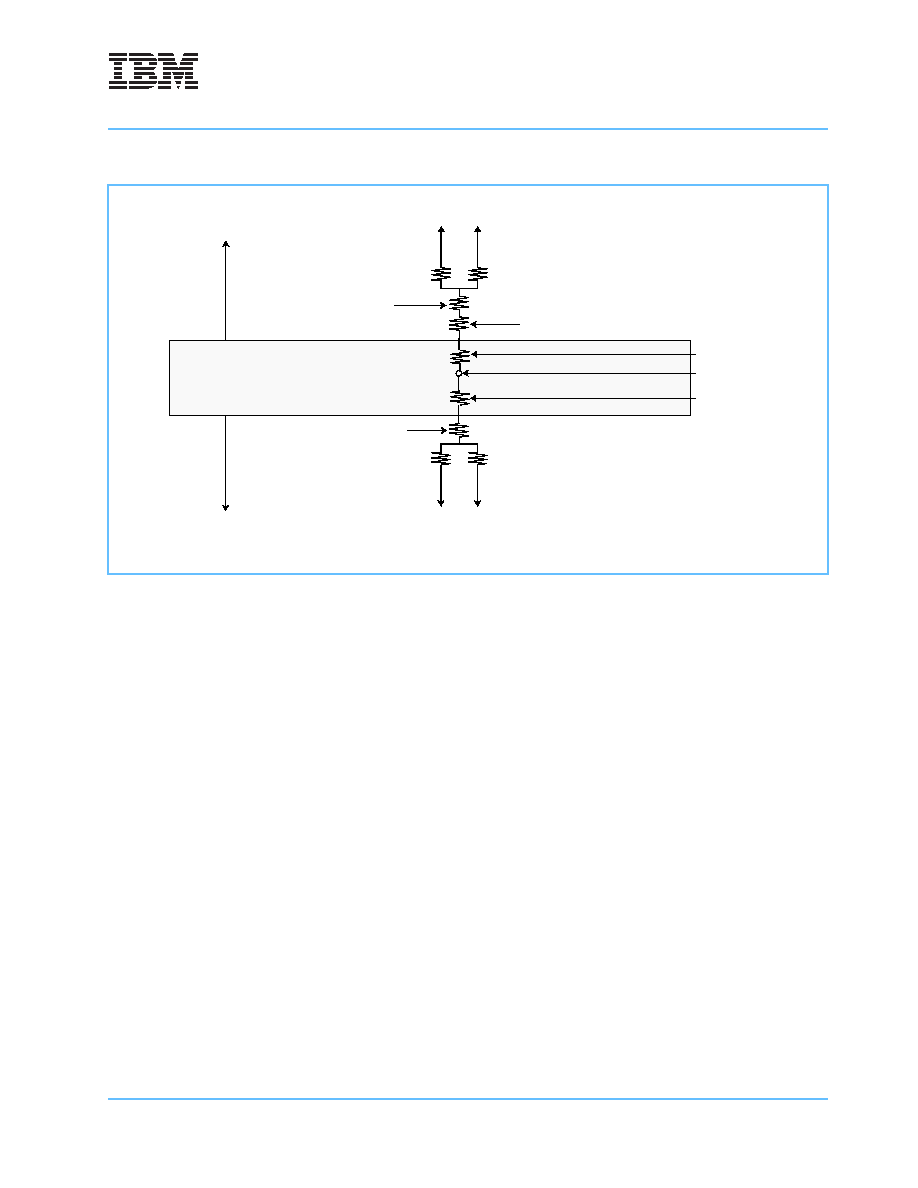
Datasheet
IBM PowerPC 750GX RISC Microprocessor
DD1.X
750GX_ds_body.fm SA14-2765-02
September 2, 2005
System Design Information
Heat generated on the active side (ball) of the chip is conducted through the silicon, then through the heat-
sink attach material (or thermal interface material), and finally to the heat sink; where it is removed by forced-
air convection. Since the silicon thermal resistance is quite small, for a first-order analysis, the temperature
drop in the silicon may be neglected. Thus, the heat sink attach material and the heat-sink conduc-
tion/convective thermal resistances are the dominant terms.
5.7.4 Adhesives and Thermal Interface Materials
A thermal interface material is required at the package die-surface-to-heat-sink interface to minimize the
thermal contact resistance. For those applications where the heat sink is attached by a spring clip mecha-
nism,
Figure 5-9 on page 66 shows an example of the thermal performance of three thin-sheet thermal-inter-
face materials (silicon, graphite/oil, floroether oil), a bare joint, and a joint with synthetic grease, as a function
of contact pressure. As shown, the performance of these thermal interface materials improves with increasing
contact pressure. The use of synthetic grease significantly reduces the interface thermal resistance. That is,
the bare joint results in a thermal resistance approximately seven times greater than the synthetic grease
joint. Customers are advised to investigate alternative thermal interface materials to ensure the most reliable,
efficient, and cost-effective thermal design.
An example of heat-sink attachment to the package by means of a spring clip to holes in the printed-circuit
on page 62. Therefore the synthetic grease offers the best thermal performance, considering the low inter-
face pressure. Of course, the selection of any thermal interface material depends on many factors—thermal
performance requirements, manufacturability, service temperature, dielectric properties, cost, and so forth.
Figure 5-8. C4 Package with Heat Sink Mounted to a Printed-Circuit Board
External Resistance Components
Internal Resistance Components
(Note the internal versus external package resistance.)
Radiation
Convection
Radiation
Convection
Custom/Application Specific
Die Junction to Case
Printed-Circuit Board
Thermal Interface Material
Die Junction to Lead
Chip Junction
(Package and Die)
(Defined by Customer Application)
Heat Sink
(Die surface)
Resistance
(Package and Leads)
(Defined by Board Design and Layout)
RJC
RJB