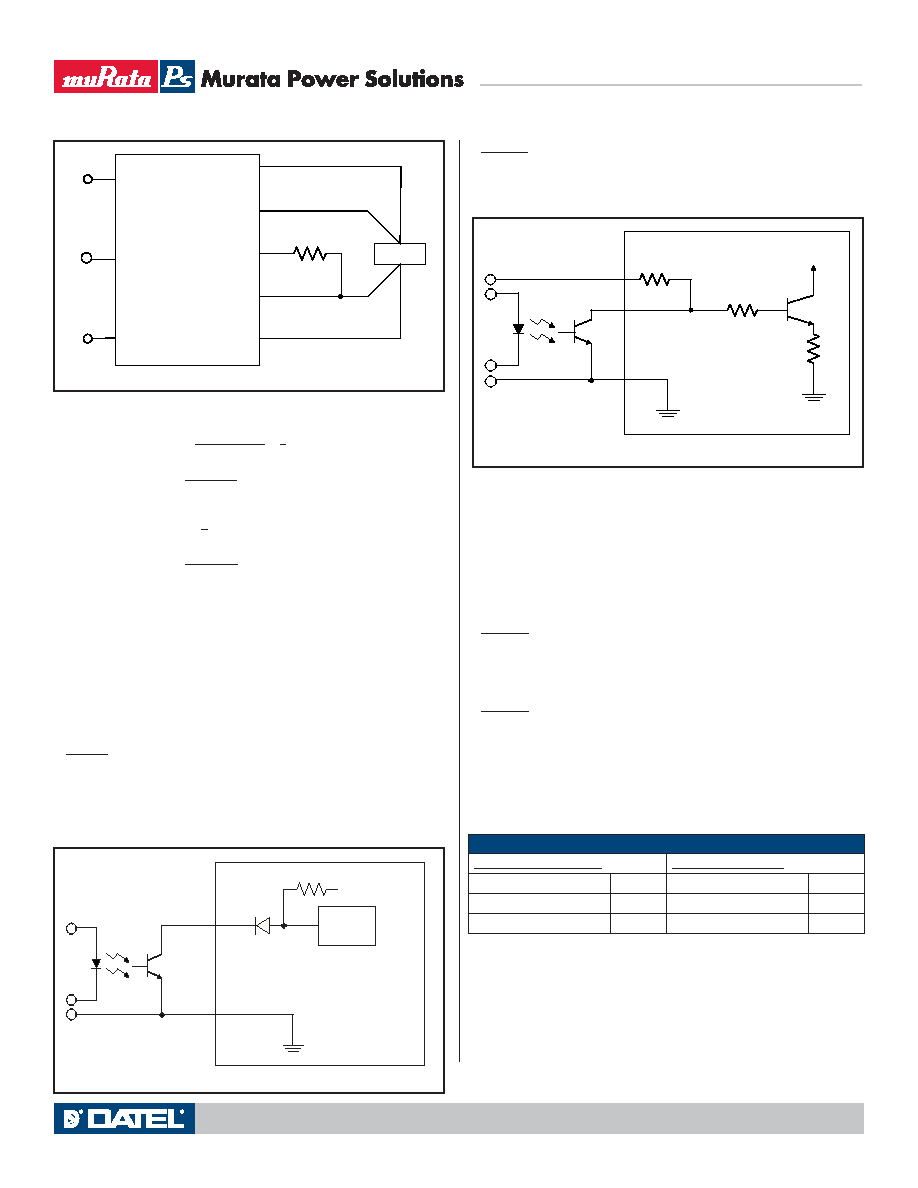
HPH-12/30-D48 Series
Isolated, 12 VOUT, 30A, Half-Brick DC/DC Converters
www.murata-ps.com
email: sales@murata-ps.com
27 May 2011
MDC_HPH-12/30-D48.A02 Page 11 of 13
Trim Equations
Where Vref = +1.225 Volts and Δ is the desired output voltage change. Note
that "Δ" is given as a small fraction, not a percentage.
A single resistor connected between Trim and +Sense will increase the output
voltage. A resistor connected between Trim and –Sense will decrease the output.
Remote On/Off Control
On the input side, a remote On/Off Control can be ordered with either polarity.
Positive: Standard models are enabled when the On/Off pin is left open or
is pulled high to +Vin with respect to –Vin. An internal bias current causes the
open pin to rise to +Vin. Some models will also turn on at lower intermediate
voltages (see Specications). Positive-polarity devices are disable when the
On/Off is grounded or brought to within a low voltage (see Specications) with
respect to –Vin.
Negative: Optional negative-polarity devices are on (enabled) when the On/
Off is grounded or brought to within a low voltage (see Specications) with
respect to –Vin. The device is off (disabled) when the On/Off is pulled high to
+Vin with respect to –Vin.
Figure 8. Trim adjustments to Decrease Output Voltage using a Fixed Resistor
Figure 9. Driving the Positive Polarity On/Off Control Pin
Figure 10. Driving the Negative Polarity On/Off Control Pin
Dynamic control of the On/Off function should be able to sink appropriate
signal current when brought low and withstand appropriate voltage when
brought high. Be aware too that there is a nite time in milliseconds (see
Specications) between the time of On/Off Control activation and stable,
regulated output. This time will vary slightly with output load type and current
and input conditions.
There are two CAUTIONs for the On/Off Control:
CAUTION: While it is possible to control the On/Off with external logic if you
carefully observe the voltage levels, the preferred circuit is either an open
drain/open collector transistor or a relay (which can thereupon be controlled by
logic).
CAUTION: Do not apply voltages to the On/Off pin when there is no input
power voltage. Otherwise the converter may be permanently damaged.
1
3
4
5
8
7
6
9
+OUTPUT
+SENSE
TRIM
-SENSE
-OUTPUT
-INPUT
ON/OFF
CONTROL
+INPUT
LOAD
R TRIM DOWN
1
3
4
ON/OFF
CONTROL
-INPUT
+INPUT
+VCC
Radj_up (in kΩ) =
-
- 2
Vnominal x (1+Δ)
1
Δ
1.225 x Δ
where Δ =
Vnominal -Vout
Vnominal
Radj_down (in kΩ) =
- 2
1
Δ
where Δ =
Vout -Vnominal
Vnominal
ON/OFF CONTROL
CONTROL
+ Vcc
-INPUT
Soldering Guidelines
Murata Power Solutions recommends the specications below when installing these
converters. These specications vary depending on the solder type. Exceeding these
specications may cause damage to the product. Your production environment may
differ; therefore please thoroughly review these guidelines with your process engineers.
Wave Solder Operations for through-hole mounted products (THMT)
For Sn/Ag/Cu based solders:
For Sn/Pb based solders:
Maximum Preheat Temperature
115° C.
Maximum Preheat Temperature
105° C.
Maximum Pot Temperature
270° C.
Maximum Pot Temperature
250° C.
Maximum Solder Dwell Time
7 seconds
Maximum Solder Dwell Time
6 seconds