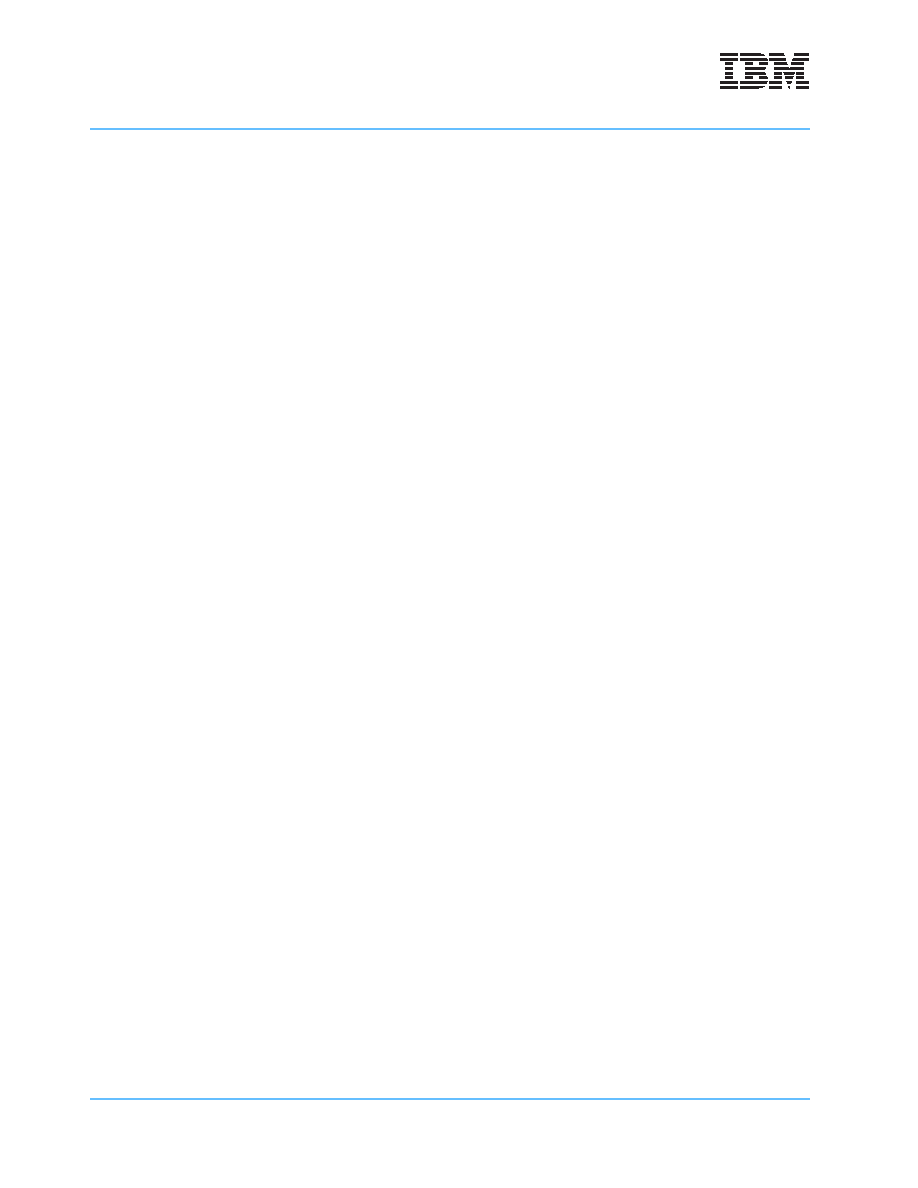
Datasheet
IBM PowerPC 750GX RISC Microprocessor
DD1.X
System Design Information
750GX_ds_body.fm SA14-2765-02
September 2, 2005
First, 750GX PD rises as TJ increases, so it is most useful to measure PD while the 750GX junction tempera-
ture is at maximum. While not specified or guaranteed, this rise in PD with TJ is typically less than 1 W per
10
°C. So regardless of other factors, the minimum cooling solution must have a maximum temperature rise of
no more than 10
°C/W. This minimum cooling solution is not generally achievable without a heat sink. A heat
sink or heat spreader of some sort must always be used in 750GX applications.
Second, due to process variations, there can be a significant variation in the PD of individual 750GX devices.
In addition, IBM will occasionally supply “downbinned” parts. These are faster parts that are shipped in place
of the speed that was ordered. For example, some parts that are marked as 800 MHz may actually run as fast
as 933 MHz. These 933 MHz parts will dissipate more power at 800 MHz than the 800 MHz parts. So power
dissipation analysis should be conducted using the fastest parts available.
Finally, regardless of methodology, IBM only supports system designs that successfully maintain the
maximum junction temperature within the datasheet limits. IBM also supports designs that rely on the
maximum PD values given in this datasheet and supply a cooling solution sufficient to dissipate that amount
of power while keeping the maximum junction temperature below the maximum TJ.
5.7.3 Internal Package Conduction Resistance
Die junction-to-case thermal resistance (primary thermal path), defined as the thermal resistance from
the die junctions to the back (exposed) surface of the die.
Die junction-to-lead thermal resistance (not normally a significant thermal path), defined as the thermal
resistance from the die junctions to the circuit board interface.
Die junction-to-ambient thermal resistance (largely dependent on customer-supplied heat sink), defined
as the sum total of all the thermally conductive components that comprise the end user's application.
Ambient is further defined as the air temperature in the immediate vicinity of the thermally conductive
components, including the pre-heat contributions of surrounding heat sources.
Figure 5-8 on page 65 is a thermal model, in schematic form, of the primary heat transfer path for a package
with an attached heat sink mounted to a printed-circuit board.